PVC vs. XLPE Cable Insulation Explained
In modern electrical and data networks—from home appliances and lighting to city grids and massive data centers—the insulation surrounding conductors is more than mere plastic: it’s a critical barrier that ensures safety, longevity and optimal performance. This article unpacks the two most common insulation materials, Polyvinyl Chloride (PVC) and Cross-Linked Polyethylene (XLPE). You’ll learn why insulation matters, how PVC and XLPE differ in chemical structure, heat resistance, mechanical strength and installation practices, and which applications favor each material. Through side-by-side comparisons, practical case studies and a look at emerging trends, you’ll gain the insight needed to choose the right cable insulation for any project.
5/16/20259 min read
PVC vs. XLPE Cable Insulation Explained
1. Introduction
In modern electrical and data networks—from home appliances and lighting to city grids and massive data centers—the insulation surrounding conductors is more than mere plastic: it’s a critical barrier that ensures safety, longevity and optimal performance. This article unpacks the two most common insulation materials, Polyvinyl Chloride (PVC) and Cross-Linked Polyethylene (XLPE). You’ll learn why insulation matters, how PVC and XLPE differ in chemical structure, heat resistance, mechanical strength and installation practices, and which applications favor each material. Through side-by-side comparisons, practical case studies and a look at emerging trends, you’ll gain the insight needed to choose the right cable insulation for any project.
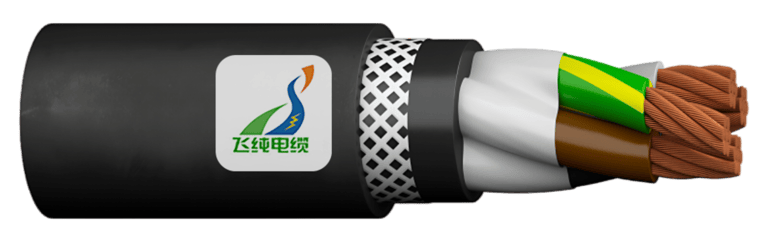
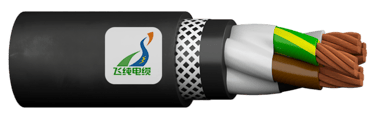
2. Basics of Cable Insulation
2.1. Role of Insulation
Cable insulation serves multiple critical functions:
Electrical Isolation: The primary purpose of insulation is to confine electrical current to the conductor, preventing leakage, short circuits, and potential hazards.
Mechanical Protection: Insulation shields the conductor from physical damage during installation and service.
Environmental Shielding: It protects against moisture, chemicals, UV radiation, and other environmental factors that could compromise the cable's integrity.
Thermal Management: Quality insulation helps manage heat generated during operation, preventing overheating and maintaining performance.
Signal Integrity: In data and communication cables, insulation properties directly impact signal quality and transmission speeds.
2.2. Common Insulating Materials
Insulating materials generally fall into two major categories:
Thermoplastics: Materials that soften when heated and harden when cooled, allowing them to be remolded multiple times. PVC is a classic example of a thermoplastic insulator.
Thermosets: Materials that undergo irreversible chemical changes during processing, resulting in a permanently set structure that cannot be remolded with heat. XLPE belongs to this category.
This fundamental difference in molecular structure creates distinct performance characteristics that make each material suitable for different applications.
