AS/NZS 2802 Type 441 Class 2 Mining Cables in Open-Cut Operations
Comprehensive guide to AS/NZS 2802 Type 441 Class 2 1.1kV mining cables for Australian open-cut mines. Covers specifications, applications at major sites like Super Pit Kalgoorlie, Mount Whaleback, electrical parameters, and mining industry FAQ solutions.
6/23/202523 min read
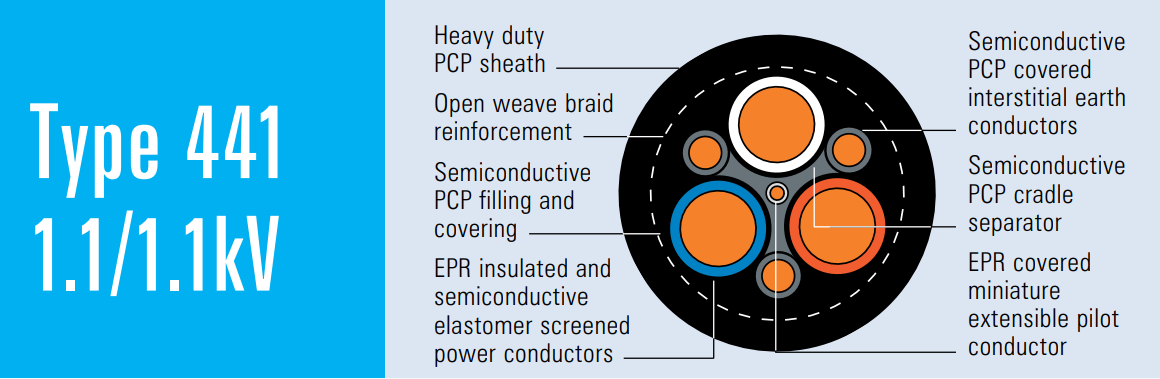

AS/NZS 2802 Type 441 Class 2 Mining Cables in Open-Cut Operations
Introduction: The Backbone of Australia's Mining Power Infrastructure
Australia's open-cut mining industry represents one of the most demanding electrical environments on Earth. From the scorching heat of Western Australia's Pilbara region to the dust-laden operations of Queensland's Bowen Basin, mining equipment operates under conditions that would destroy conventional electrical cables within days. This is where AS/NZS 2802 Type 441 Class 2 trailing and reeling cables become absolutely essential.
These specialised mining cables serve as the electrical lifelines for some of the world's largest mobile mining equipment. Unlike standard industrial cables, Type 441 Class 2 cables are engineered specifically for the brutal realities of open-cut mining operations, where draglines weighing thousands of tonnes crawl across unstable terrain, massive shovels bite into rock faces, and haul trucks the size of small buildings traverse roads that would challenge military vehicles.
The significance of robust trailing and reeling cables in open-cut mining cannot be overstated. When a cable fails on a dragline operating in a pit worth millions of dollars per day in production, the consequences extend far beyond simple equipment downtime. These failures can trigger cascade effects throughout the entire mining operation, affecting everything from production schedules to safety protocols. This is precisely why the AS/NZS 2802 Type 441 Class 2 specification exists – to provide a cable solution that can withstand the mechanical stresses, environmental challenges, and electrical demands that define Australian open-cut mining.
What sets Type 441 Class 2 cables apart from their Class 1 counterparts and conventional industrial cables is their enhanced mechanical protection and sophisticated internal architecture. The Class 2 designation indicates thicker insulation and sheath materials, providing superior protection against the crushing forces, abrasion, and impact damage that are inevitable in surface mining applications. These cables incorporate advanced features like semiconductive cradle separators and central pilot conductors that not only improve mechanical resilience but also enable sophisticated monitoring and protection systems that are crucial for modern mining safety standards.
Australia's Mining Giants: Where Type 441 Cables Power the Nation's Economy
Understanding the application environment for Type 441 Class 2 cables requires examining the scale and complexity of Australia's major open-cut mining operations. These sites represent some of the most challenging electrical environments in the industrial world, where cables must perform reliably under conditions that combine extreme mechanical stress with harsh environmental factors.
The Super Pit: Kalgoorlie's Golden Giant
The Super Pit, officially known as the Fimiston Open Pit, stands as one of Australia's most iconic mining operations and serves as an excellent example of where Type 441 Class 2 cables prove their worth. Stretching approximately 3.5 kilometres in length, 1.5 kilometres in width, and plunging to depths of 600 to 700 metres, this massive excavation represents one of the largest gold mining operations in the Southern Hemisphere.
