Understanding BS 6708 Type 11 Mining Cable
Comprehensive guide to BS 6708 Type 11 mining cables covering applications, electrical specifications, installation requirements, and frequently asked questions for UK mining operations.
5/27/202517 min read
Understanding BS 6708 Type 11 Mining Cabl
Introduction
The mining industry demands electrical equipment that can withstand the most challenging environments imaginable. Deep underground, where explosive gases lurk in poorly ventilated spaces and heavy machinery operates under extreme conditions, standard electrical cables simply cannot cope. This is where specialised mining cables, particularly those conforming to British Standard BS 6708, become absolutely essential for safe and reliable operations.
British Standard BS 6708 represents decades of engineering expertise and safety research, establishing comprehensive requirements for flexible cables used specifically in mining and quarrying operations. This standard addresses the unique challenges that mining environments present: the constant threat of explosive atmospheres, the presence of corrosive chemicals and oils, extreme temperature variations, and the mechanical stresses imposed by heavy, moving equipment.
Within the BS 6708 family of cables, Type 11 cables occupy a particularly important position. These cables serve as the electrical lifeline for some of the most critical equipment in mining operations, including the powerful excavating machines that extract valuable materials from the earth, the crushing equipment that processes raw materials, and the shuttle cars that transport materials through narrow underground passages. Understanding the capabilities and proper application of BS 6708 Type 11 cables is crucial for anyone involved in mining operations, from electrical engineers designing power distribution systems to maintenance technicians ensuring equipment reliability.
The significance of Type 11 cables extends beyond their immediate function as power conductors. They represent a carefully engineered balance between flexibility and durability, designed to withstand both the mechanical stresses of dynamic equipment movement and the harsh environmental conditions that characterise mining operations. Their construction incorporates multiple layers of protection, each serving a specific purpose in ensuring long-term reliability and safety in explosive atmospheres.
Applications of BS 6708 Type 11 Cable
Primary Use Cases in Mining Operations
BS 6708 Type 11 cables find their most critical applications in powering the heavy machinery that forms the backbone of modern mining operations. These cables are specifically engineered to supply reliable electrical power to excavating and crushing machines, which represent some of the most power-hungry and mechanically demanding equipment in the mining industry. The excavating machines, including continuous miners and roadheaders, require substantial electrical power to drive their cutting heads through rock and coal seams, whilst simultaneously managing the conveyor systems that remove extracted material.
Shuttle cars present another crucial application area for Type 11 cables. These mobile vehicles transport extracted materials through underground tunnels and require flexible power connections that can accommodate their constant movement whilst maintaining electrical integrity. The cables must withstand the repeated flexing and potential impact damage that occurs as these vehicles navigate through confined underground spaces, often in conditions where dust and moisture are prevalent.
Coal cutters represent perhaps the most demanding application for these cables. These machines operate at the coal face, where conditions are at their most extreme. They must cut through varying geological formations whilst being supplied with consistent electrical power through cables that may be dragged across rough surfaces, exposed to coal dust, and subjected to the mechanical stresses of the cutting operation itself. The Type 11 cable's robust construction ensures that power delivery remains stable even under these challenging conditions.
At-face equipment operations encompass a broader category of machinery that operates in the immediate vicinity of active extraction work. This includes roof bolters, which secure the mine ceiling for safety, ventilation fans that maintain air quality, and conveyor systems that transport materials away from the working face. Each of these applications demands cables that can maintain electrical integrity whilst being exposed to the dust, moisture, and potential mechanical damage that characterises the working face environment.
Operational Environments and Conditions
The environments where BS 6708 Type 11 cables operate present unique challenges that standard industrial cables cannot address. Deep mines create conditions where explosive gases, particularly methane, can accumulate in poorly ventilated areas. These atmospheres require cables with specialised construction features that minimise the risk of electrical arcing or sparking that could trigger catastrophic explosions. The Type 11 cable's design incorporates screening and earthing systems that help manage electromagnetic interference and provide safe paths for fault currents.
