Understanding BS 6708 TYPE 7 Mining Cable
Comprehensive guide to BS 6708 TYPE 7 mining cables covering construction, electrical parameters, applications in coalcutters and mining equipment, with expert FAQ answers for safe underground operations.
5/27/202516 min read
Understanding BS 6708 TYPE 7 Mining Cable
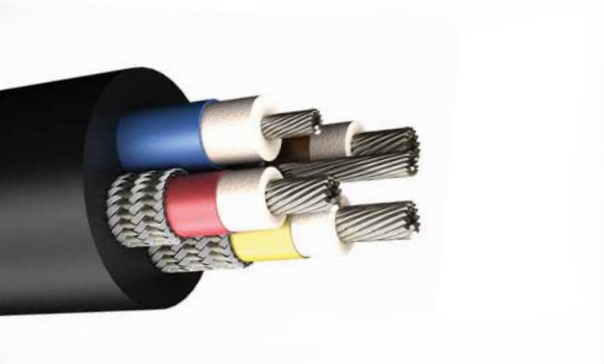
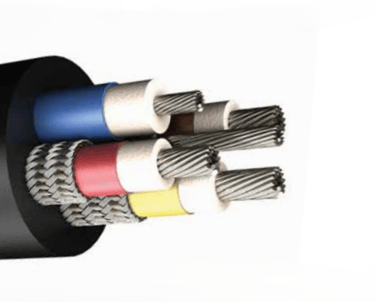
Introduction
In the demanding world of underground mining operations, electrical safety and reliability aren't just important—they're matters of life and death. The BS 6708 TYPE 7 mining cable represents a pinnacle of engineering design specifically created to meet the extraordinary challenges of powering heavy machinery in some of the most hazardous environments on Earth. These specialized power supply cables serve as the electrical lifelines for coalcutters, crushers, drilling equipment, and other critical mining machinery operating in explosive atmospheres where traditional cables would fail catastrophically.
Understanding the intricacies of BS 6708 TYPE 7 cables becomes essential when we consider that mining operations often occur in environments where explosive gases and coal dust create constant threats of ignition. The consequences of electrical failure in such settings extend far beyond simple equipment downtime—they can result in explosions, fires, and loss of life. This is why these cables incorporate multiple layers of protection, from their unique construction methods to their specialized materials, all designed to maintain electrical integrity while withstanding the mechanical abuse that mining environments inevitably deliver.
The British Standard 6708 specification emerged from decades of mining industry experience and represents a collaborative effort between electrical engineers, mining safety experts, and cable manufacturers to create a product that could reliably serve in the harshest industrial applications. Unlike standard industrial cables, BS 6708 TYPE 7 cables must simultaneously address electrical performance, mechanical durability, chemical resistance, and explosion prevention—a combination of requirements that demands innovative engineering solutions.
Application Scenarios and Operating Environments
The primary applications for BS 6708 TYPE 7 cables center around powering the heavy machinery that forms the backbone of modern mining operations. Coalcutters, which are massive machines designed to shear coal from mine faces, represent perhaps the most demanding application for these cables. These machines operate in continuous motion, requiring cables that can flex thousands of times per day while maintaining electrical integrity. The cutting action generates enormous mechanical stresses on all connected equipment, including the power cables that must follow the machine's movements through confined underground spaces.
Crushing equipment presents another critical application scenario where these cables prove indispensable. Rock crushers and ore processing machinery operate under extreme mechanical loads, generating vibrations that would quickly destroy conventional electrical cables. The BS 6708 TYPE 7 design specifically addresses these challenges through its flexible conductor construction and robust outer sheath, allowing it to absorb and dissipate mechanical energy without compromising electrical performance.
Drilling operations create unique demands on electrical infrastructure, as drilling equipment must often operate in areas where water infiltration, abrasive materials, and temperature variations create hostile conditions for electrical components. The waterproof characteristics of the chloroprene outer sheath, combined with the cable's resistance to chemical attack from drilling fluids and mineral salts, make it particularly suitable for these applications.
