(N)3GHSSHCH 8.7/15kV and 12/20kV Mining Cables
In the challenging world of underground mining and tunneling operations, reliable power distribution is absolutely critical for both operational efficiency and safety. The (N)3GHSSHCH cables represent specialized medium voltage (MV) cable technology specifically engineered to thrive in these demanding environments. These flexible, robust cables deliver dependable power to essential equipment in some of industry's most challenging settings. This article aims to provide a comprehensive understanding of (N)3GHSSHCH cables, exploring their unique applications, technical specifications, and addressing common questions about their use. Whether you're an engineer specifying equipment for a new mining project, a maintenance professional responsible for existing infrastructure, or simply interested in specialized industrial cables, this guide will deepen your understanding of these important components.
5/21/20258 min read
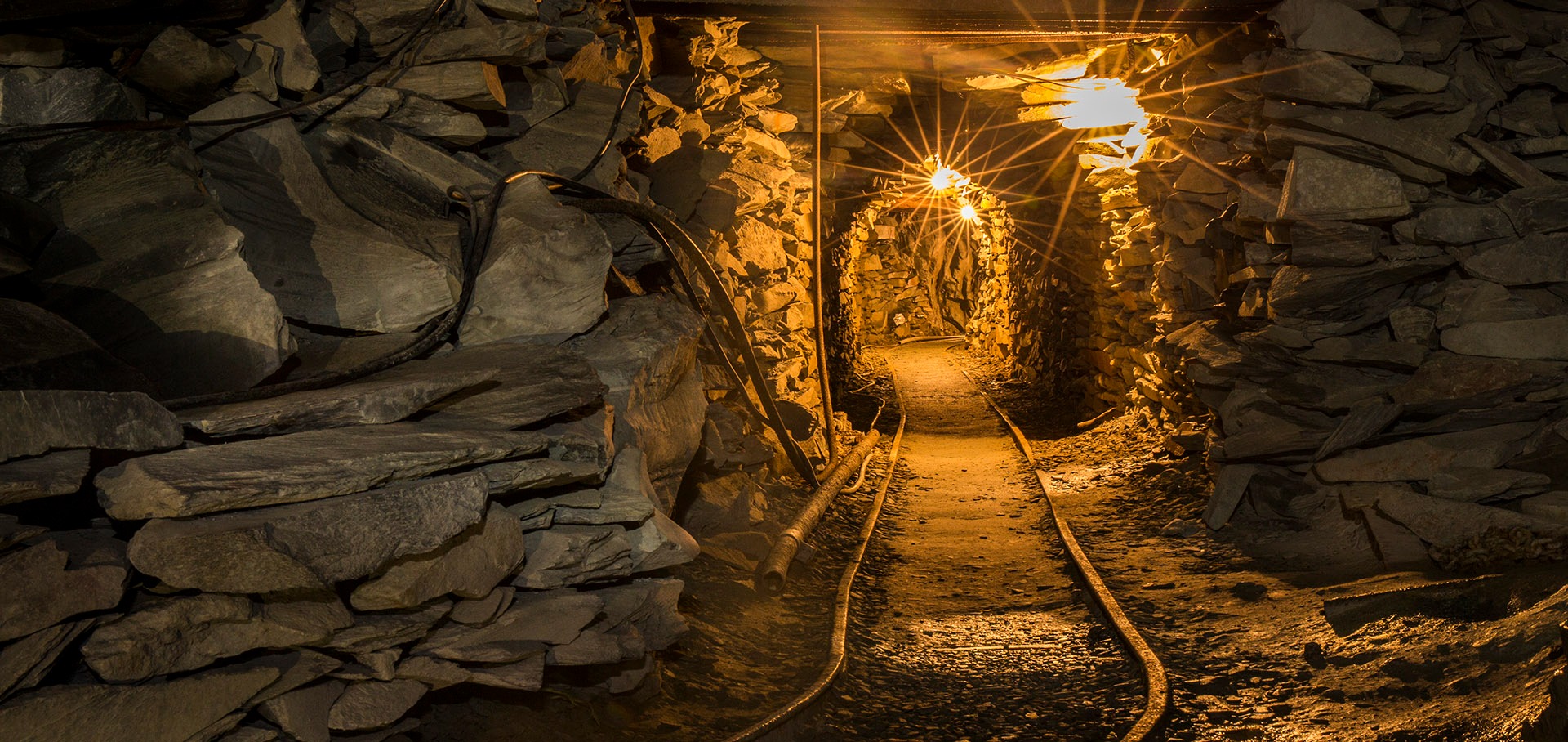
(N)3GHSSHCH 8.7/15kV and 12/20kV Mining Cables
I. Introduction
In the challenging world of underground mining and tunneling operations, reliable power distribution is absolutely critical for both operational efficiency and safety. The (N)3GHSSHCH cables represent specialized medium voltage (MV) cable technology specifically engineered to thrive in these demanding environments. These flexible, robust cables deliver dependable power to essential equipment in some of industry's most challenging settings.