Temperature extremes present another significant challenge in mining operations. Underground environments can range from near-freezing conditions in deep shafts to elevated temperatures in areas where geothermal heating occurs or where heavy machinery generates substantial heat. Surface mining operations expose cables to even wider temperature variations, from sub-zero winter conditions to intense summer heat. BS 6708 Type 11 cables are engineered to maintain their electrical and mechanical properties across this entire temperature range, ensuring reliable operation regardless of environmental conditions.
The presence of various chemicals and oils in mining environments creates additional challenges for cable construction. Hydraulic fluids from heavy machinery, lubricating oils, and various chemical solutions used in mineral processing can all attack conventional cable materials, leading to premature failure. The heavy-duty chloroprene outer sheath of Type 11 cables provides excellent resistance to these substances, maintaining cable integrity even when exposed to spills or continuous contact with contaminated surfaces.
Moisture management represents another critical consideration in mining cable applications. Underground environments often have high humidity levels, and water infiltration is a constant concern. Surface operations may expose cables to direct rainfall or flooding conditions. The construction of Type 11 cables includes moisture barriers and materials selection that prevents water ingress from compromising electrical performance or causing internal corrosion.
Installation Considerations and Flexibility Requirements
The installation requirements for BS 6708 Type 11 cables reflect the unique demands of mining operations, where equipment must often be installed in confined spaces and may need to be relocated frequently as mining operations progress. The cables are specifically designed to accommodate both fixed installations, where they may be permanently routed through underground tunnels or surface installations, and flexible operations, where they must move with mobile equipment.
For fixed installations, the cables can be installed with tighter bending radii, allowing for more compact routing through existing infrastructure. This flexibility in installation parameters enables engineers to design efficient power distribution systems that make optimal use of available space whilst maintaining safety clearances and accessibility for maintenance. The minimum bending radius of four times the cable diameter for fixed installations represents a carefully calculated balance between mechanical stress management and installation practicality.
Flexible operations present significantly different requirements, where cables must accommodate the dynamic movement of mobile equipment whilst maintaining electrical integrity. The increased minimum bending radius of five times the cable diameter for flexible applications reflects the additional mechanical stresses that occur when cables are repeatedly flexed during normal operation. This design consideration ensures that the internal conductors and insulation systems are not subjected to stress levels that could cause premature failure.
The adaptability of Type 11 cables to dynamic mining equipment movements extends beyond simple flexibility requirements. These cables must withstand the vibrations generated by heavy machinery, the mechanical stresses of being dragged across rough surfaces, and the potential impact damage that can occur in the confined spaces of underground operations. The robust construction of the outer sheath and the careful design of internal cable geometry ensure that these mechanical challenges do not compromise electrical performance.
Electrical and Physical Specifications
Voltage Ratings and Electrical Performance
The electrical specifications of BS 6708 Type 11 cables reflect the demanding requirements of mining equipment power distribution. With a rated voltage of 640/1100 V, these cables are designed to handle the substantial power requirements of heavy mining machinery whilst providing the safety margins necessary for reliable operation in challenging environments. The dual voltage rating indicates the cable's capability to operate in both phase-to-phase and phase-to-earth configurations, providing flexibility in system design and installation.
The test voltage specification of 3 kV represents a critical safety parameter that ensures the cable's insulation system can withstand electrical stresses well beyond normal operating conditions. This test voltage is applied during manufacturing to verify that the insulation system can handle transient overvoltages that may occur during system operation, such as those caused by motor starting currents or switching operations. The substantial margin between operating voltage and test voltage provides confidence in the cable's long-term electrical integrity.
Understanding these voltage specifications is crucial for proper system design, as they determine not only the cable's capability to handle normal operating conditions but also its ability to safely manage fault conditions and electrical transients. The robust insulation system designed to meet these specifications ensures that the cable can continue to operate safely even when subjected to the electrical stresses that characterise industrial mining environments.
Conductor Construction and Materials
The conductor system of BS 6708 Type 11 cables represents a sophisticated approach to balancing electrical performance with mechanical durability. The use of electrolytic copper ensures maximum electrical conductivity, which is essential for minimising power losses and heat generation in high-current applications. The stranded construction, conforming to IEC 60228 Class 5 specifications, provides the flexibility necessary for cables that must accommodate equipment movement whilst maintaining excellent electrical properties.