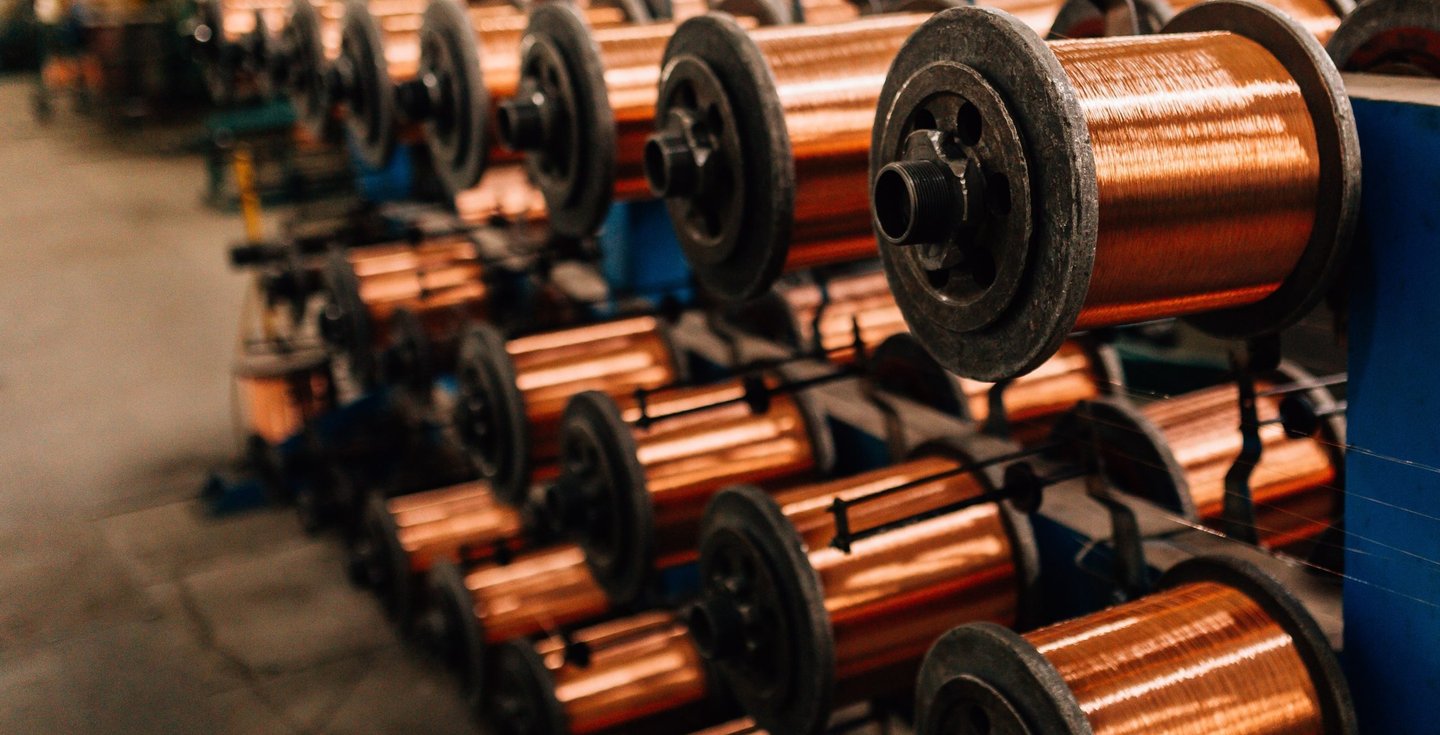
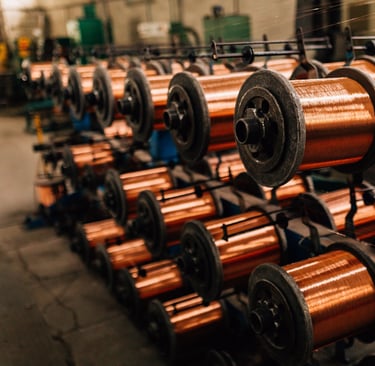
3. PVC (Polyvinyl Chloride) Insulation
3.1. Chemical Structure & Manufacturing
PVC is a synthetic plastic polymer made from repeating vinyl chloride monomers. Its basic formula is (C₂H₃Cl)n, with chlorine atoms comprising about 57% of its weight. The manufacturing process involves polymerization of vinyl chloride monomers, followed by the addition of plasticizers to enhance flexibility and other additives to improve specific properties.