What makes the Super Pit particularly challenging from an electrical perspective is the combination of its enormous scale and the precision required for gold extraction. The operation employs multiple large-scale draglines and electric shovels that must manoeuvre with remarkable precision despite their massive size. These machines require continuous, reliable electrical power to maintain the precise operational parameters necessary for efficient gold extraction.
The electrical supply demands at the Super Pit are staggering. The primary draglines alone can draw several megawatts of power during peak operation, requiring cables that can handle not only the electrical load but also the mechanical stresses of constant repositioning across unstable ground. The pit's depth creates additional challenges, as cables must be capable of supporting their own weight over vertical runs that can exceed 600 metres while maintaining electrical integrity and mechanical strength.
The tourist significance of the Super Pit adds another layer of complexity to its operations. As one of Western Australia's premier tourist attractions, the operation must maintain the highest safety standards while continuing full-scale production. This dual requirement makes cable reliability absolutely critical, as any electrical failure could impact both production schedules and public safety protocols.
Mount Whaleback: The Iron Ore Powerhouse
Mount Whaleback in the Pilbara region represents perhaps the most extreme example of where Type 441 Class 2 cables demonstrate their capabilities. As the world's largest iron ore open-pit mine, Mount Whaleback presents electrical challenges that are quite literally unprecedented in scale. The operation moves hundreds of millions of tonnes of material annually, requiring electrical infrastructure that can support some of the largest mobile mining equipment ever constructed.
The environmental conditions at Mount Whaleback are particularly demanding for electrical equipment. The Pilbara's extreme heat, combined with the abrasive nature of iron ore dust, creates conditions that rapidly degrade conventional electrical cables. Temperatures regularly exceed 45°C during summer months, while the fine iron ore dust penetrates even the smallest gaps in cable construction, potentially causing electrical faults through conductive contamination.
The scale of equipment at Mount Whaleback requires cables with exceptional current-carrying capacity and mechanical strength. The largest draglines and shovels operating at the site represent some of the most powerful mobile electrical loads in the world, requiring cables that can deliver stable power while withstanding the mechanical stresses of operation on surfaces that shift and settle as mining progresses.
Mount Arthur: Coal Mining Excellence in New South Wales
Mount Arthur, located near Muswellbrook in New South Wales, represents Australia's largest coal open-cut operation in the state, processing approximately 20 million tonnes per annum. The operation presents unique challenges for electrical infrastructure due to the specific requirements of coal extraction and the environmental conditions of the Hunter Valley region.
Coal mining operations require particularly stringent electrical safety standards due to the potential presence of methane and other combustible gases. This makes the flame-resistant properties of Type 441 Class 2 cables especially important, as any electrical fault could potentially trigger dangerous situations. The cables' compliance with AS/NZS flame resistance standards becomes a critical safety feature rather than simply a regulatory requirement.
The Hunter Valley's climate presents its own challenges for electrical equipment. The region experiences significant temperature variations, high humidity during certain seasons, and occasional severe weather events. Type 441 Class 2 cables must maintain their electrical and mechanical properties across this wide range of environmental conditions while supporting continuous mining operations.
Saraji and Hail Creek: Coking Coal Operations in Queensland's Bowen Basin
The coking coal operations at Saraji and Hail Creek in Queensland's Bowen Basin demonstrate the versatility of Type 441 Class 2 cables across different mining environments. Saraji, processing approximately 10 million tonnes per annum, and Hail Creek, with its 5.5 million tonnes per annum capacity, both present unique electrical challenges related to coking coal extraction.
Hail Creek's particular challenge with methane emissions adds another layer of complexity to electrical system design. The presence of methane requires electrical equipment that not only meets standard flame resistance requirements but also incorporates additional safety features to prevent ignition sources. The central pilot conductor in Type 441 Class 2 cables becomes especially valuable in these environments, as it enables continuous monitoring of cable integrity and rapid detection of potential fault conditions that could create ignition risks.
The Bowen Basin's tropical climate, with its high humidity and seasonal rainfall, creates additional challenges for electrical infrastructure. Cables must maintain their insulation properties in conditions where moisture ingress can rapidly lead to electrical failures. The advanced sheath materials and construction techniques used in Type 441 Class 2 cables provide the necessary protection against these environmental challenges.
Application Scenarios: Where Type 441 Class 2 Cables Excel
Understanding the specific application scenarios where Type 441 Class 2 cables provide their greatest value requires examining the unique electrical and mechanical requirements of different mining operations. These cables are not simply larger versions of industrial cables; they represent specialised solutions designed for specific challenges that arise in open-cut mining environments.
