Type 2S 1.1/1.1 kV & 3.3/3.3 kV Individually Screened Mining Cables
In the challenging environment of underground mining operations across Australia, power distribution isn't just a matter of convenience—it's a critical safety and operational concern. The harsh conditions found in mines demand specialized electrical solutions that can withstand extreme mechanical stress, moisture, dust, and potentially explosive atmospheres while delivering reliable power to essential equipment. Type 2S individually screened mining cables represent one of the most important developments in mining electrical infrastructure. These specialized cables are designed specifically for the unique demands of underground mining environments, where standard industrial cables would quickly fail. The "Type 2S" designation refers to the construction standard under AS/NZS 1972:2006, while "individually screened" indicates that each power core within the cable has its own metallic screening layer—a crucial feature for both electrical performance and safety in mining environments.
5/20/20258 min read
1. Introduction
Context & Importance
In the challenging environment of underground mining operations across Australia, power distribution isn't just a matter of convenience—it's a critical safety and operational concern. The harsh conditions found in mines demand specialized electrical solutions that can withstand extreme mechanical stress, moisture, dust, and potentially explosive atmospheres while delivering reliable power to essential equipment.
Type 2S individually screened mining cables represent one of the most important developments in mining electrical infrastructure. These specialized cables are designed specifically for the unique demands of underground mining environments, where standard industrial cables would quickly fail. The "Type 2S" designation refers to the construction standard under AS/NZS 1972:2006, while "individually screened" indicates that each power core within the cable has its own metallic screening layer—a crucial feature for both electrical performance and safety in mining environments.
Type 2S 1.1/1.1 kV & 3.3/3.3 kV Individually Screened Mining Cables


2. Application Scenarios
2.1 Underground Coal Mines
Australian coal mining operations present particularly demanding conditions for electrical infrastructure. Type 2S cables excel in these environments by powering critical equipment such as:
Longwall shearers: These massive cutting machines require substantial power delivery through cables that can withstand constant movement and coal dust exposure. The individually screened design prevents electrical faults that could potentially ignite coal dust or methane gas.
Belt conveyors: The backbone of material handling in coal mines, these systems require reliable power distribution that can resist the accumulated coal dust while maintaining operational integrity.
Water pumps: Essential for mine dewatering, these systems must operate continuously in wet conditions where standard cables would quickly deteriorate.
The individually screened design provides critical protection against water ingress, coal dust accumulation, and mechanical damage—all common challenges in Australian coal mining operations.
2.2 Hard-Rock Mines
Australia's vast hard-rock mining sector, including operations extracting gold, copper, nickel, and iron ore, presents different but equally challenging conditions:
High-torque drilling equipment: Rock drills and boring machines create extreme vibration and require consistent power delivery through cables that can withstand these mechanical stresses.
Load-haul-dump (LHD) machines: These vehicles operate in tight spaces with limited visibility, increasing the risk of cable damage from crushing or abrasion.
Rock crushers: These high-power applications generate substantial dust and vibration while requiring reliable power transmission.
In these environments, Type 2S cables must resist not only physical damage but also exposure to hydraulic fluids, lubricants, and other chemicals common in hard-rock mining operations. The heavy-duty CPE (Chlorinated Polyethylene) outer sheath provides excellent resistance to these substances while maintaining flexibility.
2.3 Mobile & Semi-Mobile Equipment
Modern Australian mining operations rely heavily on equipment that moves or repositions frequently:
Draglines: These massive earth-moving machines require cables that can withstand repeated flexing and coiling while delivering substantial power.
Shuttle cars: Used to transport coal or ore between mining faces and conveyor systems, these vehicles subject cables to repeated flexing and potential crushing.
Roof support systems: These hydraulic systems move incrementally as mining progresses, requiring cables that can accommodate this movement without damage.
The individually screened design, combined with flexible construction, allows Type 2S cables to maintain electrical integrity even when subjected to repeated bending and flexing. This flexibility is achieved through the combination of finely stranded conductors, elastomeric insulation, and carefully designed internal structure.