PVC cable insulation typically contains:
Base PVC resin
Plasticizers (phthalates, adipates, or trimellitates)
Stabilizers to prevent degradation
Flame retardants
Fillers and colorants
The mixture is compounded, extruded around the conductor, and cooled to form the finished insulation layer.
3.2. Key Properties
Electrical Rating
Dielectric Strength: 15-50 kV/mm (varies with formulation)
Volume Resistivity: 10¹²-10¹⁵ Ω·cm
Suitable for Low to Medium Voltage: Commonly used up to 600-1000V applications
Thermal Limits
Continuous Operating Temperature: 70-105°C (depending on formulation)
Emergency Overload: Up to 130°C for short durations
Low Temperature Flexibility: Remains workable down to -15°C with standard plasticizers, or -40°C with special formulations
Flexibility and Mechanical Strength
Tensile Strength: 10-25 MPa
Elongation at Break: 150-400%
Highly Flexible: Excellent bend radius properties, especially with higher plasticizer content
Abrasion Resistance: Moderate
Flame Retardancy
Inherently Flame Retardant: The chlorine content naturally suppresses combustion
Self-Extinguishing: Typically stops burning when ignition source is removed
Low Smoke Variants: Special formulations available for reduced smoke emission
Meets Various Standards: UL, IEC, and EN fire safety requirements
3.3. Typical Applications
Building Wiring: Electrical installations in residential and commercial buildings
Appliance Wiring: Internal connections in household and industrial equipment
Control Cables: Industrial automation and control systems
Power Cords: Flexible connections for portable equipment
Automotive Wiring: Vehicle electrical systems (non-engine compartment)
Low-Voltage Power Distribution: Indoor commercial and industrial settings
3.4. Pros & Cons
Advantages