The tinning of the copper conductors serves multiple important functions in the harsh mining environment. The tin coating provides excellent corrosion resistance, preventing the copper from oxidising when exposed to moisture or corrosive atmospheres. This protection is particularly important in mining applications where cables may be exposed to various chemicals and high humidity conditions over extended periods. Additionally, the tin coating facilitates reliable electrical connections and helps prevent galvanic corrosion when the conductors are terminated to different metal components.
The Class 5 stranding specification indicates a high degree of flexibility in the conductor construction, with many small wires twisted together to form each conductor. This construction method ensures that the conductor can withstand repeated flexing without work-hardening or breaking individual wire strands, which is crucial for applications involving mobile equipment or frequent cable movement.
Insulation and Sheathing Systems
The insulation system of BS 6708 Type 11 cables utilises Ethylene Propylene Rubber (EPR), a material specifically chosen for its excellent electrical properties and environmental resistance. EPR insulation provides superior performance across the wide temperature range encountered in mining operations, maintaining its dielectric properties from the sub-zero conditions of deep shafts to the elevated temperatures that can occur around heavy machinery or in geothermally active areas.
The EPR insulation system offers excellent resistance to electrical tracking and treeing, which are common failure modes in cables exposed to contaminated environments. This resistance is particularly important in mining applications where cables may be exposed to conductive dust, moisture, and various chemicals that can compromise the performance of less robust insulation materials. The material's inherent flexibility also ensures that the insulation system can accommodate the mechanical stresses of cable movement without cracking or developing weak points.
The outer sheath construction represents perhaps the most critical component in protecting the cable from the harsh mining environment. The heavy-duty chloroprene outer sheath provides exceptional resistance to abrasion, chemicals, oils, and environmental exposure. Chloroprene, also known as neoprene, offers an optimal combination of mechanical toughness and chemical resistance that makes it ideal for mining applications.
The abrasion resistance of the chloroprene sheath is particularly important in mining applications where cables may be dragged across rough surfaces, subjected to impact from falling debris, or exposed to the mechanical stresses of heavy equipment operation. The material's toughness ensures that the underlying electrical components remain protected even when the cable is subjected to significant mechanical abuse.
Chemical resistance is another crucial property of the chloroprene sheath, providing protection against the various oils, hydraulic fluids, solvents, and other chemicals commonly encountered in mining operations. This resistance prevents the gradual degradation that would occur with less suitable materials, ensuring long-term cable reliability and reducing maintenance requirements.
Screening and Earthing Configuration
The screening system of BS 6708 Type 11 cables incorporates a sophisticated approach to electromagnetic compatibility and electrical safety. The tinned copper and nylon braided screen over the phase cores provides effective electromagnetic interference (EMI) shielding, which is crucial in mining environments where multiple pieces of electrical equipment operate in close proximity. This screening helps prevent interference between different electrical systems and reduces the potential for electrical noise to affect sensitive control circuits.
The decision to leave the ground core unscreened reflects careful consideration of the cable's intended application and electrical safety requirements. The ground conductor serves as the primary safety earth path, and its unscreened construction ensures that it can effectively carry fault currents without being impeded by screening impedance. This design approach provides optimal safety performance whilst maintaining the EMI benefits of screening for the power-carrying conductors.
The braided construction of the screen provides several advantages over alternative screening methods. The braided design offers excellent flexibility, allowing the screen to accommodate cable movement without degrading its effectiveness. Additionally, the braided construction provides multiple parallel paths for fault currents and screening currents, ensuring reliable performance even if individual braid elements are damaged.
Mechanical Properties and Performance Limits
The mechanical specifications of BS 6708 Type 11 cables reflect the demanding physical environment of mining operations. The maximum operating temperature of 90°C ensures that the cable can handle not only the ambient temperature conditions found in mining environments but also the heat generated by high current flow through the conductors. This temperature rating provides adequate margin for equipment operating at full load even in elevated ambient temperature conditions.
