AS/NZS 1802 Type 210 Mining Cables: Essential Power Solutions for Australian Gold Mining Operations
Comprehensive guide to AS/NZS 1802 Type 210 mining cables (1.1/1.1 kV) for Australian gold mines. Covers technical specifications, applications at major sites like Boddington and Super Pit, electrical parameters, and mining challenges with expert solutions.
7/3/202523 min read
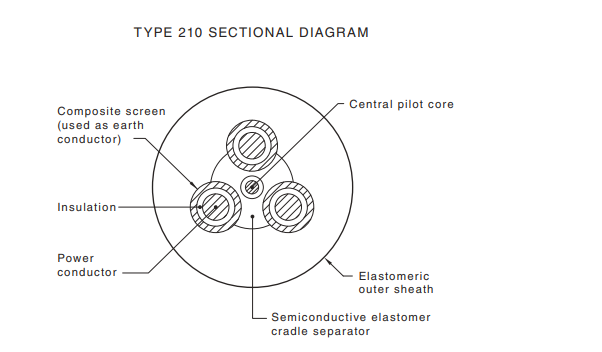
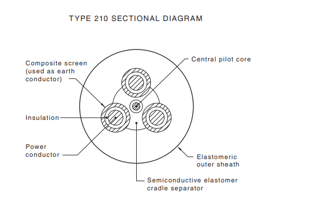
AS/NZS 1802 Type 210 Mining Cables: Essential Power Solutions for Australian Gold Mining Operations
Introduction: The Backbone of Australian Mining Power Systems
In the demanding world of Australian gold mining, where operations extend from the blazing heat of Western Australian open pits to the challenging depths of underground workings, reliable electrical infrastructure forms the absolute foundation of safe and productive mining operations. At the heart of this infrastructure lies the AS/NZS 1802 Type 210 mining cable, a specialised power transmission solution engineered specifically for the unique demands of mineral extraction environments.
The AS/NZS 1802 standard represents Australia and New Zealand's comprehensive approach to mining cable specifications, establishing rigorous requirements that ensure electrical safety, mechanical durability, and operational reliability in some of the world's most challenging industrial environments. Type 210 cables, rated at 1.1/1.1 kV, occupy a critical position within this framework, serving as the vital electrical arteries that power everything from handheld drilling equipment to massive shuttle cars and essential pumping systems.
Understanding the importance of these cables requires appreciating the extraordinary demands placed upon electrical systems in mining environments. Unlike conventional industrial applications, mining operations subject cables to extreme temperature variations, constant mechanical stress from mobile equipment, exposure to abrasive materials, and the ever-present risks associated with water ingress and chemical exposure. The Type 210 cable design addresses each of these challenges through sophisticated engineering that balances electrical performance with mechanical resilience.
The significance of proper cable selection extends far beyond mere operational efficiency. In mining environments, electrical failures can trigger catastrophic consequences, from equipment damage and production delays to serious safety incidents that put workers at risk. The AS/NZS 1802 Type 210 standard ensures that cables meet stringent safety requirements while providing the flexibility and durability necessary for the dynamic nature of mining operations.
Gold Mining Landscape Across Australia
Australia's position as one of the world's leading gold producers stems from its diverse array of mining operations, each presenting unique electrical infrastructure challenges that shape cable selection and installation requirements. The continent's gold mining industry encompasses both massive open-pit operations and sophisticated underground workings, creating a complex tapestry of electrical demands that Type 210 cables are specifically designed to address.
Major Gold Mining Operations and Their Electrical Demands
Boddington Gold Mine, Western Australia
Standing as Australia's largest gold-producing operation, the Boddington mine represents the pinnacle of open-pit mining technology and scale. Operated by Newmont Corporation, this enormous operation processes millions of tonnes of ore annually, requiring an electrical infrastructure that can support massive processing equipment, extensive conveyor systems, and the constant movement of some of the world's largest mining vehicles.
The open-pit nature of Boddington creates specific challenges for electrical systems. The mine's expansive footprint means that power distribution networks must span considerable distances while maintaining reliability across varying elevations and environmental conditions. Mobile equipment operations require flexible cable solutions that can withstand the constant vibration and movement associated with large-scale earthmoving activities. The Type 210 cable's robust construction and flexible design make it particularly well-suited for powering drilling equipment, mobile pumps, and auxiliary systems that support the mine's primary operations.