The operating environments where these cables serve extend from deep underground coal mines to surface mining operations, each presenting distinct challenges. Underground environments are characterized by high humidity, temperature variations, exposure to groundwater, and the constant presence of explosive gases such as methane. The accumulation of coal dust further compounds these hazards, as fine particulate matter can create explosive atmospheres even in well-ventilated areas. Surface mining operations, while avoiding some underground hazards, expose cables to weather extremes, ultraviolet radiation, and mechanical abuse from heavy equipment traffic.
One particularly challenging aspect of mining cable applications involves the mobile nature of much mining equipment. Unlike stationary installations where cables can be permanently routed and protected, mining machinery often requires trailing cables that must flex, twist, and bend as equipment moves through mine tunnels or across mining sites. This dynamic loading creates fatigue stresses that conventional cables cannot withstand over extended periods. The BS 6708 TYPE 7 design addresses this challenge through its fine-stranded conductor construction and specialized bedding compounds that distribute mechanical stresses across the cable structure.
The explosive atmosphere classification system used in mining operations requires cables that meet strict standards for preventing ignition sources. Even minor electrical faults that might be acceptable in other industrial applications become potentially catastrophic in mining environments. This reality drives the comprehensive screening and grounding approaches used in BS 6708 TYPE 7 cables, where multiple layers of protection work together to prevent any possibility of electrical discharge that could trigger an explosion.
Construction and Design Features
The construction of BS 6708 TYPE 7 cables represents a masterpiece of electrical engineering, where every component serves multiple purposes in creating a product capable of surviving mining environments. Understanding this construction requires examining each layer and component to appreciate how they work together to provide both electrical performance and mechanical protection.
Core Structure and Conductor Design
The heart of any electrical cable lies in its conductor design, and BS 6708 TYPE 7 cables employ electrolytic, tinned, and stranded copper conductors that meet the demanding requirements of IEC 60228 Class 5 specifications. This classification indicates extremely fine stranding, with individual wire diameters as small as 0.40mm in smaller cross-sections, increasing to 0.50mm in larger sizes. This fine stranding serves multiple critical purposes in mining applications.
The flexibility achieved through fine stranding allows the cable to bend repeatedly without conductor fatigue, essential for equipment that operates in continuous motion. Each individual wire in the strand can move independently during flexing, distributing mechanical stress across the entire conductor cross-section rather than concentrating it at specific points where failure might occur. The tinning process applied to each individual wire provides protection against corrosion from moisture and chemical exposure common in mining environments.
The three-phase conductor arrangement follows a carefully engineered geometry where all conductors maintain contact with the central bare earth conductor. This design creates multiple current paths for fault currents, enhancing safety by ensuring rapid operation of protective devices in the event of insulation failure. The geometric arrangement also provides inherent mechanical support, as the conductors cannot separate from each other during cable flexing.
Insulation System and Screening Technology
The insulation system employs Ethylene Propylene Rubber (EPR), chosen specifically for its superior performance characteristics in demanding environments. EPR provides excellent electrical properties across a wide temperature range while maintaining flexibility even in cold conditions commonly encountered in deep mines. Unlike thermoplastic insulations that can become brittle at low temperatures or soft at high temperatures, EPR maintains consistent properties across the operating temperature range.
The decision to leave the earth conductor uninsulated reflects sophisticated engineering thinking about safety and performance. By allowing the earth conductor to remain in direct contact with the screening systems and other conductors, any insulation failure immediately creates a fault current path that will trip protective devices. This approach prioritizes rapid fault detection over attempting to prevent all possible fault conditions, recognizing that in mining environments, rapid response to electrical faults is more important than preventing them entirely.
The screening system applied to the phase conductors represents another layer of engineering sophistication. Tinned copper wire braided with nylon creates a screen that provides both electrical performance and mechanical protection. The electrical function includes containing electromagnetic emissions that could interfere with sensitive mining control systems while providing a low-impedance path for fault currents. The mechanical function involves distributing forces across the conductor surface during cable flexing and providing abrasion resistance.
The absence of screening on the pilot conductor reflects the different functional requirements of this conductor. Used primarily for control signals and monitoring functions, the pilot conductor operates at much lower currents than the main power conductors. Eliminating the screen reduces cable diameter and weight while maintaining the flexibility needed for dynamic applications.