This article aims to provide a comprehensive understanding of (N)3GHSSHCH cables, exploring their unique applications, technical specifications, and addressing common questions about their use. Whether you're an engineer specifying equipment for a new mining project, a maintenance professional responsible for existing infrastructure, or simply interested in specialized industrial cables, this guide will deepen your understanding of these important components.
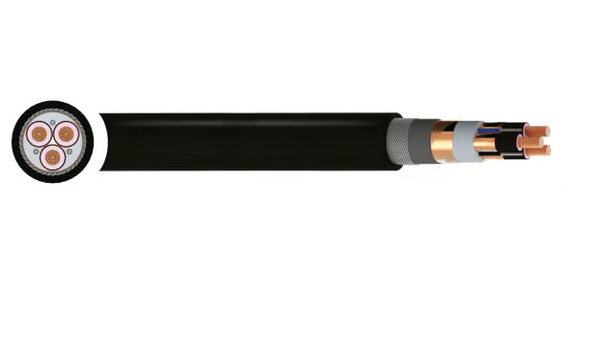
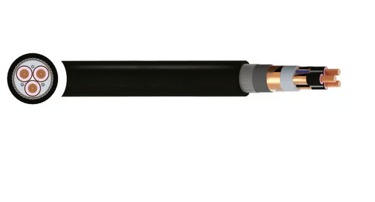
II. Application Scenarios
Underground Mining Operations
The primary application of (N)3GHSSHCH cables is in underground mining, where they supply power to both mobile and stationary equipment. Underground mining presents unique challenges for electrical systems, including limited space, potentially explosive atmospheres, wet conditions, and constant mechanical stress. In this environment, these cables power critical equipment such as:
Continuous miners and longwall shearers
Mobile mining equipment like shuttle cars and roof bolters
Ventilation systems ensuring breathable air underground
Dewatering pumps keeping mining areas operational
Lighting systems for visibility and safety
The flexibility of these cables allows them to follow mining equipment as operations progress through the mine, while their robust construction withstands the harsh conditions inherent in underground operations.
Tunneling Projects
Similar to mining applications, tunneling projects require reliable power distribution in confined spaces with challenging environmental conditions. During tunnel construction and maintenance, (N)3GHSSHCH cables supply power to:
Tunnel boring machines (TBMs)
Conveyor systems for removing excavated material
Temporary and permanent lighting installations
Ventilation equipment maintaining air quality
Water pumping systems controlling groundwater infiltration
The cables' ability to flex without damage is particularly important in tunneling, where equipment often moves along a progressing tunnel face, requiring the power supply to follow while maintaining integrity.
Hazardous Environments
Beyond their primary applications, (N)3GHSSHCH cables are suitable for any industrial environment characterized by:
High mechanical stress from equipment movement
Persistent moisture or temporary submersion
Potential exposure to oils, fuels, and industrial chemicals
Risk of fire, with the need for low smoke and zero halogen performance
Abrasive conditions that would damage standard cables
The comprehensive protection features built into these cables make them valuable in chemical processing plants, oil and gas facilities, and similar challenging industrial settings.