Temperature extremes present another significant challenge at Boddington. Western Australia's climate subjects electrical equipment to intense heat during summer months, while equipment operating in the pit's depths may experience different thermal conditions. The Type 210 cable's temperature rating of negative 25 degrees Celsius to 90 degrees Celsius, with emergency ratings extending to 130 degrees Celsius, provides the thermal resilience necessary for reliable operation across these varying conditions.
Cadia-Ridgeway Operations, New South Wales
The Cadia-Ridgeway complex, operated by Newcrest Mining and Newmont, represents a sophisticated combination of open-cut and underground mining operations that extract both gold and copper from the same geological formation. This dual-method approach creates particularly complex electrical infrastructure requirements, as systems must support both the large-scale equipment associated with open-pit operations and the specialised machinery required for underground extraction.
Underground operations at Cadia-Ridgeway demand electrical systems that can function reliably in confined spaces with limited ventilation, high humidity, and the constant presence of water. The Type 210 cable's earth-monitoring pilot core becomes particularly valuable in this environment, providing continuous monitoring of cable integrity and early warning of potential failures that could compromise both safety and production.
The mine's combination of gold and copper extraction also means that electrical systems must support diverse processing equipment, from traditional gold recovery circuits to copper flotation systems. This diversity requires cables capable of handling varying electrical loads while maintaining consistent performance across different operational contexts.
Kalgoorlie Super Pit (KCGM), Western Australia
Perhaps no mining operation better exemplifies the scale and complexity of modern Australian gold mining than the Kalgoorlie Super Pit. This massive open-pit operation, stretching approximately 3.5 kilometres in length, 1.5 kilometres in width, and extending to depths of 600 metres, represents one of the largest excavations on Earth. Currently operated by Northern Star Resources, the Super Pit requires an electrical infrastructure capable of supporting operations that operate continuously across multiple benches and processing facilities.
The sheer scale of the Super Pit creates unique challenges for electrical systems. Power distribution networks must span enormous distances while maintaining voltage stability and system reliability. The pit's depth means that cables must often traverse significant elevation changes, subjecting them to mechanical stresses that would overwhelm conventional electrical cables. The Type 210 cable's maximum working tension rating of 0.02 kN per square millimetre provides the mechanical strength necessary to handle these installation and operational stresses.
Mobile equipment operations at the Super Pit involve some of the world's largest mining vehicles, including massive haul trucks, draglines, and drilling rigs. These machines require flexible power connections that can accommodate their movement while providing reliable electrical supply. The Type 210 cable's symmetrical construction and flexible copper conductors make it particularly well-suited for reeling drum applications, where cables must be repeatedly wound and unwound as mobile equipment moves throughout the pit.
Telfer Gold Mine, Western Australia
The Telfer operation represents a sophisticated multi-metal mining complex that extracts gold, copper, and silver through a combination of underground and open-pit methods. This operational diversity creates electrical infrastructure requirements that span the full spectrum of mining applications, from the mobile equipment needs of open-pit operations to the specialised requirements of underground extraction systems.
Telfer's remote location in Western Australia's Pilbara region adds another layer of complexity to electrical infrastructure planning. The mine's isolation means that electrical systems must be extraordinarily reliable, as equipment failures can result in extended downtime while replacement components are transported from distant supply centres. The Type 210 cable's heavy-duty polychloroprene sheath provides exceptional resistance to oil, ultraviolet radiation, flame, and abrasion, ensuring long-term reliability in this challenging environment.
The mine's multi-metal processing requirements also create diverse electrical load profiles, as different metals require different extraction and processing techniques. Electrical systems must be capable of supporting varying power demands while maintaining stable performance across different operational modes.
Agnew Gold Mine, Western Australia
The Agnew operation represents the cutting edge of sustainable mining practices, incorporating a hybrid microgrid power supply system that combines traditional grid power with renewable energy sources. This innovative approach to mine power systems creates unique requirements for electrical infrastructure, as cables must be capable of handling power flows from multiple sources while maintaining system stability and reliability.
The underground nature of Agnew's operations places particular emphasis on electrical safety and monitoring systems. The confined spaces and limited escape routes characteristic of underground mining make electrical failures particularly dangerous, requiring cable systems with sophisticated monitoring capabilities and fail-safe design features. The Type 210 cable's central extensible earth-monitoring pilot provides continuous monitoring of cable integrity, detecting potential failures before they can compromise safety or operations.
Environmental Considerations and Operational Contexts
The diversity of Australian gold mining operations creates a complex matrix of environmental conditions that electrical systems must navigate. Surface operations face exposure to extreme weather conditions, from the scorching heat of Western Australian summers to the dust and debris generated by large-scale earthmoving activities. Underground operations present different but equally challenging conditions, including high humidity, limited ventilation, and the constant presence of water and potentially corrosive materials.