Cost-Effective: Lower material and processing costs
Easy Processing: Can be extruded at relatively low temperatures
Excellent Flexibility: Good handling characteristics during installation
Inherent Flame Retardancy: Reduced need for additional fire-inhibiting additives
Color Versatility: Easily colored for circuit identification
Good Chemical Resistance: Particularly against acids and alkalis
Disadvantages
Limited Temperature Range: Lower thermal endurance than alternatives
Environmental Concerns: Chlorine content raises end-of-life disposal issues
Plasticizer Migration: Can harden over time as plasticizers leach out
Moderate Electrical Properties: Lower voltage ratings than XLPE
Potential for Hydrogen Chloride Release: Can produce corrosive gases when burned
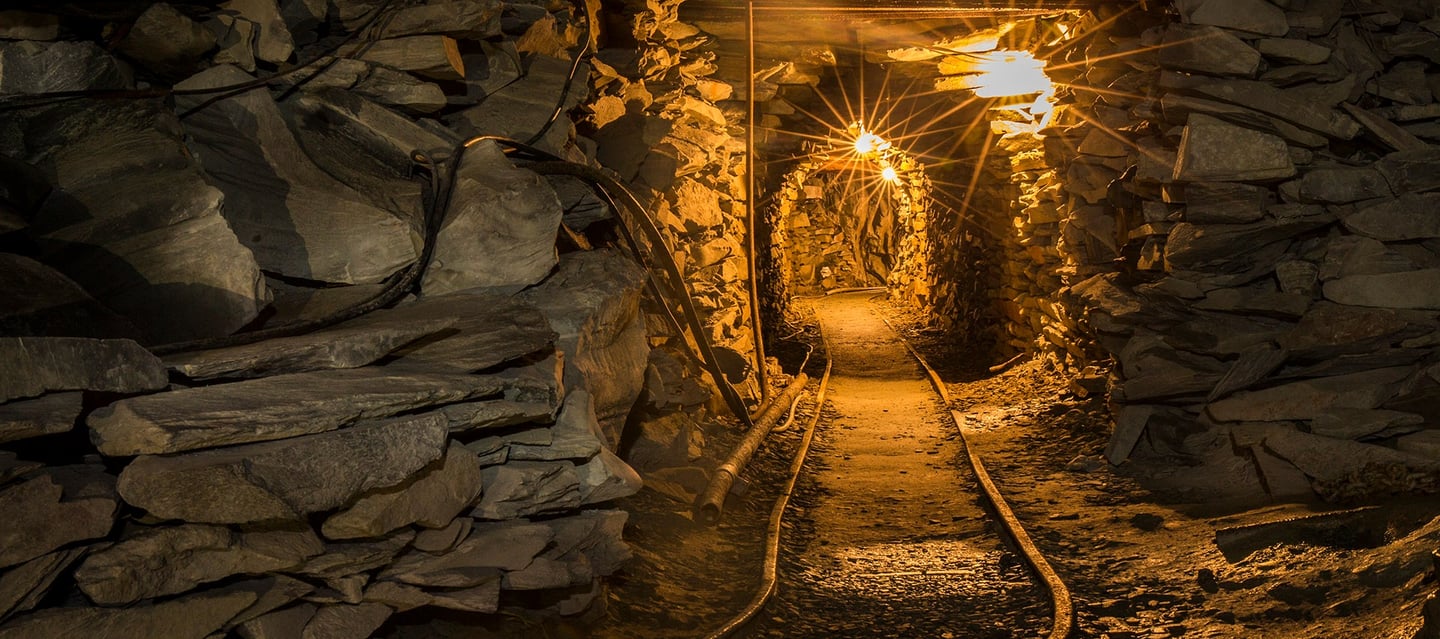
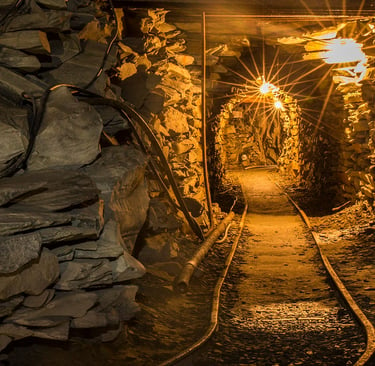
4. XLPE (Cross-Linked Polyethylene) Insulation
4.1. Cross-Linking Process & Chemistry
XLPE begins as standard polyethylene (PE), a simple polymer with the formula (C₂H₄)n. The cross-linking process transforms this thermoplastic into a thermoset material by creating three-dimensional molecular bonds between adjacent PE chains.
There are three primary methods for achieving cross-linking:
Peroxide Cross-Linking: Organic peroxides decompose at high temperatures, creating free radicals that form bonds between PE chains.
Silane Cross-Linking: PE is grafted with silane compounds, then exposed to moisture which triggers the cross-linking reaction.
Irradiation Cross-Linking: High-energy electron beams or gamma radiation create free radicals that form inter-chain bonds.
The resulting material maintains the basic PE structure but with a three-dimensional network that significantly enhances thermal and electrical properties.