The maximum short circuit temperature rating of 200°C for a 5-second duration addresses the extreme conditions that can occur during electrical fault conditions. This specification ensures that the cable's insulation and other components can survive the intense heating that occurs during short circuit events, maintaining their integrity until protective devices can operate to clear the fault. This capability is crucial for maintaining system safety and minimising damage during fault conditions.
The permanent tensile force rating of 15 N/mm² provides guidance for cable installation and handling procedures. This specification indicates the maximum tension that can be applied to the cable during installation without causing damage to the internal components. Understanding this limitation is crucial for proper installation practices, particularly in applications where cables must be pulled through conduits or routed around obstacles.
Dimensional Specifications and Physical Characteristics
The cross-sectional area range of BS 6708 Type 11 cables, from 10 mm² up to 120 mm², provides flexibility in matching cable capacity to equipment power requirements. This range encompasses applications from smaller auxiliary equipment to the largest mining machinery, allowing system designers to optimise both electrical performance and installation cost. The availability of multiple cross-sectional areas also enables proper coordination of protective devices and ensures that cable capacity matches the requirements of connected equipment.
The minimum bending radius specifications represent critical installation parameters that directly affect cable longevity and performance. The distinction between fixed installation requirements (4 × cable diameter) and flexible operation requirements (5 × cable diameter) reflects the different mechanical stresses encountered in these applications. For fixed installations, where the cable will not be repeatedly flexed, the tighter bending radius allows for more compact installation configurations. For flexible applications, the larger bending radius ensures that repeated flexing does not cause fatigue damage to the internal cable components.