Trailing Applications in Mobile Equipment
The primary application for Type 441 Class 2 cables lies in trailing applications, where the cable must follow mobile equipment as it moves across the mining site. This application presents several unique challenges that conventional cables simply cannot handle. The cable must be capable of being dragged across surfaces that range from smooth haul roads to rough, uneven terrain created by blasting and excavation activities.
Draglines represent perhaps the most demanding trailing application for these cables. These massive machines, which can weigh several thousand tonnes, move continuously across the mining site as they strip overburden and extract ore. The trailing cable must not only supply the electrical power required for the dragline's operation but also withstand the mechanical stresses created by the machine's movement across unstable ground.
Electric shovels present different but equally challenging trailing requirements. These machines operate in a more stationary manner than draglines but require cables that can handle the extreme electrical loads created during digging operations. The sudden load changes that occur when a shovel bites into rock or encounters unexpected geological formations create electrical transients that can damage conventional cables.
Mobile crushing and screening plants represent an emerging application area for Type 441 Class 2 cables. These relocatable processing facilities require electrical connections that can be quickly established and broken down as the plant moves to new locations within the mining site. The cables must be robust enough to handle repeated setup and breakdown cycles while maintaining electrical integrity.
Reeling Applications for Extended Reach Operations
Reeling applications present their own unique set of challenges for mining cables. In these applications, the cable is wound onto a reel system that allows for controlled deployment and retrieval as equipment moves or as operational requirements change. The cable must be designed to handle the mechanical stresses of repeated winding and unwinding while maintaining its electrical properties.
The reeling process subjects cables to particular types of mechanical stress that do not occur in trailing applications. The repeated bending and flexing that occurs as the cable is wound onto and unwound from the reel can cause fatigue in conventional cable constructions. Type 441 Class 2 cables incorporate specific design features, including the semiconductive cradle separator, that help distribute these stresses and prevent premature failure.
Long-run reeling systems, which may deploy several hundred metres of cable, present additional challenges related to cable weight and mechanical support. The cable must be designed to support its own weight over extended lengths while maintaining electrical conductivity and insulation integrity. The textile braid reinforcement incorporated into Type 441 Class 2 cables provides the necessary tensile strength for these applications.
Enhanced Crush Resistance Through Advanced Design
One of the most significant advantages of Type 441 Class 2 cables lies in their enhanced crush resistance, achieved through the incorporation of a semiconductive cradle separator and advanced core geometry. This design feature addresses one of the most common failure modes in mining cable applications: mechanical damage caused by crushing or impact loading.
The semiconductive cradle separator serves multiple functions within the cable construction. First, it provides mechanical support for the power conductors, helping to maintain their geometry under load and preventing deformation that could lead to insulation failure. Second, the semiconductive material helps distribute electrical stress within the cable, reducing the likelihood of electrical breakdown under high-voltage conditions.
The cradle design also contributes to the cable's ability to withstand the dynamic loading conditions that are common in mining applications. When a cable is run over by heavy equipment or subjected to impact loading from falling rocks or debris, the cradle helps distribute the load across the entire cable cross-section rather than concentrating it on individual conductors.
This enhanced crush resistance is particularly valuable in applications where cables must be routed across areas that may be subjected to vehicle traffic or where falling debris is a concern. Traditional cable routing methods, such as overhead lines or underground conduits, are often impractical in open-cut mining environments, making the cable's ability to withstand mechanical abuse essential for reliable operation.
Electrical and Mechanical Specifications: Engineering Excellence in Detail
The technical specifications of AS/NZS 2802 Type 441 Class 2 cables reflect decades of engineering evolution specifically focused on the demands of Australian mining operations. These specifications are not arbitrary numbers but represent carefully engineered solutions to real-world challenges faced by mining operators across the continent.
Compliance and Standards Framework
The compliance framework for Type 441 Class 2 cables encompasses multiple Australian and New Zealand standards, each addressing specific aspects of cable performance and safety. The primary standard, AS/NZS 2802:2000, establishes the fundamental requirements for mining cables, including construction specifications, electrical performance criteria, and testing protocols that ensure cables can withstand the demands of mining applications.
AS/NZS 1125 addresses the specific requirements for flexible cables used in mining applications, with particular emphasis on the mechanical properties necessary for trailing and reeling operations. This standard establishes requirements for conductor flexibility, insulation durability, and sheath resistance to mechanical damage that are critical for mining cable reliability.
AS/NZS 3808 focuses on the electrical safety aspects of mining cables, establishing requirements for insulation resistance, dielectric strength, and fault current handling capabilities. These requirements are particularly important in mining applications where electrical faults can have consequences that extend far beyond simple equipment damage.
AS/NZS 5000.1 provides the overarching framework for electrical installations in mining environments, establishing the context within which mining cables must operate. This standard addresses issues such as earthing systems, protection coordination, and safety protocols that influence cable design and application.