Understanding these environmental contexts is crucial for appreciating why Type 210 cables are engineered with such robust specifications. The cables must function reliably across temperature ranges that span from sub-zero conditions in underground workings to the extreme heat generated by heavy machinery operating under the Australian sun. They must resist the corrosive effects of mine water while maintaining electrical integrity in the presence of dust, debris, and mechanical stress.
The mobile nature of much mining equipment adds another dimension to these environmental challenges. Unlike fixed industrial installations, mining cables must often accommodate equipment that moves frequently, subjecting them to repeated flexing, stretching, and potential impact damage. The Type 210 cable's flexible construction and robust sheathing materials are specifically designed to handle this dynamic environment while maintaining electrical and mechanical integrity.
Type 210 Cable Applications in Mining Operations
The versatility and robust design of AS/NZS 1802 Type 210 cables make them indispensable across a wide range of mining applications, each presenting unique electrical and mechanical requirements. Understanding these applications provides insight into why Type 210 cables have become the standard choice for critical mining operations throughout Australia.
Handheld Drilling Equipment and Portable Tools
In both underground and surface mining operations, handheld drilling equipment forms the backbone of exploration, development, and production activities. These tools, ranging from lightweight rock drills to heavy-duty boring machines, require electrical connections that can accommodate constant movement, vibration, and the harsh conditions inherent to drilling operations.
The Type 210 cable's flexible copper conductor construction makes it particularly well-suited for these applications. Unlike rigid cables that can fatigue and break under repeated flexing, the stranded copper conductors maintain their electrical properties even after thousands of bending cycles. This flexibility is crucial for handheld equipment, where operators must manoeuvre tools into confined spaces and awkward positions while maintaining reliable electrical connections.
The cable's EPR (Ethylene Propylene Rubber) insulation provides additional benefits for handheld equipment applications. EPR maintains its insulating properties across the wide temperature range encountered in mining operations, from the cool conditions of underground workings to the heat generated by drilling equipment operating at high speed. The insulation's resistance to ozone, chemicals, and mechanical stress ensures that electrical safety is maintained even when cables are subject to the rough handling inevitable in mining environments.
Mobile Boring Machines and Heavy Drilling Equipment
Large-scale boring machines and drilling rigs represent some of the most demanding electrical applications in mining operations. These machines require substantial electrical power to drive hydraulic systems, rotate drill bits, and operate auxiliary equipment, while simultaneously moving across irregular terrain and operating in confined spaces.
The Type 210 cable's symmetrical construction becomes particularly important for these applications. The balanced electrical characteristics of the cable ensure that power delivery remains stable even when cables are subject to the twisting and turning motions associated with mobile drilling equipment. This symmetry also contributes to the cable's suitability for reeling drum applications, where cables must be repeatedly wound and unwound as equipment moves throughout the mine.
The cable's composite earth screen braid provides essential safety protection for these high-power applications. The screen effectively contains electromagnetic interference while providing a reliable earth path that ensures rapid fault detection and safe equipment operation. This is particularly important for mobile drilling equipment, where the combination of high electrical power and constant movement creates elevated risks of electrical faults.
Shuttle Car and Underground Transport Systems
Underground mining operations rely heavily on shuttle cars and other mobile transport systems to move ore, waste, and equipment through the confined spaces of underground workings. These vehicles require flexible electrical connections that can accommodate their movement while providing reliable power for propulsion, lighting, and auxiliary systems.
The Type 210 cable's design addresses the unique requirements of shuttle car applications through several key features. The cable's flexible construction allows it to follow the complex paths required by shuttle cars as they navigate through underground tunnels and workings. The heavy-duty polychloroprene sheath provides protection against the abrasion and impact damage that can result from contact with tunnel walls, floor surfaces, and transported materials.
The central extensible earth-monitoring pilot core provides particular value in shuttle car applications. This monitoring system continuously checks the integrity of the cable's earth path, providing early warning of damage that could compromise safety. In the confined spaces of underground workings, where escape routes may be limited, this early warning capability is essential for maintaining safe operations.
Pumping Systems and Water Management
Water management represents one of the most critical aspects of mining operations, particularly in underground workings where water ingress can pose serious safety risks and operational challenges. Pumping systems must operate reliably in wet, corrosive environments while providing the substantial power required to move large volumes of water against significant head pressure.