Cable weight considerations are important for both installation planning and structural support requirements. The example specification of 3.92 kg/m for a 3×16+16 mm² cable illustrates the substantial weight that must be supported in mining cable installations. This weight factor affects not only the mechanical design of cable support systems but also the practical aspects of cable handling and installation. Proper consideration of cable weight is essential for ensuring that support structures are adequate and that installation procedures account for the physical demands of handling heavy cables.
The copper weight specification provides important information for both material cost estimation and recycling considerations. Understanding the copper content of cables is valuable for lifecycle cost analysis and for planning cable disposal or recycling at the end of service life. The copper content also affects the cable's electrical characteristics, as higher copper content generally indicates lower electrical resistance and improved current-carrying capacity.
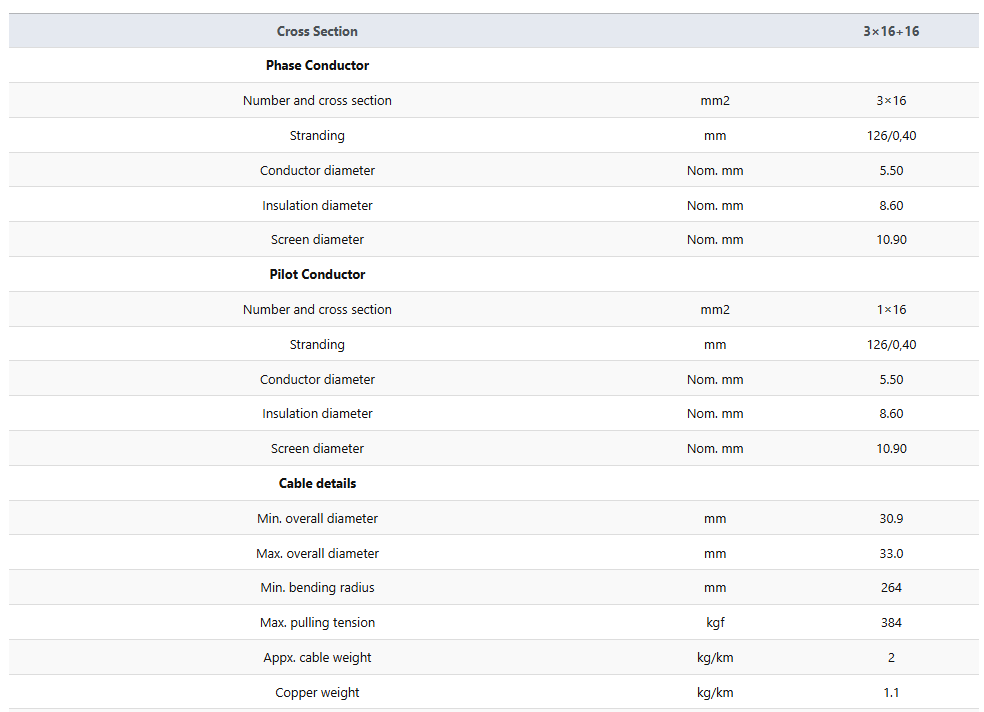
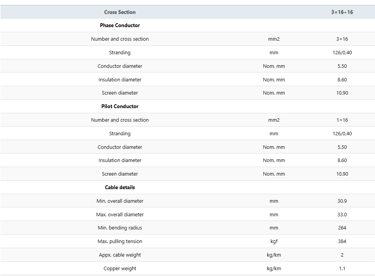
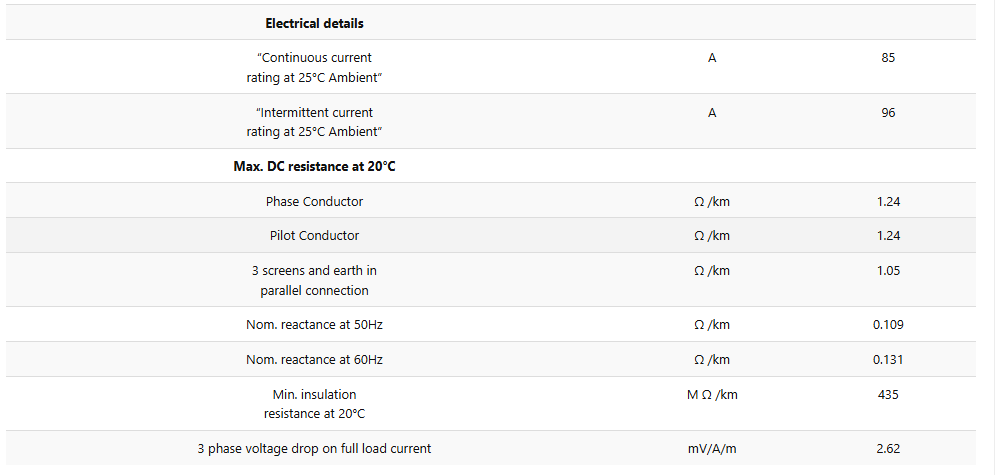
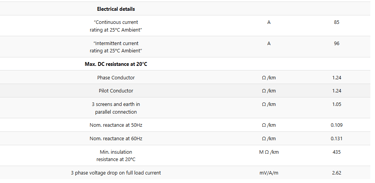
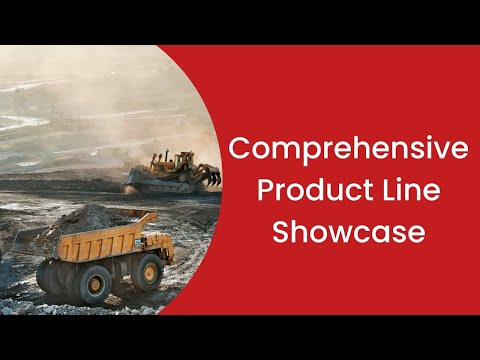
Frequently Asked Questions About BS 6708 Type 11 Cables
Temperature Performance and Environmental Limits
One of the most common inquiries about BS 6708 Type 11 cables concerns their temperature performance limits, particularly given the extreme environmental conditions encountered in mining operations. These cables are engineered to operate reliably across a temperature range from -40°C to 80°C, which encompasses virtually all conditions encountered in practical mining applications. This exceptional temperature range capability results from careful materials selection and construction techniques that ensure both electrical and mechanical performance remain stable across these extremes.
At the lower end of this temperature range, the cable materials must maintain their flexibility and mechanical properties even when subjected to the extreme cold that can occur in deep mine shafts or during winter surface operations. The EPR insulation and chloroprene sheath materials are specifically formulated to resist becoming brittle at low temperatures, ensuring that the cable can be handled and installed even in sub-zero conditions without risk of cracking or mechanical failure.