Compliance with Standards
(N)3GHSSHCH cables are designed and manufactured in accordance with several key standards:
VDE 0250 Part 605: Specifying requirements for rubber-insulated power cables
VDE 0207: Defining insulating and sheathing materials for cables
IEC/EN 60332-1-2: Flame retardant testing for electrical cables
IEC/EN 60754-1/2: Testing for halogen content and acidity of gases during combustion
This adherence to international standards ensures consistent performance, compatibility with standard connection equipment, and predictable behavior in emergency situations—all crucial factors in high-risk environments like mining and tunneling.
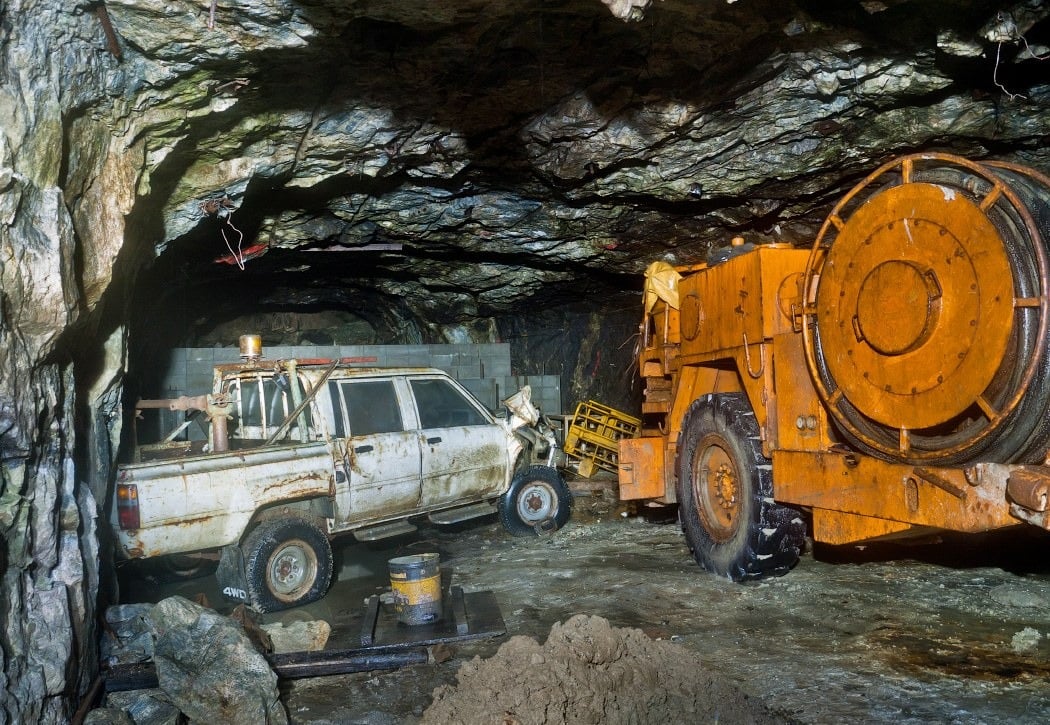
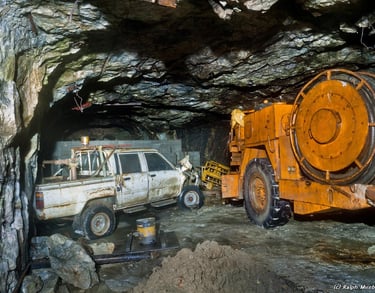
III. Electrical and Technical Specifications
Voltage Ratings
(N)3GHSSHCH cables are available in two primary voltage configurations:
8.7/15kV: The lower voltage option, suitable for many standard mining and tunneling applications
12/20kV: The higher voltage alternative, providing greater power transmission capability over longer distances
These ratings represent the operating voltage (U₀/U), where U₀ is the voltage between conductor and earth, and U is the voltage between conductors. The test voltages (24kV for 8.7/15kV cables and 29kV for 12/20kV cables) confirm the cables' ability to withstand temporary voltage spikes without failure.