Mechanical Protection Systems
The bedding compound used in BS 6708 TYPE 7 cables serves as a critical interface between the electrical components and the mechanical protection system. This rubber-based compound fills the spaces between conductors and screens, preventing water ingress while cushioning the electrical components against mechanical shock and vibration. The compound must maintain its properties across the temperature range encountered in mining operations while remaining chemically inert to prevent degradation of other cable components.
The outer sheath constructed from heavy-duty chloroprene represents the cable's primary defense against environmental hazards. Chloroprene, a synthetic rubber compound, provides exceptional resistance to oils, chemicals, and abrasion while maintaining flexibility across a wide temperature range. The "heavy-duty" designation indicates increased wall thickness compared to standard applications, providing additional mechanical protection against the severe abuse common in mining operations.
The textile separators used for core identification serve dual purposes in the cable construction. Their primary function involves color-coding conductors for proper installation and maintenance, but they also provide mechanical separation that prevents conductor-to-conductor contact during manufacturing and installation. These separators must resist moisture absorption while maintaining their identification properties throughout the cable's service life.
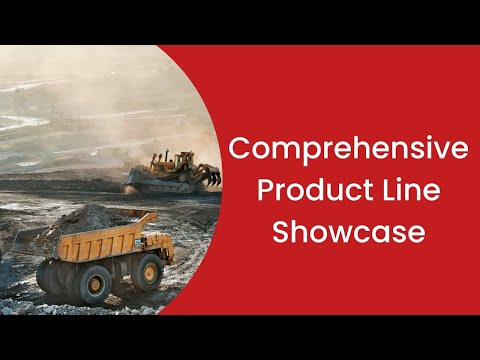
Electrical Parameters and Performance Characteristics
The electrical performance of BS 6708 TYPE 7 cables must meet stringent requirements that exceed those of most industrial applications. Understanding these parameters requires examining not just the nominal ratings but also how they relate to practical mining applications and safety requirements.
Voltage Ratings and Insulation Performance
The rated voltage of 640/1100V reflects the cable's design for medium-voltage mining distribution systems. The dual rating indicates the cable's capability to operate at 640V line-to-line voltage in three-phase systems or 1100V line-to-neutral in single-phase applications. This voltage level represents a compromise between safety considerations that favor lower voltages and efficiency considerations that favor higher voltages for reduced current and power losses.
The test voltage specification of 3kV provides substantial margin above the operating voltage, ensuring insulation integrity even under fault conditions. This test voltage must be sustained for specified durations without breakdown, demonstrating that the insulation system can withstand transient overvoltages commonly encountered in mining electrical systems. These transients often result from switching operations, lightning strikes, or fault conditions in other parts of the mining electrical system.
The minimum insulation resistance values, ranging from 435 to 250 MΩ·km depending on conductor size, provide quantitative measures of insulation quality. Higher values indicate better insulation integrity, with the variation reflecting the inverse relationship between conductor surface area and insulation resistance. These values are measured at 20°C and provide baseline reference points for acceptance testing and ongoing condition monitoring.
Current Carrying Capacity and Thermal Performance
The continuous current ratings, ranging from 85A for the smallest 3×16mm² configuration to 320A for the largest 3×150mm² size, reflect careful thermal analysis of heat generation and dissipation. These ratings assume an ambient temperature of 25°C, which is typical for many mining applications but may require derating for higher temperature environments such as deep mines where geothermal heating becomes significant.
The intermittent current ratings, reaching up to 385A for the largest conductor size, recognize that many mining applications involve cyclical loading where equipment operates at high power levels for short periods followed by reduced power or idle periods. This thermal cycling allows the cable to handle higher currents temporarily while the conductor temperature remains within acceptable limits.
Understanding the relationship between continuous and intermittent ratings becomes crucial for proper cable selection. Equipment that operates in short-duration, high-power cycles may be adequately served by smaller conductor sizes than would be required for continuous operation at the same power level. However, this approach requires careful analysis of the actual duty cycle and thermal time constants to ensure safe operation.
The copper content specifications, ranging from 1,070 kg/km to 6,500 kg/km, directly relate to both electrical performance and cable cost. Higher copper content provides lower resistance and better current carrying capacity but increases both material cost and cable weight. In mining applications where cables must often be handled manually during installation and maintenance, the weight considerations become particularly important.