At elevated temperatures, the cable must continue to provide reliable electrical performance whilst maintaining its mechanical integrity. The 80°C ambient temperature rating, combined with the cable's current-carrying capacity specifications, ensures that the conductor temperature remains within safe limits even when operating at full load in warm environments. This temperature capability is particularly important in mining applications where cables may be exposed to heat from machinery, geothermal sources, or confined spaces with limited ventilation.
The temperature ratings also account for the thermal cycling that occurs in mining operations, where cables may experience rapid temperature changes as equipment operates intermittently or as environmental conditions change. The robust construction of Type 11 cables ensures that these thermal cycles do not cause degradation of the insulation system or mechanical properties over the cable's service life.
Chemical and Oil Resistance Properties
Mining operations involve exposure to numerous chemicals and oils that can severely damage conventional electrical cables, making chemical resistance a critical concern for cable selection. BS 6708 Type 11 cables incorporate a heavy-duty chloroprene outer sheath that provides exceptional resistance to the wide range of substances commonly encountered in mining environments. This includes hydraulic fluids used in heavy machinery, various lubricating oils, cutting fluids used in rock cutting operations, and numerous chemical solutions used in mineral processing activities.
The chloroprene material offers excellent resistance to petroleum-based products, which are ubiquitous in mining operations through hydraulic systems, diesel fuel, and various lubricants. This resistance prevents the gradual swelling, softening, or degradation that would occur with less suitable materials, ensuring that cable integrity is maintained even when exposed to oil spills or continuous contact with contaminated surfaces.
Beyond petroleum products, mining operations may involve exposure to various chemical solutions used in ore processing, cleaning agents, and specialty chemicals used in equipment maintenance. The chloroprene sheath provides broad chemical resistance that protects against most of these substances, though it is always advisable to consult specific compatibility data when unusual chemicals are involved in the application.
The chemical resistance properties of Type 11 cables extend beyond the outer sheath to include consideration of the other cable components. The EPR insulation provides good resistance to many chemicals that might penetrate the outer sheath, providing an additional layer of protection for the electrical components. The tinned copper conductors also offer enhanced corrosion resistance compared to bare copper, particularly when exposed to acidic or corrosive environments.
Installation Flexibility and Bending Requirements
The versatility of BS 6708 Type 11 cables in accommodating both fixed and flexible installations represents one of their key advantages in mining applications. This dual capability stems from the careful balance of mechanical properties achieved in the cable construction, allowing it to meet the requirements of diverse installation scenarios commonly encountered in mining operations.
For fixed installations, where cables are permanently routed through underground galleries, conduits, or surface installations, the minimum bending radius of four times the cable diameter allows for relatively compact installation configurations. This capability is particularly valuable in underground mining operations where space is at a premium and cable routes must often navigate around existing infrastructure, equipment, and geological features. The tighter bending radius for fixed installations enables more efficient use of available space whilst maintaining the mechanical integrity necessary for long-term reliability.
Flexible operations present significantly different challenges, requiring cables that can accommodate the continuous movement of mobile equipment whilst maintaining electrical integrity over thousands of flexing cycles. The increased minimum bending radius of five times the cable diameter for flexible applications reflects the additional mechanical considerations necessary to prevent fatigue failure of internal cable components. This specification ensures that cables can withstand the repeated flexing associated with mobile equipment operation, cable reeling systems, and other dynamic applications common in mining operations.
The distinction between these installation types is crucial for proper cable selection and installation planning. Understanding the mechanical requirements of each application type enables engineers to specify appropriate installation methods, support systems, and handling procedures that will maximise cable service life and reliability.
Safety Features in Explosive Environments
The design of BS 6708 Type 11 cables incorporates multiple safety features specifically engineered to address the risks associated with explosive atmospheres commonly encountered in mining operations. These safety considerations reflect decades of experience with mining electrical systems and the critical importance of preventing electrical ignition sources in potentially explosive environments.
The tinned copper and nylon braided screen over the phase cores serves multiple safety functions beyond its primary role in electromagnetic interference control. This screening system helps contain electromagnetic fields generated by current flow in the conductors, reducing the potential for electromagnetic interference with other electrical systems and minimising the risk of induced electrical effects that could create ignition sources.