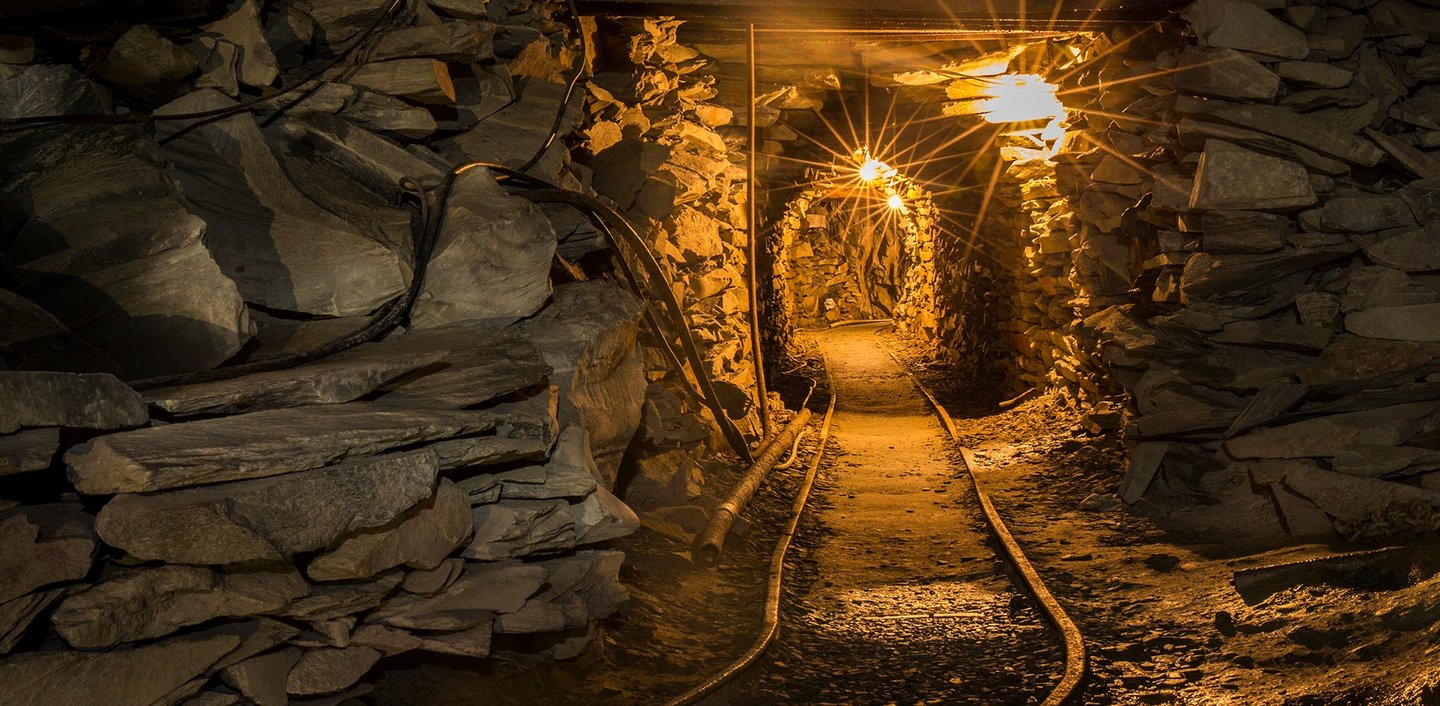
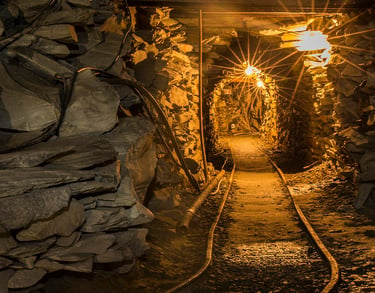
3. Electrical Parameters
3.1 Voltage Ratings
The voltage rating of mining cables is expressed in the format of X/Y kV, where:
X represents the phase-to-phase voltage rating
Y represents the phase-to-earth voltage rating
For Type 2S cables, the common ratings are:
1.1/1.1 kV cables: These are designed for standard mining operations where equipment operates at 1000V or less. The matching values (1.1/1.1) indicate that the cable has full insulation between phases and from phase to earth, providing additional safety in the event of a fault.
3.3/3.3 kV cables: These higher-voltage cables are used for powering larger equipment or for longer distribution runs where voltage drop becomes a concern. The increased insulation thickness (3.0mm versus 1.2-1.6mm for 1.1kV cables) provides the necessary electrical separation for safe operation at these higher voltages.
The choice between these voltage ratings depends on several factors including:
The power requirements of the equipment being supplied
The distance between power source and equipment
The potential for voltage fluctuations during operation
Local mining regulations and safety standards
Australian mining operations typically select the appropriate voltage based on both equipment requirements and site-specific safety protocols.