4.2. Key Properties
Higher Thermal Rating
Continuous Operating Temperature: 90-110°C (standard XLPE)
Emergency Overload: Up to 140°C for short periods
Short-Circuit Rating: Can withstand up to 250°C for very brief durations
Low Temperature Performance: Maintains flexibility down to -40°C
Improved Dielectric Performance
Dielectric Strength: 22-35 kV/mm
Volume Resistivity: 10¹⁶-10¹⁸ Ω·cm
Low Dielectric Losses: Lower dissipation factor than PVC
Suitable for Medium to High Voltage: Commonly used from 600V up to 500kV
Moisture and Chemical Resistance
Water Tree Resistance: Special formulations resist water treeing phenomenon
Hydrophobic Surface: Naturally repels water
Chemical Stability: Excellent resistance to oils, chemicals, and solvents
Low Water Absorption: Typically below 0.1%
Mechanical Robustness
Tensile Strength: 12-25 MPa
Elongation at Break: 200-500%
Abrasion Resistance: Good to excellent
Environmental Stress Crack Resistance: Superior to non-cross-linked PE
4.3. Typical Applications
Medium and High Voltage Power Distribution: Underground and overhead power lines
Renewable Energy: Solar farm and wind turbine connections
Submarine Cables: Undersea power transmission
Oil and Gas Industry: Downhole pumps and offshore platform wiring
Railway Systems: Trackside power distribution
Nuclear Facilities: Where radiation resistance is required
Data Centers: Power distribution in mission-critical facilities
4.4. Pros & Cons
Advantages
Superior Thermal Performance: Withstands higher operating temperatures
Excellent Electrical Properties: Higher voltage capability and lower losses
Long Service Life: Typically 30+ years under proper conditions
No Plasticizers: Does not harden or become brittle with age
Chemical and Environmental Resistance: Performs well in harsh conditions
Low Smoke Zero Halogen Options: Available for critical installations
Disadvantages
Higher Cost: More expensive than PVC both in materials and processing
More Complex Processing: Requires additional cross-linking step
Less Flexible: Generally stiffer than PVC, requiring larger bending radii
Installation Challenges: More difficult to terminate and joint
Limited Flame Retardancy: Requires flame-retardant additives
Recycling Difficulties: Thermoset nature complicates end-of-life recycling
5. Comparative Analysis
5.1. Electrical Performance
When comparing electrical properties, XLPE demonstrates clear advantages for high-performance applications:
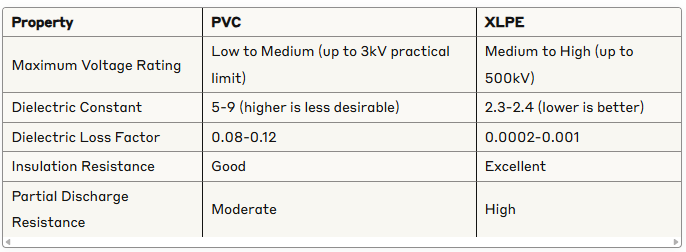
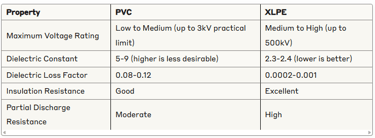
XLPE's superior dielectric properties make it the preferred choice for high-voltage applications and situations where electrical efficiency is critical. PVC remains adequate and cost-effective for lower voltage requirements where its other properties (flexibility, flame retardance) may be more valuable.
5.2. Thermal Endurance
Temperature handling capability represents one of the most significant differences between these materials:
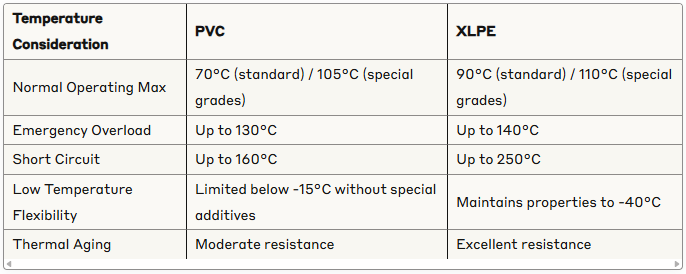
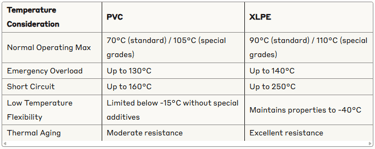
XLPE's superior thermal endurance derives from its cross-linked structure, which prevents the material from melting even at temperatures well above its crystalline melting point. This characteristic is particularly valuable in applications with cyclic loading or potential overload conditions.
