Understanding AS/NZS 1802 Type 240 1.1 kv Mining Cablesv
In the challenging environment of mining operations, reliable power distribution is critical for both productivity and safety. Mining cables form the backbone of these power systems, delivering electricity to essential machinery in some of the harshest industrial conditions. This article aims to demystify the AS/NZS 1802 Type 240 1.1 cable specification, providing mining professionals, engineers, and safety personnel with a clear understanding of these specialized cables.
4/25/20255 min read
Understanding AS/NZS 1802 Type 240 1.1 Mining Cables
1. Introduction
In the challenging environment of mining operations, reliable power distribution is critical for both productivity and safety. Mining cables form the backbone of these power systems, delivering electricity to essential machinery in some of the harshest industrial conditions. This article aims to demystify the AS/NZS 1802 Type 240 1.1 cable specification, providing mining professionals, engineers, and safety personnel with a clear understanding of these specialized cables.
2. What is AS/NZS 1802 Type 240 1.1 Mining Cable?
The AS/NZS 1802:2003 standard is a joint Australian and New Zealand standard that specifies requirements for electric cables used in mining applications, particularly reeling and trailing cables. These cables are designed to withstand the unique challenges of mining environments while ensuring reliable power transmission and safety.
The "Type 240" designation refers to a specific design for flexible trailing cables with three power cores, three large interstitial pilots, and large core screens that provide low resistance earthing. This design makes them particularly suitable for mining applications where both power delivery and safety monitoring are essential.
The "1.1" in the type code indicates a voltage rating of 1.1 kV (1100 volts), making these cables suitable for many standard mining equipment applications that operate at this voltage level.
3. Application Scenarios
Underground Mining Operations
Type 240 1.1 cables are frequently used to power heavy machinery such as shuttle cars, continuous miners, and loaders in underground mining operations. Their design makes them ideal for feeding power to machinery or providing longwall supply in coal mining operations.
Open-cut Mining Sites
In open-cut mining, these cables can power draglines, drills, and excavators that require flexible power connections as they move throughout the mining site.
Mobile and Relocatable Equipment
The flexible nature of these cables makes them perfect for equipment that needs to be moved regularly. The cables can follow the machinery as it changes location within the mine.
Harsh Environments
Mining environments expose cables to mechanical stress, moisture, chemicals, and abrasive materials. Type 240 1.1 cables are specifically designed to withstand these conditions while maintaining electrical integrity.
4. Electrical and Mechanical Parameters
Voltage Rating
Type 240 1.1 cables are rated for 1.1 kV operation, suitable for many standard mining equipment power requirements.
Conductor Size
According to the Feichun Cable specifications, these cables are available in various conductor sizes ranging from 6mm² to 300mm². The conductors are made of flexible stranded tinned annealed copper, enhancing both flexibility and corrosion resistance.
Temperature Rating
While not explicitly stated in the provided document, mining cables typically have a temperature rating of 90°C for normal operation.
Insulation and Sheathing
Insulation: EPR (Ethylene Propylene Rubber) provides excellent electrical properties and flexibility
Conductor Screen: Semiconductive compound (for cables with voltage ratings of 3.3/3.3kV and above)
Insulation Screen: Semiconductive elastomer
Sheath: Heavy duty PCP (Polychloroprene) sheath, with CPE/CSP (Chlorinated Polyethylene/Chlorosulfonated Polyethylene) available upon request
Composite Screen (Earth Conductor)
Tinned annealed copper braiding interwoven with polyester yarn provides effective earthing and mechanical strength.
Pilot Cores
Three EPR-covered flexible stranded tinned copper conductors serve as pilot cores, which are essential for safety monitoring systems.
Physical Dimensions
For example, a 50mm² Type 240.1 cable has:
Insulation thickness: 1.7mm
Sheath thickness: 5.0mm
Overall diameter: 47.7mm
Weight: 404 kg/100m
Cable Flexibility
The multi-stranded construction (e.g., 380/0.40 for 50mm² conductor) provides excellent flexibility for the repeated movement required in mining applications.
5. Common Issues in Mining Applications and Cable Challenges
Mechanical Damage from Rough Terrain
Challenge: Mining cables must withstand dragging over rough surfaces, impact from falling objects, and crushing forces. Solution: The heavy-duty PCP sheath (3.8mm to 10.4mm thick, depending on cable size) provides excellent protection against abrasion and mechanical damage.
Moisture Ingress or Chemical Exposure
Challenge: Underground mines often have wet conditions, and cables may be exposed to various chemicals. Solution: The PCP outer sheath is resistant to water, oils, and many chemicals, helping to protect the electrical integrity of the cable.