The Type 210 cable's water-resistant construction makes it particularly well-suited for pumping applications. The heavy-duty polychloroprene sheath provides excellent resistance to water penetration, while the cable's overall construction ensures that electrical integrity is maintained even in wet conditions. This is crucial for pumping systems, which often operate in sumps and other locations where water contact is inevitable.
The cable's temperature rating becomes important in pumping applications, as pump motors often generate significant heat during operation. The Type 210 cable's ability to operate at conductor temperatures up to 90 degrees Celsius, with emergency ratings extending to 130 degrees Celsius, ensures reliable operation even when pumps are working at maximum capacity.
Reeling Drum Applications and Mobile Equipment
Many mining operations utilise reeling drums to manage electrical connections for mobile equipment, allowing cables to be automatically wound and unwound as equipment moves throughout the mine. These applications place extraordinary demands on cable construction, as cables must maintain their electrical and mechanical properties through thousands of winding and unwinding cycles.
The Type 210 cable's symmetrical construction provides crucial advantages for reeling drum applications. The balanced electrical characteristics prevent the development of circulating currents that could cause heating and degradation during the winding process. The flexible conductor construction ensures that the cable maintains its electrical properties even after repeated bending cycles, while the robust sheath construction protects against the mechanical stresses associated with drum operations.
The cable's earth-monitoring pilot core provides additional benefits for reeling drum applications. The monitoring system can detect damage to the cable before it results in electrical faults, allowing maintenance to be performed during scheduled downtime rather than as emergency repairs. This predictive maintenance capability is particularly valuable for mobile equipment, where cable failures can result in significant operational disruptions.
Electrical and Mechanical Specifications: Engineering Excellence
The AS/NZS 1802 Type 210 cable represents sophisticated electrical engineering that balances performance requirements with practical considerations of installation, operation, and maintenance. Understanding these specifications provides insight into why Type 210 cables have become the standard choice for demanding mining applications.
Core Dimensions and Conductor Configuration
The Type 210 cable is available in two primary conductor sizes: 1.5 square millimetres and 2.5 square millimetres cross-sectional area. These sizes are specifically chosen to match the power requirements of typical mining equipment while maintaining the flexibility necessary for mobile applications. The 1.5 square millimetre version provides adequate power capacity for lighter equipment and auxiliary systems, while the 2.5 square millimetre version serves heavier equipment and applications requiring greater power transmission capability.
The conductor construction utilises tinned annealed copper strands arranged in a flexible configuration that maintains electrical properties under repeated flexing. The tinning process provides additional protection against corrosion, particularly important in mining environments where cables may be exposed to moisture and corrosive materials. The annealing process ensures that the copper retains its flexibility even after extended service, preventing the work-hardening that can cause conductor failure in mobile applications.
The conductor sheath thickness varies according to the conductor size, with 1.4 millimetres thickness for 1.5 square millimetre conductors and 1.5 millimetres thickness for 2.5 square millimetre conductors. This graduated approach ensures that smaller conductors receive adequate protection while avoiding unnecessary bulk that could compromise flexibility in larger sizes.
Insulation System and Dielectric Properties
The Type 210 cable employs a sophisticated insulation system built around EPR (Ethylene Propylene Rubber) primary insulation with a thickness of 3.0 millimetres for both conductor sizes. This insulation thickness provides excellent electrical isolation while maintaining the flexibility necessary for mobile applications. EPR was specifically chosen for its exceptional performance across the wide temperature range encountered in mining operations, maintaining its dielectric properties from negative 25 degrees Celsius to 90 degrees Celsius.
The insulation system incorporates both conductor and insulation screens to control electrical stress and prevent the development of partial discharge that could lead to insulation failure. The conductor screen consists of polyester barrier tape that provides a smooth, uniform surface for the primary insulation while controlling electrical stress concentrations. The insulation screen utilises semiconductive tape that provides a controlled path for electrical stress while maintaining the cable's overall flexibility.
This screening approach is particularly important for mining applications, where cables may be subject to mechanical stress that could create air gaps or irregularities in the insulation system. The screens ensure that electrical stress remains controlled even when cables are subjected to bending, compression, or other mechanical forces that could compromise conventional insulation systems.
Composite Earth Screen and Monitoring System
One of the most sophisticated aspects of the Type 210 cable design is its composite earth screen system, which combines electrical safety with continuous monitoring capability. The screen consists of seven strands of 0.25 millimetre copper wire arranged in a braid configuration that provides both mechanical strength and electrical conductivity.
The earth screen serves multiple functions critical to mining operations. It provides a low-impedance path for fault currents, ensuring that protective devices operate quickly to isolate faults and prevent equipment damage or personnel injury. The screen also contains electromagnetic interference generated by the cable, preventing this interference from affecting sensitive electronic equipment that may be operating in the vicinity.