The integration of these standards ensures that Type 441 Class 2 cables meet not only the immediate electrical and mechanical requirements of mining applications but also the broader safety and regulatory requirements that govern Australian mining operations.
Advanced Construction Details
The construction of Type 441 Class 2 cables represents a sophisticated engineering solution that addresses multiple challenges simultaneously. The three-conductor power circuit utilises flexible stranded tinned copper conductors that provide excellent electrical conductivity while maintaining the flexibility necessary for trailing and reeling applications.
The use of tinned copper for the power conductors serves several important functions. The tinning process provides corrosion protection in the harsh environments typical of mining operations, where exposure to moisture, chemicals, and abrasive materials can rapidly degrade untreated copper. The tinning also improves the connection reliability at terminations, reducing the likelihood of connection failures that could cause equipment downtime.
The EPR (Ethylene Propylene Rubber) insulation system provides excellent electrical properties combined with superior mechanical durability. EPR maintains its insulation properties across a wide temperature range and demonstrates excellent resistance to the types of mechanical stress encountered in mining applications. The insulation system includes a semiconductive screen that helps control electrical stress distribution within the cable.
The three interstitial earth conductors represent a critical safety feature that goes beyond simple regulatory compliance. These conductors provide multiple independent earth paths, ensuring that earth fault protection systems can operate reliably even if one earth conductor is damaged. The semiconductive PCP (Polychloroprene) covering on these conductors provides additional protection against mechanical damage while maintaining the electrical properties necessary for effective earth fault protection.
The central extensible pilot conductor represents one of the most innovative features of Type 441 Class 2 cables. This conductor enables continuous monitoring of cable integrity through the use of pilot wire protection systems. These systems can detect developing faults before they become dangerous, allowing for planned maintenance rather than emergency repairs.
Comprehensive Dimensional and Performance Data
The dimensional specifications for Type 441 Class 2 cables reflect careful optimisation between electrical performance, mechanical durability, and practical handling considerations. The range of available sizes, from 6 mm² to 300 mm², ensures that appropriate cable sizes are available for applications ranging from small mobile equipment to the largest draglines and shovels.
For the smallest size (6 mm²), the cable incorporates 84 strands of 0.30 mm diameter tinned copper wire, providing excellent flexibility while maintaining adequate current-carrying capacity. The 1.5 mm insulation thickness provides substantial electrical protection, while the 28.5 mm overall diameter ensures the cable remains manageable for installation and maintenance operations.
At the largest size (300 mm²), the cable utilises 854 strands of 0.67 mm diameter wire, providing the current-carrying capacity necessary for the largest mining equipment. The 3.0 mm insulation thickness and 91.2 mm overall diameter reflect the increased electrical and mechanical demands of high-power applications.
The weight progression from 111 kg/100m for the 6 mm² size to 1629 kg/100m for the 300 mm² size illustrates the substantial mechanical engineering challenges involved in designing cables that can support their own weight over the distances typical of mining applications. The textile braid reinforcement becomes increasingly important in larger sizes, providing the tensile strength necessary to prevent damage during installation and operation.
The earth conductor specifications are carefully matched to the power conductor sizes, ensuring adequate fault current capacity while maintaining mechanical compatibility with the overall cable construction. The pilot conductor specifications remain consistent across all sizes, reflecting the standardised requirements for cable monitoring systems.
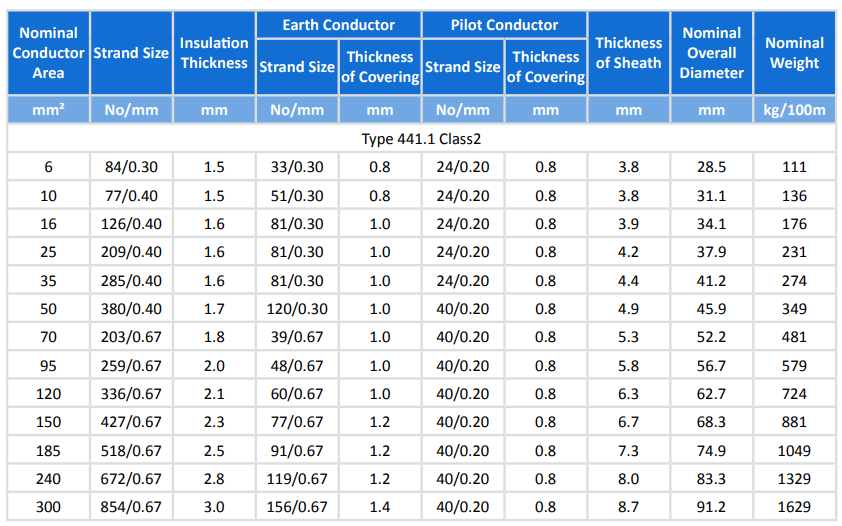
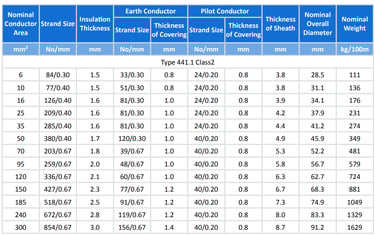
Typical Mining Use Cases: Real-World Applications and Benefits
The practical applications of Type 441 Class 2 cables in Australian mining operations demonstrate the real-world benefits of their advanced design and construction. These applications range from straightforward power supply situations to complex installations that require careful coordination between electrical, mechanical, and safety systems.