Operating Temperatures
These cables are designed to function across a broad temperature range:
Fixed Installation: -40°C to +80°C, allowing deployment in extremely cold environments as well as high-temperature industrial settings
Flexible Applications: +5°C to +80°C, with the higher minimum temperature reflecting the reduced flexibility of polymers at very low temperatures when being actively flexed
This temperature performance ensures reliable operation from arctic mining conditions to hot subterranean environments where ambient temperatures can rise significantly.
Cable Construction
The (N)3GHSSHCH cables feature a sophisticated multi-layer construction designed to provide electrical performance, mechanical protection, and safety features:
Phase Conductor: Class 5 flexible stranded copper provides the primary current path with enhanced flexibility compared to rigid conductors. The stranding allows the cable to flex repeatedly without developing fatigue cracks.
Insulation: A specialized rubber compound surrounds each conductor, providing excellent dielectric properties (electrical insulation) while maintaining flexibility across the operating temperature range.
Semi-Conductive Layers: Both inner and outer semi-conductive rubber layers sandwich the insulation. These layers create a smooth, uniform electric field around the conductor, eliminating points of high electrical stress that could lead to premature failure.
Protective Earth Conductor: Individual copper wire screens provide a path for fault currents, enhancing safety by ensuring rapid response of protection systems during ground faults.
Control Conductor: Class 5 flexible stranded tinned copper conductors carry control signals, allowing remote operation of connected equipment.
Central Filler: A rubber compound on a textile polyester support maintains the cable's circular cross-section, providing structural integrity while remaining flexible.
First Inner Sheath: LSZH (Low Smoke Zero Halogen) material provides the initial layer of mechanical protection while ensuring minimal toxic emissions during fires.
Monitoring Conductor: A copper wire screen over the first inner sheath allows for continuous monitoring of cable integrity through resistance measurements.
Second Inner Sheath: Another LSZH layer adds further mechanical protection and fire performance.
Armour: Steel wire braid over the second inner sheath provides exceptional mechanical protection against crushing, impacts, and abrasion.
Outer Sheath: A final LSZH layer provides environmental protection against moisture, chemicals, and abrasion while maintaining the cable's flame-retardant and low-toxicity characteristics.
This complex construction creates a cable that maintains electrical performance while withstanding the severe mechanical stresses and environmental challenges of mining and tunneling operations.
Mechanical Properties
The mechanical specifications of (N)3GHSSHCH cables reflect their intended use in dynamic applications:
Minimum Bending Radius:
Fixed installations: 6 times the overall diameter
Flexed applications: 10 times the overall diameter
These limits prevent internal damage to conductors and insulation during installation and operation.
Maximum Tensile Load: Ranging from 1,125N for 25mm² cables to 5,400N for 120mm² cables, these ratings ensure the cable can withstand pulling forces during installation without damage.
Weight: From approximately 4,030 kg/km for smaller 8.7/15kV cables to 8,920 kg/km for larger 12/20kV variants. This weight reflects the substantial protective elements incorporated into the cable design.
Current Carrying Capacity: Varies based on installation method and cross-sectional area, with values ranging from 31 amps (for 25mm² cable in 7-layer configuration) to 428 amps (for 150mm² cable laid on the floor). These ratings account for heat dissipation in different installation scenarios.
