AS/NZS 1802 Type 241 Mining Cable: The Electrical Backbone of Australia's Gold Mining Operations
Discover how AS/NZS 1802 Type 241 mining cables power Australia's major gold mines including Boddington, Kalgoorlie Super Pit, and Cadia-Ridgeway. Learn about electrical parameters, applications, and mining-specific challenges.
7/3/202513 min read
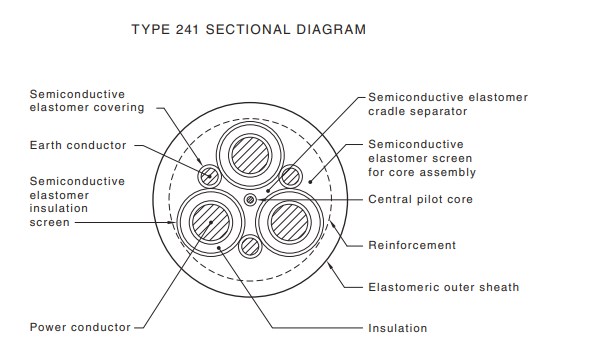
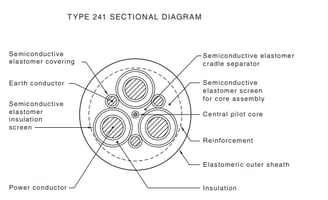
AS/NZS 1802 Type 241 Mining Cable: The Electrical Backbone of Australia's Gold Mining Operations
Introduction: The Critical Role of Specialised Mining Cables
When you think about Australia's gold mining industry, images of massive excavators, underground tunnels, and gleaming gold bars likely spring to mind. However, beneath the surface of these spectacular operations lies a complex network of electrical infrastructure that literally powers the entire enterprise. At the heart of this electrical ecosystem sits the AS/NZS 1802 Type 241 mining cable – a specialised piece of equipment that most people never see but which proves absolutely essential to keeping Australia's gold mines operational.
The AS/NZS 1802 standard represents Australia and New Zealand's comprehensive approach to mining cable specifications, establishing rigorous requirements for cables operating in the harsh underground environment. Type 241 cables, designed for voltage ranges from 1.1 kV to 11 kV, serve as the primary power distribution system for mining equipment across the continent. These cables must withstand extreme conditions that would quickly destroy ordinary electrical cables – from temperature fluctuations and mechanical stress to moisture, dust, and the constant vibration of heavy machinery.
Understanding why Type 241 cables are so critical requires appreciating the unique challenges of mining operations. Underground mines operate in environments where a single electrical failure can halt production worth millions of dollars per day, or worse, create safety hazards for workers. The cables must deliver reliable power to continuous miners that extract ore, pumps that keep tunnels dry, ventilation systems that provide breathable air, and countless other pieces of equipment that make modern mining possible.
Australia's Major Gold Mines: Where Type 241 Cables Power the Industry
Australia's position as the world's second-largest gold producer stems from several world-class mining operations, each presenting unique electrical challenges that Type 241 cables help solve. These mines showcase the diverse applications and demanding conditions where these specialised cables prove their worth.
Boddington Gold Mine in Western Australia stands as Australia's largest gold and copper producer, generating approximately 709,000 ounces of gold annually. This massive open-pit operation requires extensive electrical infrastructure to power enormous mining equipment, processing facilities, and support systems. The scale of Boddington's operations means that electrical cables must handle substantial power loads while maintaining reliability across vast distances. Type 241 cables serve as the primary power distribution system, carrying electricity from main substations to mobile equipment and fixed installations throughout the mine site.
The Kalgoorlie Super Pit, operated by Kalgoorlie Consolidated Gold Mines (KCGM), represents one of Australia's most iconic mining operations. This massive open-cut mine has produced over 50 million ounces of gold since operations began, making it a testament to sustained mining excellence. The Super Pit's electrical infrastructure spans several square kilometres, requiring cables that can withstand the constant movement of massive trucks, the vibration from blasting operations, and the extreme temperature variations of the Western Australian desert. Type 241 cables in this environment must maintain performance reliability while serving as trailing cables for mobile equipment and fixed installations for processing plants.
Cadia-Ridgeway in New South Wales combines both open-cut and underground operations, producing approximately 561,000 ounces of gold annually. This dual-mode operation presents particularly complex electrical challenges, as cables must function effectively both in the controlled environment of underground tunnels and the exposed conditions of open-pit mining. The underground sections require cables with enhanced flexibility for mobile equipment, while the surface operations demand cables that can withstand weather exposure and mechanical stress from heavy machinery.