Haul Truck and Mobile Equipment Power Supply
While many haul trucks in modern mining operations utilise diesel-electric drive systems, there remains a significant population of all-electric haul trucks, particularly in operations where environmental considerations favour electric power. These vehicles present unique challenges for power supply cables, as they require high-power electrical connections that can be quickly established and broken during loading and unloading operations.
Type 441 Class 2 cables excel in these applications due to their ability to handle the high current requirements of electric haul trucks while withstanding the mechanical stresses of repeated connection and disconnection. The cables' flexibility allows them to accommodate the movement of the truck during loading operations, while their mechanical durability ensures reliable service despite the harsh operating environment.
The central pilot conductor becomes particularly valuable in haul truck applications, as it enables monitoring of cable condition during operation. This monitoring capability allows operators to detect developing problems before they result in equipment failure, reducing the likelihood of costly downtime during critical loading operations.
Dragline Power and Control Systems
Draglines represent perhaps the most demanding application for Type 441 Class 2 cables, combining extreme electrical loads with severe mechanical stresses. Modern draglines can require several megawatts of power for their drive systems, along with sophisticated control and monitoring systems that depend on reliable electrical connections.
The electrical demands of dragline operation are characterised by extreme variability, with power requirements ranging from relatively modest levels during positioning operations to maximum levels during digging and swinging operations. Type 441 Class 2 cables must be capable of handling these load variations without degradation, while also providing the mechanical durability necessary for the constant movement required in dragline operations.
The semiconductive cradle separator proves particularly valuable in dragline applications, where the cable may be subjected to crushing forces as the dragline moves across uneven terrain. The enhanced crush resistance provided by this design feature can mean the difference between continued operation and costly downtime for cable replacement.
Relocatable Crushing and Processing Plant Connections
The trend toward relocatable processing equipment in modern mining operations has created new applications for Type 441 Class 2 cables. These mobile plants must be repositioned regularly as mining progresses, requiring electrical connections that can be quickly established and broken down without compromising reliability.
Type 441 Class 2 cables are ideally suited for these applications due to their combination of mechanical durability and electrical performance. The cables can withstand the mechanical stresses of repeated installation and removal, while their electrical properties ensure reliable power delivery to critical processing equipment.
The reeling capability of Type 441 Class 2 cables becomes particularly valuable in relocatable plant applications, where the ability to quickly deploy and retrieve electrical connections can significantly reduce setup and breakdown times. This capability translates directly into increased equipment utilisation and improved operational efficiency.
Long-Term Moving and Reeling Applications
Some mining operations require electrical connections that must be regularly repositioned over distances of several hundred metres. These applications might include conveyors that advance as mining progresses, or processing equipment that must be periodically relocated to maintain optimal positioning relative to the mining face.
Type 441 Class 2 cables excel in these applications due to their design features that address the specific challenges of repeated reeling and unreeling operations. The textile braid reinforcement provides the tensile strength necessary to support the cable's weight during deployment, while the flexible conductor construction ensures that the cable maintains its electrical properties despite repeated bending and flexing.
The semiconductive cradle separator provides additional benefit in reeling applications by helping to maintain conductor geometry during the winding and unwinding process. This feature helps prevent the development of internal mechanical stresses that could lead to premature failure in conventional cable constructions.
Comprehensive FAQ: Addressing Common Mining Cable Concerns
The complexity of mining cable applications inevitably leads to questions about selection, installation, maintenance, and troubleshooting. The following comprehensive FAQ section addresses the most common concerns encountered by mining professionals working with Type 441 Class 2 cables.
Why Choose Class 2 Over Class 1 Construction?
The decision between Class 1 and Class 2 construction fundamentally comes down to the level of mechanical protection required for the specific application. Class 2 cables incorporate thicker insulation and sheath materials that provide superior protection against mechanical damage, making them the preferred choice for harsh open-cut mining environments.