The screening system also provides improved fault current handling capabilities, offering additional paths for fault currents and helping to ensure that protective devices operate quickly and effectively when faults occur. Rapid fault clearing is crucial in explosive environments, as sustained arcing or elevated temperatures from fault conditions could potentially ignite explosive gases or dust.
The robust earthing arrangements incorporated in Type 11 cables provide reliable paths for fault currents and help maintain electrical system integrity during abnormal conditions. The unscreened earth conductor ensures low impedance fault paths that enable protective devices to operate effectively, minimising the duration and intensity of fault conditions that could pose ignition risks.
The overall construction quality and materials selection of Type 11 cables contribute to their safety performance in explosive environments. The high-quality insulation system reduces the likelihood of insulation breakdown that could lead to arcing or tracking, whilst the robust outer sheath protects against mechanical damage that could compromise electrical integrity.
Comparison with Other BS 6708 Cable Types
Understanding how BS 6708 Type 11 cables compare with other types within the same standard helps clarify their specific role and advantages in mining applications. The BS 6708 standard encompasses multiple cable types, each designed for specific applications and operating conditions commonly encountered in mining and quarrying operations.
Type 11 cables are specifically optimised for applications involving shuttle cars, coal cutters, and at-face equipment, where the combination of flexibility, durability, and electrical performance is crucial. This specialisation is reflected in their construction details, including the specific insulation and sheathing materials, screening arrangements, and mechanical properties that make them ideal for these demanding applications.
Other types within the BS 6708 standard, such as Type 7 or Type 21 cables, may have different construction details that optimise them for different applications or operating conditions. Type 7 cables, for example, might be designed for different voltage levels or specific equipment types, whilst Type 21 cables could be optimised for different environmental conditions or installation requirements.
The selection of appropriate cable type within the BS 6708 family requires careful consideration of the specific application requirements, including electrical parameters, environmental conditions, mechanical demands, and installation constraints. Type 11 cables represent an optimal choice for applications requiring the specific combination of properties they provide, but other types may be more suitable for different applications within the same mining operation.
Understanding these distinctions enables engineers to select the most appropriate cable type for each application, optimising both performance and cost whilst ensuring compliance with relevant safety standards and regulations.
Conclusion
BS 6708 Type 11 mining cables represent a sophisticated engineering solution to the unique challenges presented by mining environments. Their carefully balanced design addresses the complex requirements of electrical power distribution in operations where safety, reliability, and durability are paramount concerns. From their robust conductor construction using tinned copper stranding to their heavy-duty chloroprene outer sheath, every aspect of these cables reflects decades of experience in mining electrical systems.
The comprehensive specifications of Type 11 cables demonstrate their capability to handle the demanding electrical and mechanical requirements of modern mining operations. Their voltage ratings provide adequate capacity for powering substantial mining equipment, whilst their temperature performance ensures reliable operation across the extreme environmental conditions encountered in both underground and surface mining applications. The chemical resistance properties of their construction materials protect against the various oils, hydraulic fluids, and chemical solutions that are commonplace in mining environments.
Perhaps most importantly, the safety features incorporated into BS 6708 Type 11 cables address the critical concerns associated with electrical systems in potentially explosive atmospheres. The screening systems, earthing arrangements, and overall construction quality work together to minimise ignition risks whilst providing the electrical performance necessary for effective mining operations.
The versatility of these cables in accommodating both fixed and flexible installations makes them valuable components in diverse mining applications, from permanent power distribution systems to the dynamic requirements of mobile equipment. This flexibility, combined with their robust construction and comprehensive safety features, positions BS 6708 Type 11 cables as essential components in safe and efficient mining operations.
Understanding the proper selection, installation, and application of these cables is crucial for anyone involved in mining electrical systems, from design engineers to maintenance technicians. Their role in maintaining safe and reliable electrical power distribution in some of the world's most challenging industrial environments makes them indispensable components of modern mining operations. As mining operations continue to evolve and face new challenges, the proven performance and reliability of BS 6708 Type 11 cables ensure their continued importance in supporting safe and efficient resource extraction activities.