5.3. Mechanical Durability
Both materials offer distinct mechanical characteristics suited to different applications:
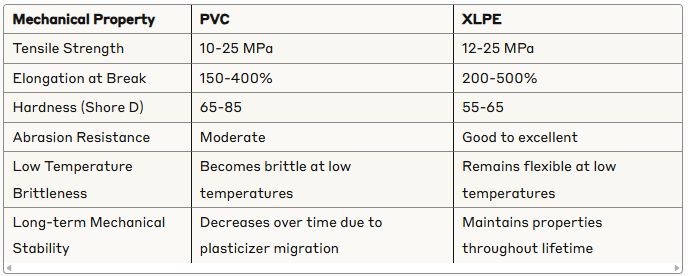
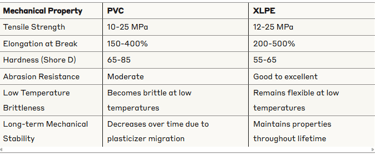
PVC's initial flexibility can be an advantage during installation, but XLPE offers better long-term mechanical stability without the concerns of plasticizer migration or environmental stress cracking.
5.4. Environmental Resistance
Environmental factors can significantly impact cable performance and longevity:
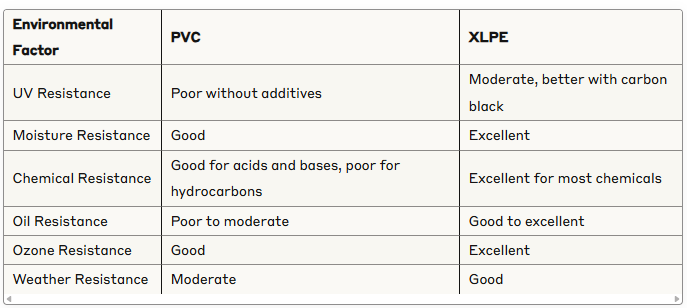
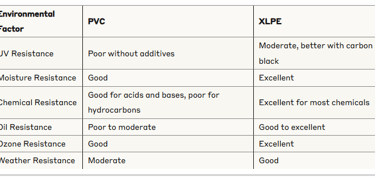
XLPE generally offers superior environmental resistance across most categories, making it especially suitable for outdoor and harsh environment installations. However, both materials can be formulated with additives to enhance specific resistance properties.
5.5. Installation Considerations
Practical installation factors often impact material selection:
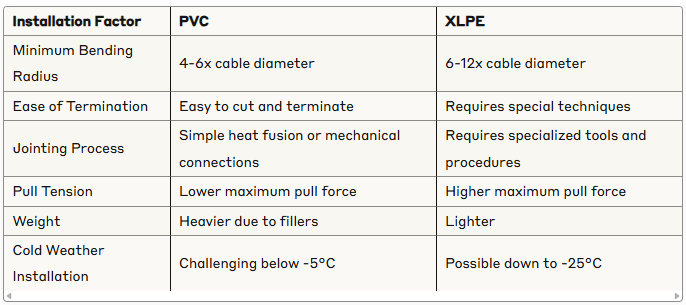
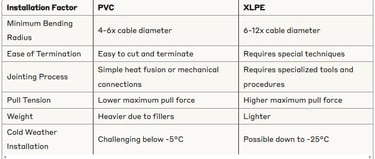
PVC's superior flexibility and ease of termination make it advantageous for installations with space constraints or frequent bends. XLPE's stiffness requires more careful handling but provides advantages in pulling strength and cold-weather installation.