3.2 Conductor & Insulation
The conductors in Type 2S mining cables are made from stranded tinned annealed copper, offering several advantages:
The fine stranding (e.g., 77/0.40mm for 10mm² conductors) provides excellent flexibility
Tinning improves corrosion resistance in humid mine environments
The annealing process ensures optimal conductivity and flexibility
Conductor sizes typically range from 10mm² to 120mm², with larger sizes used for equipment with higher power demands or longer cable runs. The specific cross-sectional area is selected based on:
The maximum current the cable must carry
The acceptable voltage drop over the cable length
The ambient temperature in the installation area
The duty cycle of the connected equipment
The insulation material is primarily EPR (Ethylene Propylene Rubber), which offers excellent:
Electrical properties over a wide temperature range
Resistance to moisture absorption
Flexibility for repeated movement
Long service life in harsh environments
The insulation thickness varies with voltage rating, with 3.3/3.3kV cables requiring significantly thicker insulation (3.0mm) compared to 1.1/1.1kV cables (1.2-1.6mm).
3.3 Screening & Shielding
The defining feature of Type 2S mining cables is their individual core screening. Each power conductor is surrounded by its own metallic screen, typically constructed from tinned annealed copper braiding interwoven with polyester yarn. This composite screen serves multiple critical functions:
Electrical safety: In the event of insulation damage, fault current is contained and directed to earth
EMI reduction: The screens minimize electromagnetic interference between cores and from external sources
Uniform electric field: The screen helps distribute electrical stress evenly around the insulation
Touch potential control: In the event of damage, the screen helps prevent dangerous touch voltages from developing
The screen area is carefully sized according to the conductor size and voltage rating, typically ranging from 7.9mm² to 47.5mm² for the larger conductors. This ensures adequate capacity to carry fault currents safely to earth.
3.4 Temperature & Environmental Ratings
Type 2S mining cables conform to stringent Australian standards for environmental performance:
Temperature range: These cables are typically designed to operate in ambient temperatures from -25°C to +90°C, covering the full range of conditions found in Australian mining operations from tropical northern regions to cooler southern areas.
Fire performance: In accordance with AS/NZS 1125, these cables offer limited flame propagation, reduced smoke emission, and minimal halogen content to enhance safety during fire events.
Mechanical resistance: The heavy-duty CPE outer sheath provides excellent resistance to:
Abrasion from rough surfaces
Impact from falling objects
Crushing under vehicle wheels
Cutting from sharp rock edges
Chemical resistance: The CPE sheath offers exceptional resistance to:
Mineral oils and hydraulic fluids
Diesel fuel and petrol splashes
Weak acids and alkalis
UV exposure during surface installations
These ratings are verified through rigorous testing to ensure compliance with AS/NZS 1972:2006, AS/NZS 1125, and AS/NZS 3808 standards, which are specifically developed for Australian mining conditions.
3.5 Dimensions and Weight
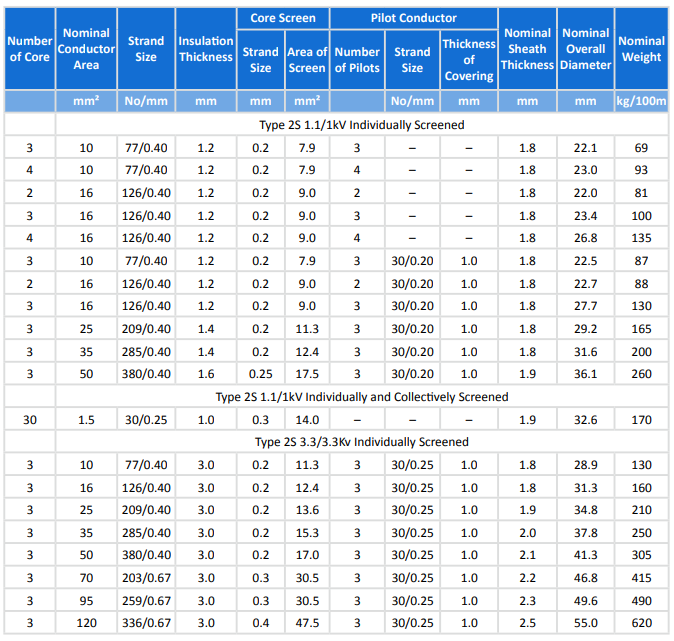

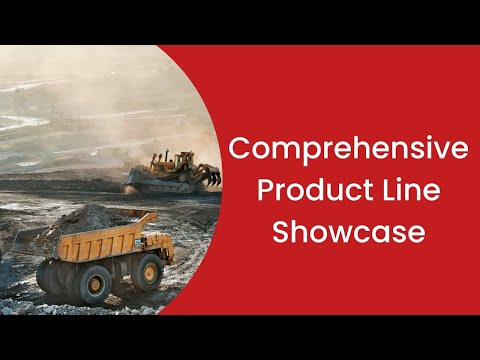
4. FAQ: Common Mining-Tailored Questions
Q: Why individually screened cables instead of common-screen?