Tropicana Gold Mine, a joint venture between AngloGold Ashanti and Regis Resources, produces around 518,000 ounces annually and demonstrates the importance of reliable electrical infrastructure in remote mining operations. Located in Western Australia's challenging desert environment, Tropicana relies heavily on electrical systems for ore processing, water management, and camp operations. Type 241 cables provide the robust power distribution necessary to maintain operations in this isolated location where equipment failures can be particularly costly and time-consuming to repair.
Western Australia's other significant gold mines – including St Ives (371,000 ounces in 2023), Agnew (245,000 ounces in 2023), Telfer (349,000 ounces in 2022-23), and Gwalia (one of Australia's deepest underground operations) – each present unique electrical challenges that Type 241 cables help address. These operations range from deep underground mines requiring flexible trailing cables to surface operations needing weather-resistant power distribution systems.
Application Scenarios: Where Type 241 Cables Prove Essential
Type 241 cables serve multiple critical functions across Australia's gold mining operations, each requiring specific electrical and mechanical characteristics. Understanding these applications helps explain why these cables incorporate such sophisticated design features and why they command premium pricing compared to standard electrical cables.
Main feeder applications represent perhaps the most critical use of Type 241 cables. These installations carry primary power from main electrical substations to various sections of mining operations. In underground mines, main feeders must traverse long distances through tunnels, often following complex routing that includes vertical shafts, horizontal drifts, and inclined passages. The cables must maintain electrical integrity while withstanding the mechanical stresses of installation and the ongoing vibration from mining equipment. Surface feeder applications require cables that can handle exposure to weather, dust, and the mechanical stress from being buried or suspended across mining areas.
Continuous miner power supply represents another crucial application where Type 241 cables excel. Continuous miners – massive machines that cut coal or ore from underground faces – require substantial electrical power delivered through cables that can flex and move as the machines operate. These trailing cable applications demand exceptional flexibility combined with robust construction, as the cables must bend repeatedly while maintaining electrical integrity. The cables must also resist damage from the sharp edges of freshly cut rock, the abrasive environment of underground tunnels, and the hydraulic fluids commonly used in mining equipment.
Pump and dewatering systems throughout mining operations rely on Type 241 cables to deliver power to equipment that keeps mines operational. Underground water management proves critical to mining safety and productivity, requiring pumps that operate continuously in challenging conditions. The cables powering these systems must withstand high moisture environments while maintaining electrical safety standards that protect both equipment and personnel.
Longwall mining systems – used in coal mining operations that often coincide with gold mining areas – require sophisticated electrical distribution networks. These systems include massive shearers that cut coal from underground faces, hydraulic roof supports that protect workers, and conveyor systems that transport material to the surface. Type 241 cables provide the flexible power distribution necessary to support these mobile mining systems as they advance through underground workings.
Transformer and substation connections represent more traditional applications where Type 241 cables provide reliable power distribution between electrical equipment. These installations require cables that can handle high voltage levels while maintaining safety margins appropriate for industrial environments. The cables must resist environmental factors that could cause electrical failures, including moisture, temperature fluctuations, and mechanical stress.
Electrical and Physical Parameters: Engineering Excellence in Cable Design
The technical specifications of Type 241 cables reflect decades of engineering refinement aimed at meeting the unique demands of mining operations. These parameters represent careful balancing of electrical performance, mechanical durability, and safety requirements that enable reliable operation in challenging environments.
Voltage classifications for Type 241 cables encompass four distinct categories, each designed for specific applications within mining electrical systems. Type 241.1 cables, rated for 1.1 kV operation, serve lower-voltage applications such as control systems, lighting circuits, and small equipment power supply. Type 241.3 cables, designed for 3.3 kV operation, handle medium-voltage applications including larger pumps, ventilation systems, and some mining equipment. Type 241.6 cables, rated for 6.6 kV operation, represent the workhorses of mining electrical systems, powering major equipment including continuous miners, large pumps, and processing equipment. Type 241.11 cables, designed for 11 kV operation, handle high-voltage applications such as main feeder circuits and connections to major electrical substations.
Conductor specifications reflect the demanding current-carrying requirements of mining operations. Available in sizes ranging from 6 mm² to 300 mm² cross-sectional area, these conductors utilise multi-strand tinned copper construction arranged in rope lay configuration. This design provides several advantages over solid conductors, including enhanced flexibility for mobile applications, improved current distribution that reduces heating effects, and better resistance to mechanical fatigue from repeated bending. The tinning process protects the copper conductors from corrosion in the moisture-rich environment of underground mines, extending cable lifespan and maintaining electrical performance over time.