The additional material thickness in Class 2 construction provides tangible benefits in terms of impact resistance, crush resistance, and abrasion resistance. While Class 1 cables may be adequate for less demanding applications, the investment in Class 2 construction typically pays for itself through reduced maintenance costs and improved reliability in challenging mining environments.
The enhanced mechanical protection of Class 2 construction becomes particularly valuable in applications where cables may be subjected to vehicle traffic, falling debris, or other mechanical hazards that are common in open-cut mining operations. The additional protection provided by Class 2 construction can prevent costly failures that would require emergency repairs or equipment replacement.
How Does the Central Pilot Conductor System Function?
The central pilot conductor represents one of the most sophisticated features of Type 441 Class 2 cables, enabling advanced monitoring and protection capabilities that are essential for modern mining safety standards. The pilot conductor operates as part of a pilot wire protection system that continuously monitors the integrity of the cable and the connected equipment.
In typical operation, the pilot wire protection system sends a low-level signal through the pilot conductor and monitors the return signal characteristics. Changes in the signal characteristics can indicate developing problems such as insulation degradation, mechanical damage, or water ingress. This monitoring capability allows maintenance personnel to detect problems before they become dangerous or cause equipment failure.
The pilot conductor system also enables sophisticated ground fault detection capabilities that go beyond what is possible with conventional earth fault protection systems. By providing a dedicated conductor for monitoring purposes, the system can detect fault conditions that might not be detected by conventional protection systems, improving overall safety and reliability.
The extensible nature of the pilot conductor is particularly important in reeling applications, where the conductor must be capable of stretching as the cable is deployed and retracting as it is wound up. This capability ensures that the pilot conductor remains functional throughout the full range of cable deployment, maintaining monitoring capability regardless of cable position.
Environmental Resistance Capabilities
The environmental resistance of Type 441 Class 2 cables encompasses multiple aspects of protection against the harsh conditions typical of mining operations. The EPR insulation and PCP/CSP sheath materials are specifically formulated to provide resistance against UV radiation, oil contamination, and flame exposure.
UV resistance is particularly important for cables that may be exposed to direct sunlight during installation or operation. The advanced polymer formulations used in Type 441 Class 2 cables include UV stabilisers that prevent degradation of the insulation and sheath materials even after prolonged exposure to intense sunlight.
Oil resistance is essential in mining applications where hydraulic fluids, lubricants, and fuel may come into contact with cables. The sheath materials used in Type 441 Class 2 cables are specifically selected for their resistance to petroleum-based products, ensuring that accidental exposure does not compromise cable integrity.
Flame resistance is a critical safety feature that ensures cables will not contribute to fire spread in the event of an electrical fault or external ignition source. The materials used in Type 441 Class 2 cables meet strict AS/NZS standards for flame resistance, providing assurance that the cables will not become a fire hazard in mining operations.
Handling Heavy Machinery Impact and Mechanical Stress
The ability of Type 441 Class 2 cables to withstand mechanical stress from heavy machinery represents one of their most important design features. The semiconductive cradle separator plays a central role in this capability by distributing crushing forces across the entire cable cross-section rather than concentrating them on individual conductors.
When a cable is subjected to crushing forces, the cradle separator deforms in a controlled manner that protects the power conductors from damage. This deformation is designed to be recoverable, allowing the cable to return to its original shape after the crushing force is removed. This capability allows Type 441 Class 2 cables to survive impacts that would destroy conventional cables.
The textile braid reinforcement provides additional protection against tensile stresses that can occur when cables are subjected to pulling forces. This reinforcement distributes tensile loads across the entire cable construction, preventing concentration of stress on individual components that could lead to failure.
The overall construction philosophy of Type 441 Class 2 cables emphasises mechanical robustness without sacrificing electrical performance. This balance is achieved through careful selection of materials and construction techniques that provide maximum protection while maintaining the flexibility and electrical properties necessary for mining applications.
Field Repair Procedures and Best Practices
Field repair of Type 441 Class 2 cables requires specialised techniques and materials that are specifically designed for mining cable applications. The complexity of the cable construction, particularly the semiconductive components, requires careful attention to detail during repair operations to ensure that the repaired cable maintains its original performance characteristics.
Approved mining cable repair kits are essential for proper field repairs. These kits include all the materials and components necessary to restore the cable's original construction, including semiconductive materials, insulation compounds, and sheath materials that are compatible with the original cable design.
Cleanliness during repair operations is absolutely critical, as contamination can compromise the electrical properties of the repaired cable. All repair work should be conducted in clean conditions, with particular attention paid to preventing the introduction of moisture or foreign materials into the cable construction.