A: Individual screening provides several critical advantages in mining environments. Unlike common-screened cables where all cores share a single screen, individual screening:
Prevents circulating currents between cores that can cause overheating
Isolates faults to a single core, allowing continued operation of remaining phases in some situations
Provides better EMI protection for sensitive control circuits
Enhances mechanical protection for each core individually
This design is particularly important in Australian mining operations where equipment often operates at the limits of its rated capacity, and where maintenance access can be challenging.
Q: How do I know if my 1.1 kV cable is overloaded?
A: Several indicators suggest a Type 2S cable is operating beyond its capacity:
Overheating of the outer sheath (above 70°C) during normal operation
Discoloration or embrittlement of the CPE sheath
Reduced flexibility or cracking of the outer layer
Premature insulation breakdown or intermittent faults
Circuit breaker nuisance tripping without apparent cause
Modern Australian mining operations often employ thermal imaging cameras during routine inspections to identify hotspots along cable runs before failure occurs. If the cable surface temperature exceeds 60°C during normal operation, this suggests approaching the operational limits.
Q: What maintenance practices extend cable life underground?
A: To maximize service life in challenging Australian mining conditions:
Conduct regular visual inspections for mechanical damage, particularly at connection points and where cables pass through bulkheads
Ensure proper cleaning of mud, coal dust, and other debris that can trap heat and accelerate degradation
Maintain proper bend radius controls (typically 6-8 times the cable diameter for dynamic applications)
Properly secure cables to prevent excessive tension or movement
Avoid pooling water around cable installations through proper drainage systems
Implement cable management systems that prevent crushing by vehicles or falling rock
Document cable history including installation date, load profile, and any damage/repair events
Australian mining companies typically implement comprehensive cable management programs that include regular testing of insulation resistance and screen continuity.
Q: How to handle accidental cuts or abrasions?
A: When Type 2S cables sustain damage:
For minor damage limited to the outer sheath:
Clean the damaged area thoroughly and assess penetration depth
Apply appropriate vulcanizing repair tape compatible with CPE sheath material
Protect the repair with additional mechanical protection if in a high-traffic area
For more serious damage affecting screens or insulation:
Implement temporary emergency procedures to de-energize the cable
Use manufacturer-approved splice kits designed specifically for mining cables
Ensure repair work is conducted by qualified personnel in accordance with AS/NZS standards
Consider full replacement if damage is extensive or affects multiple cores
Many Australian mining operations maintain emergency repair kits specifically designed for field repairs of Type 2S cables, allowing rapid restoration of service when replacement isn't immediately possible.
Q: Can these cables withstand methane or explosive atmospheres?
A: Type 2S cables themselves are not intrinsically safe. Their use in potentially explosive atmospheres must comply with:
The requirements of Australian coal mining regulations regarding explosion protection
Installation within appropriate gas-proof conduit systems where required
Integration with properly certified explosion-protected equipment
Regular inspection and testing to ensure continued integrity
In Australian coal mining operations, these cables are typically used in conjunction with certified explosion-protected connection systems that maintain the integrity of the explosion protection system. This may include specialized glands, junction boxes, and termination methods designed to prevent ignition of explosive atmospheres.
5. Conclusion
Type 2S individually screened mining cables represent a critical element in the safe and reliable operation of Australian mining equipment. Their specialized construction, combining flexible stranded conductors, EPR insulation, individual composite screens, and heavy-duty CPE outer sheath, provides the durability and electrical performance required in challenging underground environments.
As Australian mining operations continue to push deeper and into more challenging terrain, the demands on electrical infrastructure will only increase. Future developments in mining cable technology are likely to focus on:
Higher voltage ratings to support more powerful equipment and longer distribution runs
Enhanced monitoring capabilities, including fiber optic elements for temperature and strain sensing
Improved fire performance with reduced smoke and zero halogen materials
Greater flexibility and durability for increasingly automated mining systems
Understanding the construction, application, and maintenance requirements of these specialized cables is essential for mining engineers and maintenance personnel working to ensure the safety and productivity of Australia's vital mining industry.