Insulation systems in Type 241 cables employ ethylene propylene rubber (EPR) technology, chosen specifically for its performance in mining environments. EPR insulation provides excellent electrical properties across the temperature range encountered in mining operations, from -25°C in refrigerated areas to +90°C near equipment and processing areas. The insulation thickness varies according to voltage rating, ranging from 1.5 mm for 1.1 kV cables to 7.6 mm for 11 kV cables, providing appropriate electrical safety margins for each application. Semiconductive screens applied over the insulation cores help control electrical stress distribution, preventing electrical failures that could result from high-voltage gradients.
Earth screening systems represent a critical safety feature unique to mining cable applications. Type 241 cables incorporate three separate earth conductors that provide multiple paths for fault current, ensuring that electrical faults can be quickly detected and isolated. This earth screening system works in conjunction with semiconductive coverings to provide comprehensive electrical protection. The semiconductive covering thickness ranges from 1.0 mm to 1.8 mm depending on voltage rating, creating a controlled electrical environment that prevents dangerous electrical conditions from developing.
Sheath construction utilises heavy-duty polychloroprene (PCP) materials specifically formulated for mining applications. The sheath thickness varies from 3.8 mm for smaller cables to 9.0 mm for larger high-voltage cables, providing mechanical protection appropriate for each application. This sheath construction resists damage from abrasion, chemical exposure, and mechanical stress while maintaining flexibility necessary for mobile applications. The sheath also incorporates the semiconductive screen over the core assembly, creating an integrated protection system that maintains electrical safety even if the outer sheath suffers minor damage.
Electrical performance characteristics vary according to cable size and voltage rating, with larger conductors providing lower resistance and reactance values that improve electrical efficiency. Voltage drop calculations become critical in mining applications where cables may span considerable distances between power sources and loads. The rope lay construction of conductors and careful attention to conductor spacing help minimise inductance and capacitance effects that could impact electrical performance in high-power applications.
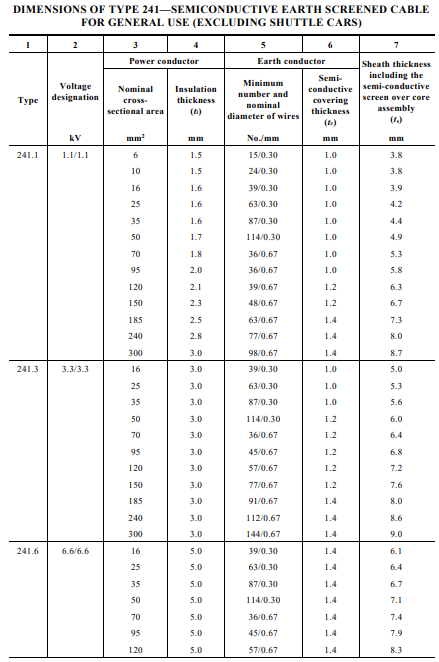
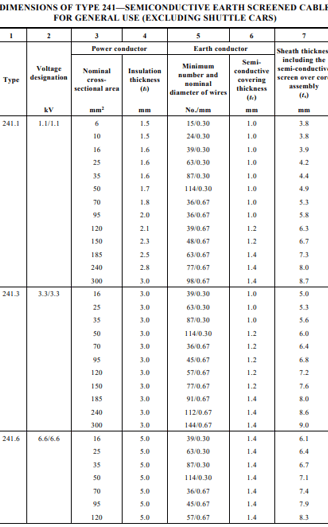

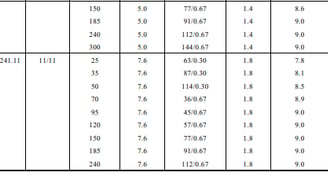
FAQ: Addressing Common Mining Cable Challenges
Mining operations present unique challenges that require specialised solutions, and Type 241 cables face questions about performance, reliability, and maintenance that reflect the demanding nature of mining environments. Understanding these common concerns helps explain the sophisticated design features incorporated into these cables and the best practices for their successful deployment.