STANDARDS
VDE 0250 Part 605, VDE 0207, Flame Retardant according to IEC/EN 60332-1-2 Halogen Free according to IEC/EN 60754-1/2
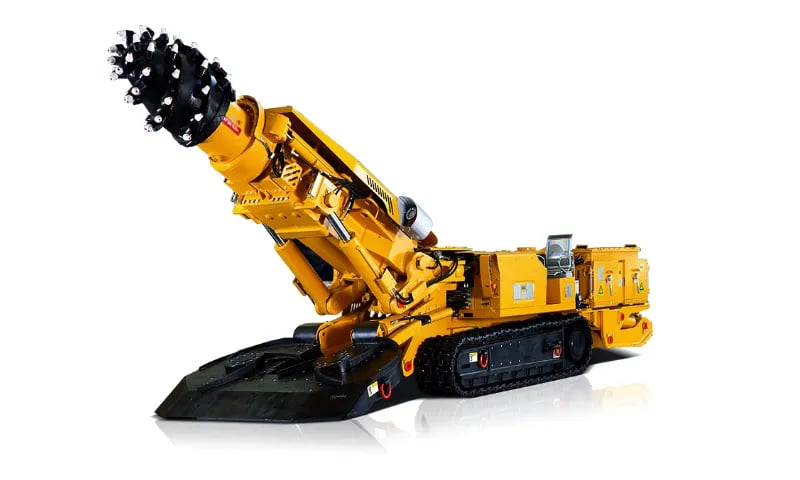
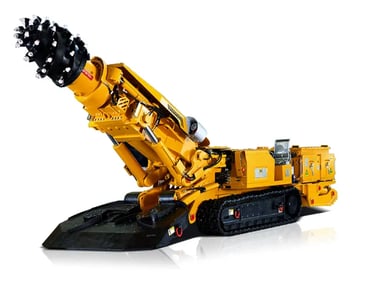
IV. Frequently Asked Questions (FAQs)
Q1: What distinguishes (N)3GHSSHCH cables from other mining cables?
A1: (N)3GHSSHCH cables stand apart from standard mining cables in several important ways. Their medium voltage rating (8.7/15kV or 12/20kV) allows them to handle higher power requirements than typical low-voltage cables. The construction includes multiple protective features specifically for harsh environments: LSZH sheaths for fire safety, steel wire braid armour for exceptional mechanical protection, and Class 5 flexible stranded conductors enabling repeated movement without failure.
Additionally, the cable's designation provides insight into its construction:
(N): Indicates compliance with VDE standards
3G: Three phase conductors
H: Rubber insulation
S: Copper wire screens
SH: Steel wire braid
CH: LSZH outer sheath
This combination of features creates a cable specifically engineered for the most demanding underground applications where reliability, safety, and flexibility are paramount.
Q2: Why is LSZH material used in the sheathing?
A2: Low Smoke Zero Halogen (LSZH) materials represent a significant safety advancement for cables used in confined spaces like mines and tunnels. When conventional PVC cable insulation burns, it releases dense smoke and toxic halogenated gases including hydrogen chloride, which forms hydrochloric acid when combined with moisture. These byproducts can be lethal in confined spaces and severely hamper evacuation efforts.
LSZH materials, by contrast, emit dramatically less smoke when burning and no halogenated gases. This provides two critical safety benefits in emergency situations:
Improved visibility during evacuation, allowing miners to find escape routes
Reduced toxic exposure, giving personnel more time to evacuate safely
In underground environments where evacuation is already challenging due to limited exit routes, these properties can be life-saving. The multiple LSZH layers in (N)3GHSSHCH cables (two inner sheaths and the outer sheath) demonstrate the priority placed on safety in their design.
Q3: Can these cables be used in both fixed and mobile applications?
A3: Yes, (N)3GHSSHCH cables are engineered for versatility, functioning effectively in both fixed installations and mobile applications. This dual capability stems from several design elements:
For fixed installations (-40°C to +80°C):
The cable's robust construction withstands long-term environmental exposure
Its smaller minimum bending radius (6x diameter) allows for efficient routing
The LSZH sheathing provides long-term resistance to environmental degradation
For mobile applications (+5°C to +80°C):
Class 5 flexible stranded conductors allow repeated flexing without metal fatigue
The larger operational bending radius (10x diameter) prevents internal damage during movement
The steel wire braid provides exceptional protection against abrasion during repeated movement
This versatility makes these cables particularly valuable in mining operations where equipment may initially be fixed but later require relocation as mining progresses to new areas.