Resistance and Voltage Drop Characteristics
The DC resistance values for phase conductors, ranging from 1.24 Ω/km for 16mm² conductors to 0.132 Ω/km for 150mm² conductors, provide the foundation for calculating power losses and voltage drops in mining distribution systems. These values measured at 20°C must be adjusted for actual operating temperatures using standard temperature coefficients for copper conductors.
The pilot conductor resistance values follow the same pattern but remain higher due to the smaller cross-sectional areas used for these control circuits. The consistency of pilot conductor sizing across multiple cable configurations reflects standardization efforts to simplify control system design and maintenance procedures.
The parallel resistance of the three screens and earth conductor combination, ranging from 0.66 Ω/km to 0.176 Ω/km, provides important information for fault current calculations and protective device coordination. This parallel path for fault currents ensures that ground faults will generate sufficient current to operate protective devices reliably.
The voltage drop calculations for three-phase full load current, expressed in mV/A·m, allow system designers to predict voltage regulation performance in mining distribution systems. These values incorporate both the resistive and reactive components of voltage drop, providing accurate predictions for system performance analysis.
The reactance values at both 50Hz and 60Hz frequencies reflect the global nature of mining operations where different power system frequencies are encountered. The relatively low reactance values compared to overhead transmission lines reflect the cable's compact geometry and magnetic coupling between conductors.
Mining-Specific Challenges and Solutions
Mining operations present unique electrical challenges that conventional industrial cables cannot address adequately. Understanding these challenges and how BS 6708 TYPE 7 cables address them provides insight into the sophisticated engineering required for mining applications.
Explosive Atmosphere Protection
The prevention of ignition sources in explosive atmospheres represents perhaps the most critical challenge in mining cable applications. Methane gas, coal dust, and other combustible materials create environments where even minor electrical faults can trigger catastrophic explosions. The comprehensive screening system used in BS 6708 TYPE 7 cables addresses this challenge through multiple mechanisms.
The individual screens on each phase conductor contain any electrical discharge within the conductor assembly, preventing external arcing that could ignite explosive atmospheres. The screens also provide defined current paths for fault conditions, ensuring that protective devices operate quickly to interrupt fault currents before dangerous conditions develop.
The bare earth conductor in constant contact with all other cable components creates multiple ground fault current paths, enhancing the reliability of protective device operation. This redundancy is essential in mining applications where a single point of failure in the grounding system could compromise safety for all personnel in the affected area.
Mechanical Durability and Flexibility Requirements
The mechanical demands placed on mining cables exceed those encountered in most other industrial applications. Equipment mobility, confined spaces, and the abrasive nature of mining environments create stress conditions that would quickly destroy conventional cables. The fine stranding used in BS 6708 TYPE 7 conductors directly addresses these challenges by distributing mechanical stress across numerous individual wire elements.
The rubber bedding compound provides cushioning that absorbs mechanical shock and vibration while preventing the migration of forces between cable components. This isolation prevents concentrated stress points that could lead to premature failure of individual components even when the overall cable structure remains intact.
The heavy-duty chloroprene outer sheath provides the primary mechanical protection against abrasion, impact, and crushing forces. The specific compound formulation balances flexibility requirements with mechanical strength, creating a product that can survive the harsh handling common in mining operations while maintaining the flexibility needed for dynamic applications.
Environmental Resistance and Chemical Compatibility
Mining environments expose cables to a wide range of chemical hazards including acids from groundwater, alkaline compounds from concrete and rock dust, petroleum products from hydraulic systems, and various cleaning chemicals used in mining operations. The chloroprene outer sheath provides broad-spectrum chemical resistance that protects the internal cable components from degradation.
Water resistance becomes particularly critical in mining applications where cables often operate in wet or humid conditions. The combination of EPR insulation and chloroprene sheath provides excellent moisture resistance while the bedding compound prevents water migration along the cable length even if the outer sheath is damaged.
Temperature variations in mining environments can be extreme, ranging from freezing conditions in some surface operations to elevated temperatures in deep mines. The material selection for BS 6708 TYPE 7 cables ensures that all components maintain their essential properties across this temperature range, preventing brittleness in cold conditions and excessive softening in hot conditions.