5.6. Cost & Lifecycle
Economic considerations often drive the final decision:
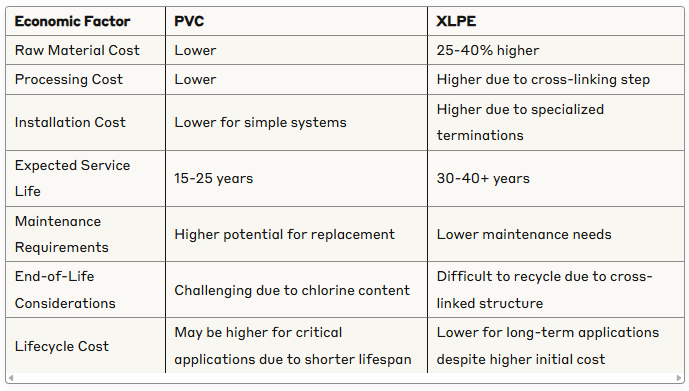
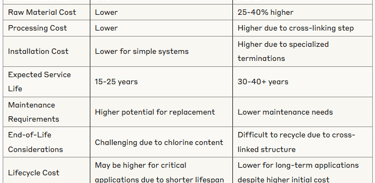
While PVC offers lower upfront costs, XLPE often provides better lifetime value for critical installations or difficult-to-access locations where replacement costs would be significant.

6. Application Scenarios & Selection Guide
6.1. Low-Voltage vs. Medium-Voltage vs. High-Voltage
Low-Voltage Applications (≤1kV)
PVC Recommended For: Residential wiring, appliance connections, control circuits, temporary installations, cost-sensitive projects
XLPE Recommended For: Industrial environments with thermal stress, outdoor installations, critical infrastructure, harsh chemical environments
Medium-Voltage Applications (1kV-33kV)
PVC Limited Applications: Indoor distribution up to 3kV in non-critical settings
XLPE Recommended For: Power distribution networks, industrial plants, commercial buildings, renewable energy collection systems
High-Voltage Applications (>33kV)
PVC Not Suitable
XLPE Standard Choice: Transmission lines, grid infrastructure, large renewable projects, interconnectors
6.2. Indoor vs. Outdoor vs. Subterranean
Indoor Applications
PVC Advantages: Cost-effective, flame-retardant, sufficient for controlled environments
XLPE Applications: Data centers, industrial facilities with high ambient temperatures, critical infrastructure
Outdoor Applications
PVC Limitations: Degrades with UV exposure, temperature fluctuations challenging
XLPE Advantages: Weather resistance, thermal stability across seasons, UV resistance with proper additives
Subterranean Applications
PVC Considerations: Limited current carrying capacity, potential plasticizer leaching
XLPE Advantages: Moisture resistance, higher ampacity, chemical stability, long service life
6.3. Special Environments
Marine Applications
PVC: Limited to above-deck non-critical applications
XLPE: Preferred for underwater cables, ship-to-shore connections, offshore platforms due to moisture and salt resistance
Petrochemical Industry
PVC: Generally unsuitable due to hydrocarbon exposure
XLPE: Standard for hazardous areas, excellent chemical resistance, higher temperature rating
Renewable Energy
PVC: Limited to balance-of-system wiring in protected areas
XLPE: Solar interconnects, wind turbine connections, exposed array wiring, long-distance collection systems
6.4. Decision Flowchart
When selecting between PVC and XLPE, consider the following decision path:
Voltage Requirement
Above 3kV? → XLPE
Below 3kV? → Continue to next factor
Operating Temperature
Above 70°C continuous? → XLPE
Below 70°C continuous? → Continue to next factor
Installation Environment
Outdoor/Underground/Harsh? → XLPE preferred
Controlled indoor? → Continue to next factor
Flexibility Requirements
Frequent bending/tight spaces? → PVC advantage
Static installation? → Either suitable
Fire Performance Required
High flame retardance needed? → PVC advantage (or special XLPE formulation)
Low smoke/zero halogen needed? → Special XLPE or PVC formulations
Expected Service Life
25+ years required? → XLPE preferred
Shorter term installation? → PVC may be more cost-effective
Budget Constraints
Tight initial budget? → PVC
Lifecycle cost focus? → XLPE often better long-term value
7. Future Trends in Cable Insulation
7.1. Emerging Polymers and Nanocomposites
The future of cable insulation is being shaped by innovative materials research:
Polypropylene-Based Insulation: Offering excellent electrical properties with lower environmental impact than traditional materials
Thermoplastic Elastomers (TPEs): Combining the processing ease of thermoplastics with rubber-like elasticity
Nanocomposites: Adding nanoparticles (silica, zinc oxide, carbon nanotubes) to enhance specific properties:
Improved thermal conductivity
Enhanced partial discharge resistance
Reduced water tree growth
Increased mechanical strength
Bio-Based Polymers: Developing insulation materials from renewable sources to reduce petrochemical dependence
These innovations aim to address limitations in current materials while maintaining or improving performance characteristics.