The central extensible earth-monitoring pilot represents a unique feature that sets Type 210 cables apart from conventional industrial cables. This pilot consists of a separate conductor with its own EPR covering that runs through the centre of the cable assembly. The pilot provides continuous monitoring of the cable's mechanical integrity, detecting breaks in the outer sheath or damage to the earth screen before these conditions can result in electrical faults.
The monitoring system operates on the principle that any mechanical damage sufficient to compromise the cable's safety will also affect the pilot conductor. By continuously monitoring the pilot's electrical continuity, operators can detect cable damage in its early stages and schedule maintenance before failures occur. This predictive maintenance capability is particularly valuable in mining operations, where cable failures can result in significant production losses and safety risks.
Sheath Construction and Environmental Protection
The Type 210 cable's outer sheath represents the final line of defence against the harsh conditions encountered in mining operations. The sheath consists of heavy-duty polychloroprene (PCP), a synthetic rubber material specifically chosen for its exceptional resistance to oil, flame, abrasion, and ultraviolet radiation.
Polychloroprene's resistance to oil is particularly important in mining applications, where cables may be exposed to hydraulic fluids, lubricating oils, and fuel products. The material maintains its integrity even after extended exposure to these substances, preventing the degradation that could compromise cable performance or safety. The flame resistance of polychloroprene provides additional safety benefits, as it resists ignition and limits flame propagation in the event of fire.
The abrasion resistance of the polychloroprene sheath is crucial for mining applications, where cables may be dragged across rough surfaces, subjected to impact from falling rocks or equipment, or abraded by contact with moving machinery. The material's tough, resilient nature ensures that cables maintain their protective properties even after extended service in these demanding conditions.
Ultraviolet resistance becomes important for cables used in surface mining operations, where exposure to intense Australian sunlight could cause degradation of conventional sheath materials. The polychloroprene sheath maintains its properties even after extended exposure to UV radiation, ensuring long-term reliability in outdoor applications.
Thermal Performance and Temperature Ratings
The Type 210 cable's thermal performance represents a critical aspect of its design, as mining operations subject cables to extreme temperature variations that could compromise conventional electrical systems. The cable's temperature rating system provides multiple levels of protection for different operating conditions.
Normal continuous operation is rated for conductor temperatures from negative 25 degrees Celsius to 90 degrees Celsius. This range encompasses the typical conditions encountered in mining operations, from the cool conditions of underground workings to the heat generated by equipment operating under the Australian sun. The cable's insulation system maintains its electrical properties throughout this range, ensuring reliable operation across varying environmental conditions.
Emergency operation is rated for conductor temperatures up to 130 degrees Celsius, providing additional safety margin for conditions where equipment may be operating at maximum capacity or where environmental conditions exceed normal parameters. This emergency rating ensures that cables can continue to function safely even during peak demand periods or when cooling systems may be compromised.
Short-circuit conditions are accommodated by a rating of 250 degrees Celsius for five seconds, ensuring that cables can withstand the extreme temperatures generated by electrical faults without catastrophic failure. This short-circuit rating is particularly important in mining operations, where the high power levels and complex electrical systems can generate substantial fault currents.
Mechanical Properties and Installation Considerations
The Type 210 cable's mechanical properties are specifically engineered to accommodate the dynamic conditions of mining operations. The maximum working tension of 0.02 kN per square millimetre provides guidance for installation and operational stresses, ensuring that cables are not subjected to forces that could compromise their integrity.
This tension rating is particularly important for vertical installations, where cables must support their own weight plus any additional loads imposed by connected equipment. The rating also provides guidance for horizontal installations where cables may be subject to pulling forces during installation or operation.
The cable's flexible construction ensures that it can accommodate the bending and flexing associated with mobile equipment operations. The minimum bending radius specifications ensure that cables maintain their electrical and mechanical properties even when routed through complex paths or connected to equipment that moves during operation.
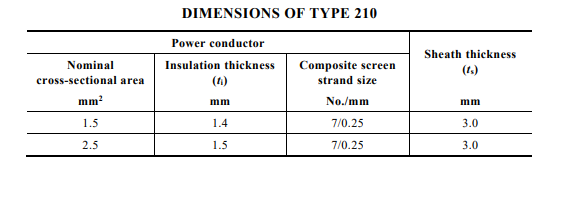
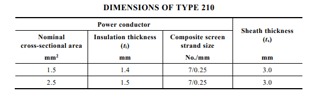
Mining Challenges and Expert Solutions
The demanding environment of Australian gold mining operations presents numerous challenges that require sophisticated solutions and deep understanding of both electrical engineering principles and practical mining operations. The Type 210 cable addresses these challenges through innovative design features and robust construction that has been proven in the harsh conditions of Australia's mining industry.