The repair procedures must follow vendor-specified protocols that are mapped to AS/NZS requirements. These procedures ensure that the repaired cable meets the same performance standards as the original cable, providing confidence that the repair will provide reliable service in the demanding mining environment.
Training of repair personnel is essential for successful field repairs. The complexity of modern mining cables requires that repair technicians understand not only the mechanical aspects of cable construction but also the electrical principles that govern cable performance. Regular training and certification programs help ensure that field repairs are performed to the highest standards.
Operating Temperature Ranges and Environmental Limits
The operating temperature range of Type 441 Class 2 cables reflects the extreme environmental conditions encountered in Australian mining operations. The EPR insulation system typically provides reliable operation from -25°C to +90°C, covering the full range of conditions from cold winter mornings to the extreme heat of summer operations in areas like the Pilbara.
The lower temperature limit is particularly important for mining operations in areas that experience significant temperature variations. The cable must maintain its flexibility and electrical properties even when exposed to freezing temperatures, ensuring that equipment can be started and operated safely regardless of ambient conditions.
The upper temperature limit reflects both the electrical loading of the cable and the ambient temperature conditions. Cables operating at their rated current capacity in high ambient temperatures may approach the upper temperature limit, requiring careful consideration of installation methods and operating procedures to ensure reliable performance.
The thermal characteristics of the cable also influence its current-carrying capacity, with derating factors applied when cables are operated in high ambient temperatures or when multiple cables are installed in close proximity. These derating factors ensure that the cable operates within its thermal limits, preventing degradation of the insulation system.
Proper Cable Sizing and Selection Criteria
Selecting the appropriate cable size for mining applications requires consideration of multiple factors beyond simple current-carrying capacity. The electrical load of the connected equipment, the length of the cable run, the ambient temperature conditions, and the installation method all influence the appropriate cable size.
The cross-sectional area of the power conductors must be selected to carry the full-load current of the connected equipment with appropriate safety margins. This selection must also consider the voltage drop that occurs over the length of the cable run, ensuring that the voltage at the equipment terminals remains within acceptable limits.
Derating factors must be applied when cables are operated in high ambient temperatures, installed in groups, or subjected to other conditions that reduce their current-carrying capacity. These factors ensure that the cable operates within its thermal limits, preventing premature aging of the insulation system.
The mine's power distribution design provides the overall framework within which cable selection decisions are made. This design establishes the voltage levels, protection systems, and safety requirements that influence cable selection and installation practices.
Consultation with qualified electrical engineers who understand mining applications is essential for proper cable selection. The complexity of modern mining electrical systems requires expert knowledge to ensure that cable selections are appropriate for the specific application and operating conditions.
Termination Practices and Connection Integrity
Proper termination of Type 441 Class 2 cables is essential for reliable operation and safety in mining applications. The complexity of the cable construction, particularly the semiconductive components, requires specialised termination techniques that ensure all components are properly connected and protected.
Heat-shrink termination systems are commonly used for mining cable applications, providing reliable environmental sealing while maintaining the electrical properties of the cable. These systems must be properly sized and installed to ensure complete sealing against moisture ingress, which is a common cause of cable failure in mining environments.
Compression lugs provide reliable electrical connections for the power conductors, ensuring low resistance connections that will not degrade over time. The lugs must be properly sized for the conductor and installed using appropriate tools to ensure proper compression and electrical contact.
The semiconductive screen components require special attention during termination to ensure proper electrical stress control. These components must be properly bonded to the earthing system to prevent the development of electrical stress concentrations that could lead to insulation failure.
Training of termination personnel is essential for reliable cable performance. The specialised nature of mining cable terminations requires that personnel understand not only the mechanical aspects of the termination process but also the electrical principles that govern proper termination practices.
Environmental Challenges: Dust and Water Ingress
The harsh environmental conditions in mining operations present ongoing challenges for cable reliability, with dust and water ingress being among the most common causes of cable failure. Type 441 Class 2 cables incorporate multiple design features to address these challenges, but proper installation and maintenance practices are essential for optimal performance.
The PCP/CSP sheath provides excellent resistance to water and oil ingress, but the integrity of this protection depends on proper installation and maintenance of cable terminations and connections. All terminations must be properly sealed to prevent water ingress, which can rapidly lead to insulation failure and equipment damage.
Dust contamination presents particular challenges in mining environments, where fine particles can penetrate even small openings in cable systems. Regular inspection and cleaning of cable terminations and connections helps prevent the accumulation of conductive dust that could cause electrical faults.