7.2. Sustainability & Recycling
Environmental concerns are driving significant changes in the cable industry:
Halogen-Free Formulations: Moving away from halogenated compounds like PVC to reduce toxic emissions during fires
Recyclable Cross-Linked Systems: Developing thermally reversible cross-links that allow thermoset recycling
Eco-Design Approaches: Life-cycle assessment driving material selection and design
End-of-Life Management: Improved techniques for separating and processing cable materials
Reduced Heavy Metal Content: Eliminating lead, cadmium, and other harmful stabilizers
Energy-Efficient Manufacturing: Lower temperature processes and reduced energy consumption
These efforts reflect the industry's response to increasing regulatory pressure and market demand for sustainable solutions.
7.3. Smart Cables with Embedded Sensors
Cable technology is evolving beyond passive power transmission to incorporate active monitoring capabilities:
Distributed Temperature Sensing: Fiber optics embedded within cable construction to monitor temperature along entire length
Partial Discharge Detection: Built-in sensors to identify insulation degradation before failure
Mechanical Strain Monitoring: Technology to detect excessive pulling or crushing forces
Water Ingress Detection: Systems that alert to moisture penetration
Load Monitoring: Real-time current measurement capabilities
Predictive Maintenance: AI-based systems using sensor data to forecast potential failures
These "smart cable" technologies promise to revolutionize grid management and maintenance strategies, potentially extending service life while reducing catastrophic failures.
8. Conclusion
8.1. Recap of Key Differences
PVC and XLPE represent different approaches to cable insulation, each with distinct advantages:
PVC excels in: Cost-effectiveness, flexibility, flame retardancy, ease of processing and termination
XLPE dominates in: Thermal performance, electrical properties, long-term stability, environmental resistance
The fundamental molecular difference—PVC as a thermoplastic versus XLPE as a thermoset—drives many of these performance distinctions and determines their appropriate applications.
8.2. Practical Recommendations
When selecting between these insulation materials:
Choose PVC when: Initial cost is critical, installation involves tight bends, flame retardancy is essential, and operating conditions are moderate
Choose XLPE when: Long service life is required, operating temperatures are elevated, installation environment is harsh, or voltage requirements exceed 3kV
Consider Special Formulations: Both materials are available in enhanced versions (e.g., low-smoke PVC, flame-retardant XLPE) that may address specific application needs
Look Beyond Initial Cost: Calculate total lifecycle expenses including potential replacement and downtime when making selections
Consult Standards: Reference applicable national and international standards (IEC, ASTM, UL) for specific application requirements
8.3. Final Thoughts on Evolving Industry Needs
The electrical cable industry continues to evolve in response to changing technology demands and environmental considerations. While PVC and XLPE remain the dominant insulation materials today, ongoing research into nanocomposites, eco-friendly alternatives, and smart cable technologies will likely reshape the landscape in coming decades.
For engineers and end-users alike, staying informed about these developments will be crucial to making optimal decisions as applications become more demanding and sustainability requirements more stringent. The "battle of the sleeves" between PVC and XLPE illustrates a broader principle in engineering: material selection always involves balancing competing priorities—cost versus performance, flexibility versus durability, and traditional solutions versus emerging technologies.
By understanding the fundamental properties and appropriate applications of these insulation materials, decision-makers can ensure safe, efficient, and cost-effective electrical systems that meet both current needs and future challenges.