Challenge: Mechanical Stress and Equipment Mobility
Mining operations subject electrical cables to mechanical stresses that would destroy conventional industrial cables within days or weeks. Mobile equipment such as shuttle cars, drilling rigs, and pumping systems create dynamic loads that constantly flex, stretch, and compress cables. The combination of equipment movement and the rough terrain characteristic of mining sites creates mechanical stress patterns that are both severe and unpredictable.
The Type 210 cable addresses these mechanical challenges through several integrated design features. The flexible stranded copper conductor construction ensures that electrical continuity is maintained even when cables are subjected to repeated bending cycles. Unlike solid conductors that can fatigue and break under repeated stress, the stranded construction distributes mechanical loads across multiple conductor elements, preventing the concentration of stress that leads to failure.
The cable's symmetrical construction provides additional benefits for mobile applications. The balanced electrical characteristics prevent the development of circulating currents that could cause heating and degradation when cables are subjected to twisting motions. This symmetry also ensures that the cable maintains its electrical properties regardless of the direction of bending or flexing, providing consistent performance as equipment moves throughout the mine.
The heavy-duty polychloroprene sheath provides the final level of mechanical protection, resisting abrasion, impact, and compression forces that could compromise cable integrity. The sheath material's resilient properties allow it to deform under load without permanent damage, protecting the internal components from mechanical stress while maintaining the cable's overall flexibility.
Challenge: Environmental Exposure and Chemical Resistance
Mining environments expose electrical cables to a complex mixture of environmental conditions that can rapidly degrade conventional materials. Water ingress from mine dewatering systems, ground water, and process water creates corrosive conditions that can attack cable components. Chemical exposure from processing reagents, fuel products, and hydraulic fluids adds another layer of environmental challenge that cables must withstand throughout their service life.
The Type 210 cable's material selection specifically addresses these environmental challenges. The tinned copper conductor provides enhanced corrosion resistance compared to bare copper, preventing the formation of corrosion products that could increase electrical resistance or compromise mechanical integrity. The tinning process creates a protective barrier that maintains conductor performance even in wet, corrosive environments.
The EPR insulation system provides exceptional resistance to water absorption and chemical attack. Unlike some insulation materials that can swell or degrade when exposed to moisture, EPR maintains its dielectric properties and mechanical strength even after extended exposure to wet conditions. This stability is crucial for mining applications, where cables may be immersed in water or exposed to high humidity for extended periods.
The polychloroprene sheath provides comprehensive protection against chemical attack from oils, fuels, hydraulic fluids, and processing chemicals commonly encountered in mining operations. The material's resistance to these substances ensures that the cable maintains its protective properties throughout its service life, preventing the formation of cracks or degradation that could compromise safety or performance.
Challenge: Temperature Extremes and Thermal Management
Australian mining operations subject electrical systems to extreme temperature variations that can cause conventional cables to fail through thermal stress, insulation breakdown, or mechanical degradation. Surface operations in Western Australia can experience ambient temperatures exceeding 50 degrees Celsius, while equipment heat generation can raise conductor temperatures significantly higher. Underground operations may experience different thermal conditions, but the confined spaces and limited ventilation can create localised hot spots that challenge cable performance.
The Type 210 cable's thermal design addresses these challenges through careful material selection and construction techniques. The EPR insulation maintains its dielectric properties across the cable's rated temperature range, preventing the thermal degradation that could lead to insulation failure. The insulation's thermal stability ensures that electrical performance remains consistent even when cables are subjected to the temperature cycling associated with equipment operation.
The cable's temperature rating system provides multiple levels of protection for different operating conditions. The continuous rating of 90 degrees Celsius conductor temperature accommodates normal mining operations, while the emergency rating of 130 degrees Celsius provides additional safety margin for peak demand conditions. The short-circuit rating of 250 degrees Celsius ensures that cables can withstand fault conditions without catastrophic failure.
The flexible conductor construction provides additional thermal benefits by allowing heat to dissipate more effectively than solid conductor designs. The air spaces between conductor strands provide thermal expansion room that prevents the mechanical stress that could result from thermal cycling. This construction approach ensures that cables maintain their electrical and mechanical properties even when subjected to the thermal stress of continuous operation.