What happens if the cable sheath becomes damaged during underground operations? This concern reflects the reality that mining operations involve sharp rocks, heavy equipment, and conditions that can damage cable sheaths despite careful installation practices. Type 241 cables address this challenge through their sophisticated earth screening system, which provides electrical protection even if the outer sheath suffers damage. The semiconductive screen over the core assembly creates a controlled electrical environment that prevents dangerous conditions from developing if the sheath is breached. This design feature allows operations to continue safely while repairs are scheduled, preventing costly production shutdowns that could result from immediate cable failures. The three separate earth conductors provide multiple paths for fault current, ensuring that electrical protection systems can detect and isolate problems before they become safety hazards.
Can Type 241 cables withstand the harsh environmental conditions found in Australian mining operations? Australia's mining environments present extreme challenges, from the desert heat of Western Australian operations to the humidity and temperature fluctuations of underground mines. Type 241 cables are specifically designed to handle temperature ranges from -25°C to +90°C, covering the full spectrum of conditions encountered in mining operations. The EPR insulation maintains its electrical properties across this temperature range, while the heavy-duty PCP sheath resists damage from moisture, oil, and chemical exposure common in mining environments. The cable construction also accommodates the mechanical stress from equipment vibration, ground movement, and the constant flexing required in mobile applications.
Are these cables flexible enough for mobile mining equipment like shuttle cars and continuous miners? Standard Type 241 cables provide semi-flexible construction suitable for many mining applications, but mobile equipment presents particularly demanding flexibility requirements. The standard cable construction balances mechanical protection with reasonable flexibility, making it suitable for installations where moderate flexing occurs. However, applications requiring tight-radius bending or frequent movement benefit from the Type 241SF (Superflex) variant, which incorporates modified conductor construction and enhanced flexibility features. This specialised version provides the tight-radius bending capability necessary for trailing cable applications while maintaining the electrical and mechanical protection features of standard Type 241 cables.
How does cable size selection impact electrical performance and installation considerations? Cable size selection involves balancing electrical performance requirements with practical installation constraints. Larger conductors provide lower electrical resistance and reactance, reducing voltage drop and improving electrical efficiency over long cable runs. However, larger cables are heavier, more expensive, and less flexible, potentially complicating installation and maintenance procedures. The selection process must consider the electrical load requirements, the distance between power source and load, the installation environment, and the mechanical requirements of the application. Mining operations often require detailed electrical calculations to optimise cable sizing for specific applications, ensuring adequate electrical performance while maintaining practical installation and maintenance capabilities.
What maintenance practices and lifespan expectations apply to Type 241 cables in mining applications? Proper maintenance practices significantly impact cable lifespan and reliability in mining operations. Regular visual inspections help identify sheath damage, mechanical stress, and environmental factors that could impact cable performance. Electrical testing, including insulation resistance measurements and earth continuity checks, helps detect developing problems before they cause failures. The sophisticated earth screening system in Type 241 cables facilitates electrical testing and fault location, making maintenance more effective. Repair procedures utilising heat-shrink sleeves and splice kits can address minor damage and extend cable life, while proper installation practices including appropriate support and protection help prevent premature failures. Cable lifespan varies significantly based on application conditions, installation quality, and maintenance practices, with well-maintained cables in suitable applications providing many years of reliable service.
Case Study: Cable Deployment in a Major Western Australian Gold Mine
To illustrate the practical application of Type 241 cables in real mining operations, consider a hypothetical but realistic scenario involving power distribution for a continuous mining operation at one of Western Australia's major gold mines. This case study demonstrates the decision-making process involved in cable selection and the practical considerations that influence successful deployment.
The Challenge: A mining operation needs to power a continuous miner working in an underground development heading approximately 800 metres from the main electrical substation. The continuous miner requires 400 kW of power at 6.6 kV, operating in a mobile configuration that requires approximately 200 metres of trailing cable. The installation must accommodate the mechanical stress of mobile operation while maintaining electrical safety standards appropriate for underground mining.
Cable Selection Process: The electrical requirements dictate a 6.6 kV cable system, indicating Type 241.6 as the appropriate voltage classification. The 400 kW load at 6.6 kV requires approximately 35 amperes of current, suggesting a conductor size of at least 50 mm² based on current-carrying capacity. However, the 800-metre distance from the substation requires consideration of voltage drop effects. Electrical calculations indicate that a 120 mm² conductor provides acceptable voltage drop performance while maintaining reasonable cable size and cost. The mobile trailing cable application requires enhanced flexibility, suggesting Type 241SF (Superflex) construction for the 200-metre trailing section.