Cable Fatigue from Repeated Flexing
Challenge: Trailing cables must bend repeatedly as machinery moves. Solution: The flexible stranded copper conductors (e.g., 209/0.40 for 25mm² cable) and elastomeric insulation materials allow for repeated flexing without conductor fatigue or insulation cracking.
Electrical Failure Due to Overloading or Improper Grounding
Challenge: Mining equipment often operates under varying loads, and proper grounding is critical for safety. Solution: The large core screens provide low resistance earthing, and the three interstitial pilots allow for continuous monitoring of the earth continuity and other safety parameters.
6. Frequently Asked Questions (FAQ)
Q1: Can Type 240 1.1 cables be used in explosive atmospheres?
A1: Only if certified for explosive environments. These cables must comply with additional mining safety standards (e.g., IECEx) if used in potentially explosive atmospheres. Always check the specific certification requirements for your application.
Q2: What's the difference between Type 240 and Type 241?
A2: Type 240 is typically used for trailing cable applications, while Type 241 may be designed for higher stress or different connection types. Type 240 specifically contains three large pilots and large core screens for low resistance earthing.
Q3: How often should these cables be inspected or replaced?
A3: It depends on usage conditions, but regular visual and electrical testing is recommended—typically every 3–6 months. Look for signs of mechanical damage, sheath degradation, or changes in electrical parameters.
Q4: Can these cables be repaired underground?
A4: Temporary splicing is possible, but permanent repairs must be done by certified technicians following safety protocols. Always follow local mining regulations regarding cable repairs.
Q5: Is there a maximum length for Type 240 1.1 cables?
A5: There's no absolute maximum, but voltage drop and mechanical handling limitations apply. Engineering evaluation is necessary to determine the appropriate length for specific applications, considering factors such as load current, voltage drop, and machinery movement range.
7. Conclusion
AS/NZS 1802 Type 240 1.1 mining cables represent specialized engineering designed to meet the unique challenges of mining environments. Their construction with flexible copper conductors, EPR insulation, and robust PCP sheathing provides the electrical performance, mechanical durability, and safety features essential for mining operations.
Proper selection, installation, and maintenance of these cables are critical not only for operational efficiency but also for the safety of mining personnel. By understanding the specifications and applications of Type 240 1.1 cables, mining operators can ensure reliable power distribution in their operations while minimizing downtime and safety risks.
Whether powering continuous miners in underground coal operations or supplying electricity to draglines in open-cut mines, these specialized cables form a vital link in the mining power distribution system, engineered to withstand the harsh conditions while maintaining electrical integrity and safety monitoring capabilities.
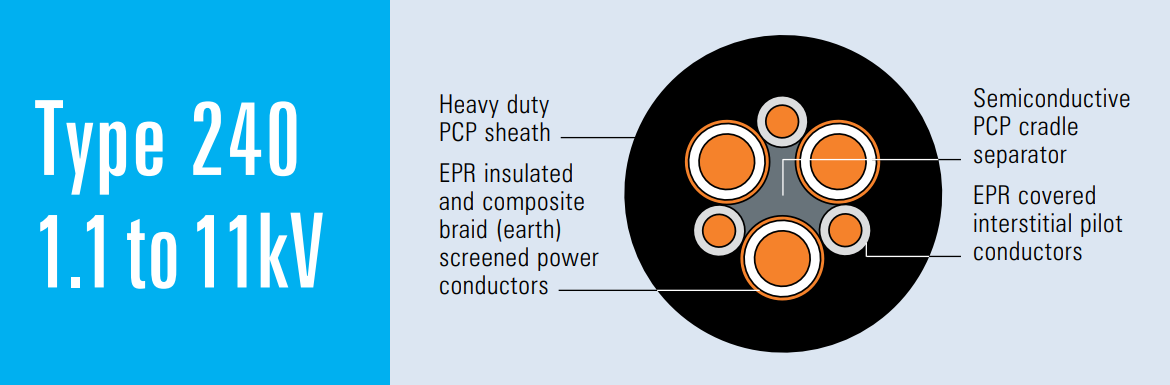
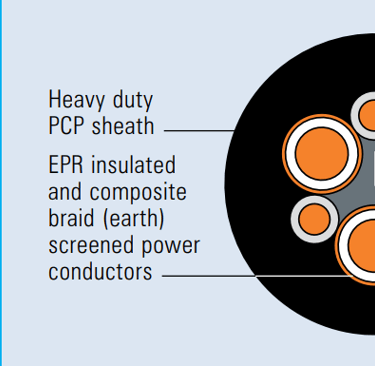