Challenge: Electrical Safety and Fault Detection
Mining operations create elevated electrical safety risks due to the combination of high power levels, wet conditions, and the presence of large metal structures that can create earth faults. The confined spaces of underground operations and the mobile nature of much mining equipment create additional safety challenges that require sophisticated electrical protection systems.
The Type 210 cable's earth-monitoring pilot system provides a revolutionary approach to electrical safety in mining operations. The central extensible pilot continuously monitors the integrity of the cable's earth path, detecting damage to the earth screen or sheath before these conditions can result in dangerous electrical faults. This monitoring capability transforms electrical safety from a reactive to a proactive approach, allowing maintenance to be performed before failures occur.
The composite earth screen provides comprehensive electrical protection through its low-impedance fault path and electromagnetic interference containment. The screen ensures that fault currents are rapidly conducted to protective devices, minimising the duration and severity of electrical faults. The screen also prevents electromagnetic interference from affecting sensitive electronic equipment that may be operating in the vicinity.
The cable's insulation system includes both conductor and insulation screens that control electrical stress and prevent the development of partial discharge that could lead to insulation failure. These screens ensure that electrical stress remains controlled even when cables are subjected to the mechanical stress and environmental conditions characteristic of mining operations.
Challenge: Installation and Maintenance in Difficult Environments
Mining operations present unique challenges for cable installation and maintenance, as work must often be performed in confined spaces, at height, or in the presence of active mining equipment. The remote locations of many mining operations mean that maintenance must be performed with limited resources and equipment, requiring cable systems that can be easily installed, maintained, and repaired in the field.
The Type 210 cable's design addresses these practical challenges through features that simplify installation and maintenance procedures. The cable's flexible construction allows it to be routed through complex paths without requiring special installation equipment or techniques. The symmetrical construction ensures that cables can be installed in any orientation without affecting performance, providing flexibility for installation in difficult locations.
The earth-monitoring pilot system provides predictive maintenance capability that allows maintenance to be scheduled during planned downtime rather than as emergency repairs. This capability is particularly valuable in mining operations, where unscheduled maintenance can result in significant production losses and safety risks.
The cable's robust construction ensures that it can withstand the mechanical stresses associated with installation in rough terrain and difficult conditions. The heavy-duty sheath provides protection against damage during installation, while the flexible internal construction prevents the conductor damage that could result from rough handling during installation procedures.
Frequently Asked Questions: Expert Guidance
Q1: Can Type 210 cables be used effectively for shuttle car and pump applications in underground mining operations?
Yes, Type 210 cables are exceptionally well-suited for both shuttle car and pump applications, and this suitability stems from several key design features that address the specific requirements of these demanding applications. The cable's screened copper braid provides essential electromagnetic interference containment while ensuring rapid fault detection, which is crucial for mobile equipment operating in the confined spaces of underground mines.
For shuttle car applications, the cable's flexible construction allows it to accommodate the complex routing required as vehicles navigate through underground tunnels and workings. The symmetrical construction prevents the development of circulating currents that could cause heating when cables are subjected to the twisting motions associated with mobile equipment operation. The heavy-duty polychloroprene sheath provides protection against the abrasion and impact damage that can result from contact with tunnel walls and transported materials.
Pump applications benefit from the cable's water-resistant construction and thermal rating capabilities. Underground pumping systems often operate in wet, corrosive environments where conventional cables would quickly fail. The Type 210 cable's EPR insulation and polychloroprene sheath maintain their integrity even when exposed to mine water and the chemicals commonly used in water treatment systems. The cable's temperature rating accommodates the heat generated by pump motors operating at maximum capacity, ensuring reliable operation even during peak demand periods.
The earth-monitoring pilot system provides particular value for both applications by detecting cable damage before it can result in electrical faults. In shuttle car applications, this early warning capability allows maintenance to be performed during scheduled downtime rather than as emergency repairs that could halt production. For pump applications, where failure could result in dangerous water accumulation, the monitoring system provides the early warning necessary to prevent safety hazards.
Q2: What specific protections does Type 210 cable provide against water ingress, oil exposure, and abrasion damage?
The Type 210 cable incorporates comprehensive protection against water, oil, and abrasion through its heavy-duty polychloroprene sheath and sophisticated internal construction. Understanding these protective features is crucial for mining professionals who must ensure reliable operation in environments where these hazards are constantly present.