Frequently Asked Questions (FAQ)
Q1: Why is the earth conductor left uninsulated in BS 6708 TYPE 7 cables?
The decision to leave the earth conductor uninsulated represents a carefully considered safety design that prioritizes rapid fault detection over fault prevention. In mining environments where explosive atmospheres are common, the most important safety consideration is ensuring that any electrical fault is quickly detected and interrupted before it can create an ignition source.
When the earth conductor remains uninsulated and in contact with the screening systems of the phase conductors, any insulation failure immediately creates a ground fault current that will trip protective devices. This approach ensures that faults are detected within milliseconds rather than allowing them to develop into more dangerous conditions such as arcing faults that could ignite explosive atmospheres.
The uninsulated earth conductor also enhances grounding performance by providing a low-impedance return path for fault currents. This improves the reliability of protective device operation and reduces the risk of dangerous voltages appearing on equipment frames during fault conditions. Additionally, the space savings achieved by eliminating earth conductor insulation allows for larger phase conductors within the same overall cable diameter, improving the cable's current carrying capacity.
Q2: Can BS 6708 TYPE 7 cables be used in wet or corrosive environments?
Yes, these cables are specifically designed to operate reliably in wet and corrosive environments commonly encountered in mining operations. The chloroprene outer sheath provides excellent resistance to water, oils, acids, and alkaline compounds typically found in mining environments. This synthetic rubber compound maintains its protective properties even when exposed to groundwater, hydraulic fluids, and cleaning chemicals used in mining operations.
The EPR insulation used on the phase and pilot conductors also provides superior moisture resistance compared to many other insulation materials. Even if moisture penetrates the outer sheath, the EPR insulation continues to provide electrical isolation and prevents the formation of conductive paths that could compromise safety.
The rubber-based bedding compound serves as an additional barrier against moisture ingress while preventing water migration along the cable length. This multi-layer protection approach ensures that even if one protective barrier is compromised, the remaining barriers continue to protect the electrical integrity of the cable.
For applications in particularly corrosive environments, proper cable support and protection methods should be employed to minimize direct exposure to aggressive chemicals. However, the inherent chemical resistance of the cable materials provides substantial protection even in demanding conditions.
Q3: What is the role of the pilot core, and why isn't it screened?
The pilot core serves multiple functions in mining cable applications, primarily related to control, monitoring, and safety systems rather than power transmission. Common applications include equipment status monitoring, emergency stop circuits, communication between equipment and control centers, and interlock systems that coordinate multiple pieces of equipment for safe operation.
The decision not to screen the pilot core reflects several engineering considerations. Since the pilot core carries much lower currents than the power conductors, it generates minimal electromagnetic interference and doesn't require the same level of electromagnetic containment. Eliminating the screen reduces cable diameter, weight, and cost while maintaining the flexibility needed for dynamic mining applications.
The pilot core's unscreened design also provides manufacturing advantages by simplifying cable construction and reducing the potential for screen-related defects. In mining applications where cable reliability is paramount, reducing complexity often improves overall reliability by eliminating potential failure modes.
The pilot core does benefit from the overall electromagnetic shielding provided by the screens on the phase conductors, which contain most electromagnetic emissions from the cable. This provides adequate protection for the control signals carried by the pilot core while maintaining the operational advantages of the unscreened design.
Q4: How do I choose the right cross-section for my mining application?
Selecting the appropriate conductor cross-section requires careful analysis of multiple factors specific to mining applications. The primary considerations include the full-load current requirements of the connected equipment, the installation length and cable routing, acceptable voltage drop limits, environmental factors such as ambient temperature and installation conditions, and future expansion requirements.
For high-power equipment such as large coalcutters or crushers, the continuous current ratings provide the starting point for cable selection. Equipment drawing 200-300 amperes would typically require the 3×120mm² or 3×150mm² configurations to provide adequate current carrying capacity with appropriate safety margins.
Voltage drop calculations become particularly important in mining applications where cable runs can be extensive and voltage regulation affects equipment performance. The voltage drop figures provided in the cable specifications allow calculation of total system voltage drop, which should typically not exceed 5% for motor loads to ensure proper starting and running performance.