Installation Strategy: The installation utilises Type 241.6 with 120 mm² conductors for the fixed portion of the cable run from the substation to the working area. This section employs standard Type 241 construction optimised for mechanical protection and electrical performance. The mobile trailing section utilises Type 241.6SF with 120 mm² conductors, providing enhanced flexibility for the continuous miner's movement requirements. The connection between fixed and mobile sections employs a heavy-duty connector system designed for mining applications, allowing quick disconnection when the continuous miner relocates to different working areas.
Safety and Performance Considerations: The installation incorporates proper earth screening connections throughout the system, ensuring that the three separate earth conductors provide comprehensive electrical protection. The semiconductive screen system offers additional protection against electrical faults, while the heavy-duty sheath construction provides mechanical protection appropriate for the underground environment. Electrical protection systems monitor the cable installation for ground faults, overcurrent conditions, and other electrical problems that could impact safety or equipment performance.
Operational Results: This installation demonstrates the successful application of Type 241 cables in demanding mining conditions. The cable system provides reliable power to the continuous miner while withstanding the mechanical stress of mobile operation. The sophisticated earth screening system ensures electrical safety, while the robust construction maintains performance despite the challenging underground environment. Regular maintenance and inspection procedures help identify potential problems before they impact operations, maximising productivity and maintaining safety standards.
Conclusion: The Foundation of Modern Gold Mining Operations
Type 241 cables represent far more than simple electrical components – they constitute the critical infrastructure that enables Australia's gold mining industry to operate safely, efficiently, and profitably. These sophisticated cables embody decades of engineering refinement aimed at meeting the unique challenges of mining operations, from the extreme environmental conditions of underground workings to the demanding electrical requirements of modern mining equipment.
The technical specifications of Type 241 cables – from their multi-strand tinned copper conductors to their sophisticated earth screening systems – reflect careful attention to the real-world challenges faced by mining operations. The voltage classifications spanning 1.1 kV to 11 kV provide appropriate solutions for applications ranging from control systems to main power distribution, while the range of conductor sizes accommodates everything from small equipment to massive continuous miners. The EPR insulation systems and heavy-duty PCP sheaths ensure reliable performance across the temperature ranges and environmental conditions encountered in Australian mining operations.
Australia's major gold mines, from the massive Boddington operation to the iconic Kalgoorlie Super Pit, rely on Type 241 cables to maintain the electrical infrastructure that keeps these operations running. The cables serve as main feeders carrying power across vast mining sites, trailing cables providing flexible power to mobile equipment, and distribution systems connecting the countless pieces of equipment that make modern mining possible. Without these specialised cables, the sophisticated mining operations that have made Australia a global leader in gold production would simply not be feasible.
The ongoing evolution of mining technology continues to place new demands on electrical infrastructure, and Type 241 cables must adapt to meet these challenges. As mining operations become deeper, more automated, and more electrically sophisticated, the cables that power them must provide ever-greater reliability, performance, and safety. The AS/NZS 1802 standard ensures that Type 241 cables continue to meet these evolving requirements, providing the foundation for Australia's continued success in gold mining.
For mining professionals, understanding the capabilities and limitations of Type 241 cables remains essential for designing and maintaining the electrical systems that power modern mining operations. These cables represent a critical investment in operational reliability, safety, and productivity, justifying their premium cost through the reliable performance they provide in demanding applications. As Australia's gold mining industry continues to evolve and expand, Type 241 cables will undoubtedly continue to play their essential role as the electrical backbone of these vital operations.
The story of Type 241 cables ultimately reflects the broader story of Australian mining excellence – the combination of technical innovation, rigorous standards, and practical experience that has made Australia one of the world's leading mining nations. These cables may operate largely unseen in the depths of underground mines and across the vast expanses of open-pit operations, but their reliable performance enables the extraction of the gold that contributes significantly to Australia's economy and the global gold supply. In this context, Type 241 cables represent not just electrical components, but essential infrastructure that underpins one of Australia's most important industries.
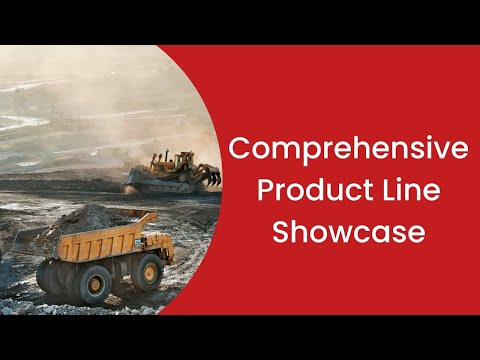