Water protection begins with the cable's overall construction philosophy, which emphasises the prevention of water ingress rather than simply accommodating its presence. The polychloroprene sheath provides excellent resistance to water penetration, maintaining its integrity even when subjected to hydrostatic pressure or immersion conditions. The material's chemical composition ensures that it does not swell or degrade when exposed to water, preventing the formation of cracks or gaps that could allow water to reach the cable's internal components.
The cable's internal construction provides additional water protection through the use of materials that maintain their properties even when exposed to moisture. The EPR insulation does not absorb water, ensuring that the cable's dielectric properties remain stable even in wet conditions. The tinned copper conductor provides enhanced corrosion resistance compared to bare copper, preventing the formation of corrosion products that could compromise electrical performance.
Oil resistance is provided by the polychloroprene sheath's chemical composition, which maintains its integrity when exposed to hydraulic fluids, lubricating oils, fuel products, and other petroleum-based substances commonly encountered in mining operations. The material's resistance to oil absorption prevents the swelling and degradation that could compromise cable performance or safety. This oil resistance is particularly important for mobile equipment applications, where cables may be exposed to hydraulic fluid leaks or fuel spills.
Abrasion protection is achieved through the polychloroprene sheath's tough, resilient nature, which resists wear even when subjected to repeated contact with rough surfaces. The material's ability to deform under load without permanent damage allows it to absorb impact energy while protecting the cable's internal components. The sheath's thickness and material composition are specifically optimised to provide maximum abrasion resistance while maintaining the flexibility necessary for mobile applications.
Q3: How does the earth-monitoring pilot core system function, and what advantages does it provide for mining operations?
The earth-monitoring pilot core represents one of the most innovative safety features of the Type 210 cable system, providing continuous monitoring of cable integrity through a sophisticated yet simple monitoring approach. Understanding how this system functions and its benefits for mining operations is essential for appreciating the Type 210 cable's advanced safety capabilities.
The pilot core consists of a separate conductor with its own EPR covering that runs through the centre of the cable assembly, physically positioned so that any mechanical damage sufficient to compromise the cable's safety will also affect the pilot conductor. This positioning ensures that the monitoring system detects damage in its early stages, before it can progress to the point where it compromises electrical safety or operational reliability.
The monitoring system operates on the principle of electrical continuity monitoring, continuously checking the pilot conductor's resistance and detecting any changes that could indicate damage. When the cable is subjected to mechanical stress, crushing, or other forms of damage, the pilot conductor will typically show changes in resistance before the main conductors or earth screen are compromised. This early warning capability allows maintenance personnel to identify potential problems before they result in electrical faults or safety hazards.
The advantages of this monitoring system for mining operations are substantial and multifaceted. The predictive maintenance capability allows maintenance to be scheduled during planned downtime rather than as emergency repairs, reducing production losses and improving operational efficiency. In mining operations where unscheduled downtime can cost thousands of dollars per hour, this predictive capability provides significant economic benefits.
The safety advantages are equally important, particularly in underground mining operations where electrical faults can pose serious risks to personnel safety. The monitoring system provides early warning of conditions that could lead to electrical faults, allowing corrective action to be taken before dangerous conditions develop. This is particularly valuable for mobile equipment operations, where personnel may be in close proximity to electrical systems and where escape routes may be limited.
The system also provides valuable information for maintenance planning and cable management. By monitoring the pilot conductor's condition over time, maintenance personnel can identify patterns of wear or stress that may indicate problems with installation, routing, or operational procedures. This information can be used to improve installation practices, optimise cable routing, and extend cable service life.
Q4: How does Type 210 cable perform in the high-temperature conditions commonly encountered in Australian mining operations?
The Type 210 cable's thermal performance represents a critical aspect of its design, as Australian mining operations subject electrical systems to some of the most extreme temperature conditions encountered in industrial applications. Understanding the cable's thermal capabilities and how they address the specific challenges of Australian mining environments is essential for ensuring reliable operation and safety.
The cable's temperature rating system provides multiple levels of protection designed to accommodate the varying thermal conditions encountered in mining operations. The continuous operating temperature rating of negative 25 degrees
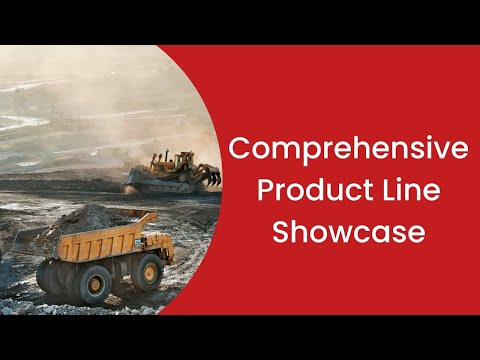