Q4: How do the semi-conductive layers benefit the cable's performance?
A4: The semi-conductive layers in (N)3GHSSHCH cables play a crucial but often underappreciated role in ensuring long-term reliability. In medium voltage cables, electrical stress is particularly concentrated at the interface between the conductor and insulation, and at the outer surface of the insulation. Without management, these stress concentrations can lead to partial discharges that gradually degrade insulation and lead to premature failure.
The semi-conductive layers address this issue by creating a smooth, uniform electric field distribution:
The inner semi-conductive layer surrounds the conductor, filling any surface irregularities and eliminating sharp points that would concentrate electric fields.
The outer semi-conductive layer creates a smooth transition at the insulation's outer boundary.
Together, these layers ensure that electric field strength remains below critical values throughout the cable's cross-section, significantly extending service life and enhancing reliability. In demanding underground applications where cable replacement is costly and disruptive, this improved lifespan represents a substantial operational advantage.
Q5: What maintenance practices are recommended for these cables?
A5: While (N)3GHSSHCH cables are designed for durability in harsh environments, proper maintenance practices can significantly extend their service life:
Regular Visual Inspections: Check for:
Outer sheath damage that might compromise environmental protection
Kinks or crushing that could damage internal components
Signs of excessive heat at connection points, which may indicate poor terminations
Proper Installation Practices:
Always respect minimum bending radius requirements, especially in mobile applications
Ensure adequate support to prevent excessive tension on cable runs
Use appropriate cable glands and terminations suited for medium voltage applications
Environmental Considerations:
Avoid prolonged exposure to oils or solvents not accounted for in the cable specification
Ensure drainage in areas where cables might otherwise remain submerged
Protect from falling rocks or contact with sharp edges where possible
Electrical Testing:
Periodically verify insulation resistance values
Test earth continuity to ensure safety systems remain effective
Use partial discharge testing for critical applications to detect insulation degradation before failure
Documentation:
Maintain records of installation dates and conditions
Document any damage and repairs
Track cable movement in mobile applications to monitor cumulative mechanical stress
Implementing these practices creates a proactive maintenance regime that can help prevent unexpected downtime and enhance overall safety.
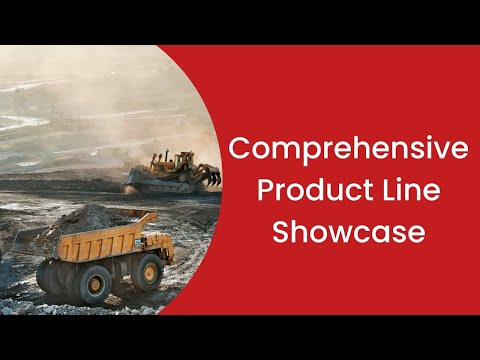
V. Conclusion
(N)3GHSSHCH 8.7/15kV and 12/20kV cables represent specialized engineering solutions for the extreme demands of underground mining and tunneling environments. Their sophisticated construction balances electrical performance, mechanical resilience, and safety considerations to create a cable uniquely suited to these challenging applications.
The combination of Class 5 flexible conductors, rubber insulation, semi-conductive stress control layers, multiple LSZH sheaths, and steel wire braid armour delivers exceptional resistance to the mechanical stresses, environmental challenges, and safety requirements inherent in underground operations.
For engineers and operators in mining and tunneling industries, understanding the capabilities and limitations of these cables is essential for ensuring reliable power distribution in environments where system failures can have serious operational and safety implications. By selecting the appropriate cable specifications and implementing recommended installation and maintenance practices, mining operations can achieve the reliability and safety that modern industrial standards demand.
As mining technology continues to advance, these specialized cables will remain a critical component in delivering the power necessary for increasingly sophisticated underground operations, supporting the industry's ongoing evolution toward greater efficiency, safety, and sustainability.