The design of cable support and routing systems must consider the environmental challenges of the specific mining operation. Cables should be routed to minimise exposure to water accumulation and dust concentration, while still providing the flexibility necessary for equipment operation.
Maintenance programs should include regular inspection of cable condition, with particular attention to areas where environmental exposure is greatest. Early detection of environmental damage allows for corrective action before problems become serious enough to cause equipment failure.
Cable Lifespan and Maintenance Optimization
The lifespan of Type 441 Class 2 cables in mining applications varies significantly depending on the duty cycle, environmental conditions, and maintenance practices. Typical lifespans range from 3 to 5 years in harsh applications, but proper maintenance and monitoring can extend this significantly.
The duty cycle of the connected equipment has a major influence on cable lifespan, with cables serving equipment that operates continuously experiencing more rapid wear than those serving intermittent loads. Understanding the duty cycle helps in planning maintenance schedules and predicting replacement requirements.
Regular inspection programs are essential for maximising cable lifespan. These inspections should include visual examination of the cable exterior, electrical testing of insulation resistance, and monitoring of pilot conductor systems where installed. Early detection of developing problems allows for corrective action before failures occur.
The pilot core monitoring capability of Type 441 Class 2 cables provides valuable information about cable condition that can be used to optimise maintenance schedules. Trending of pilot conductor measurements can indicate developing problems and help predict when maintenance or replacement will be required.
Proper storage and handling of spare cables is also important for maximising lifespan. Cables should be stored in clean, dry conditions and protected from UV exposure and mechanical damage. Proper handling techniques during installation help prevent damage that could reduce cable lifespan.
Conclusion: The Foundation of Safe and Efficient Mining Operations
Type 441 Class 2 cables represent far more than simple electrical connections in Australian open-cut mining operations. They serve as the critical foundation that enables the massive scale and precision required for modern mining while maintaining the safety standards that protect both personnel and equipment in these challenging environments.
The engineering sophistication embodied in these cables reflects decades of evolution in understanding the unique challenges of mining electrical systems. From the semiconductive cradle separator that provides crush resistance to the central pilot conductor that enables advanced monitoring capabilities, every aspect of Type 441 Class 2 cable design addresses real-world challenges encountered in mining operations across Australia.
The scale of Australia's open-cut mining operations, from the massive iron ore extraction at Mount Whaleback to the precision gold mining at the Super Pit, demands electrical infrastructure that can operate reliably under conditions that would quickly destroy conventional cables. Type 441 Class 2 cables provide this capability through their combination of advanced materials, sophisticated construction techniques, and compliance with stringent Australian standards.
The application versatility of these cables, from trailing draglines across unstable terrain to providing reliable connections for relocatable processing plants, demonstrates their value across the full spectrum of mining operations. Their ability to withstand mechanical abuse while maintaining electrical integrity makes them indispensable for operations where downtime can cost millions of dollars per day.
Perhaps most importantly, Type 441 Class 2 cables contribute to the safety culture that is essential for modern mining operations. Through features like the central pilot conductor monitoring system and compliance with flame resistance standards, these cables help create electrical systems that not only perform reliably but also provide early warning of developing problems that could threaten personnel safety.
The investment in proper cable selection, installation, and maintenance represents a small fraction of the total cost of mining operations, but the impact of this investment on operational reliability and safety is profound. Type 441 Class 2 cables, when properly selected and maintained, provide the electrical foundation that allows Australia's mining industry to continue its vital role in the global economy while maintaining the highest standards of safety and efficiency.
As mining operations continue to evolve toward larger equipment, greater automation, and more sophisticated monitoring systems, the importance of reliable electrical infrastructure will only continue to grow. Type 441 Class 2 cables provide the proven foundation upon which these future developments can be built, ensuring that Australia's mining industry remains at the forefront of global mining technology and practice.
The success of Type 441 Class 2 cables in Australian mining operations demonstrates the value of engineering solutions that are specifically designed for their intended application environment. Rather than adapting general-purpose cables for mining use, these cables represent purpose-built solutions that address the unique challenges of open-cut mining operations. This approach to engineering excellence provides the reliability and safety that are essential for the continued success of Australia
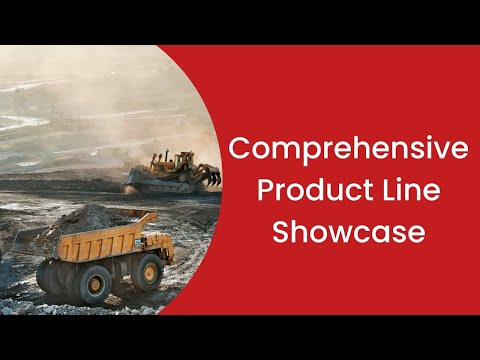