Installation conditions significantly affect cable selection in mining environments. Cables installed in conduits or cable trays have reduced heat dissipation compared to free-air installations, requiring derating of current carrying capacity. Similarly, elevated ambient temperatures in deep mines may require larger conductor sizes to maintain safe operating temperatures.
The mechanical demands of the specific application also influence selection. Equipment that operates continuously in dynamic conditions may benefit from larger conductor sizes that provide additional mechanical strength, even if the electrical requirements could be met with smaller sizes.
Q5: How flexible is this cable for reel and trailing applications?
BS 6708 TYPE 7 cables are specifically engineered for the flexibility requirements of mobile mining equipment, making them well-suited for reel and trailing applications. The fine-stranded conductor construction, with individual wire diameters as small as 0.40mm, provides exceptional flexibility that allows the cable to flex repeatedly without conductor fatigue.
The minimum bending radius specifications, ranging from 309mm for the smallest configuration to 627mm for the largest, indicate the cable's ability to form tight bends without damage. These values represent the minimum radius for installation bending; larger radii should be used for dynamic applications where the cable flexes repeatedly during operation.
The rubber bedding compound plays a crucial role in flexibility by cushioning the internal components during bending and preventing the concentration of stress at specific points. This compound remains flexible across the temperature range encountered in mining operations, ensuring consistent performance in both cold surface conditions and warm underground environments.
For reel applications, the cable's construction allows thousands of winding and unwinding cycles without degradation. The conductor stranding and insulation materials are specifically chosen to withstand the mechanical stress of repeated coiling, which can be particularly severe in automatic cable reel systems where rapid winding and unwinding occurs.
The maximum pulling tension specifications, reaching up to 2,000 kgf for larger cable sizes, provide guidance for installation procedures and reel system design. These values ensure that the cable can withstand the mechanical forces encountered during installation and operation without damage to internal components.
When designing reel systems for BS 6708 TYPE 7 cables, consideration should be given to reel diameter, winding speed, and environmental protection to maximize cable service life. Proper reel design that maintains appropriate bending radii and provides protection from environmental hazards will ensure reliable performance throughout the cable's design life.
Summary and Conclusion
BS 6708 TYPE 7 mining cables represent a pinnacle of specialized electrical engineering, combining sophisticated design elements to create products capable of reliable operation in some of the world's most challenging industrial environments. The comprehensive approach to cable construction, from the fine-stranded conductor design through the heavy-duty protective systems, demonstrates the level of engineering sophistication required for critical mining applications.
The electrical performance characteristics of these cables provide the reliability and safety margins essential for mining operations where electrical failures can have catastrophic consequences. The careful balance between current carrying capacity, voltage regulation, and fault protection ensures that mining equipment receives the electrical power needed for efficient operation while maintaining the safety standards required in explosive atmospheres.
The mechanical design features, including the flexible conductor construction, rubber bedding compounds, and chloroprene outer sheath, address the unique challenges of mobile mining equipment operating in abrasive and mechanically demanding environments. The cable's ability to withstand repeated flexing, impact, and abrasion while maintaining electrical integrity makes it suitable for the most demanding mining applications.
Understanding the specifications and capabilities of BS 6708 TYPE 7 cables enables mining professionals to make informed decisions about electrical system design and equipment selection. Proper application of these cables, considering both their capabilities and limitations, ensures safe and reliable operation of critical mining equipment while maximizing operational efficiency and minimizing maintenance requirements.
The investment in specialized mining cables such as BS 6708 TYPE 7 represents a commitment to operational safety and reliability that pays dividends through reduced downtime, improved equipment performance, and enhanced personnel safety. In mining environments where the cost of failure extends far beyond simple equipment replacement, the engineering sophistication embodied in these cables provides essential protection for both equipment and personnel.
As mining operations continue to evolve toward greater mechanization and deeper excavations, the demands on electrical infrastructure will only increase. BS 6708 TYPE 7 cables provide a proven foundation for these evolving requirements, combining established reliability with the performance characteristics needed for next-generation mining equipment. Understanding and properly applying these cables ensures that electrical systems can support the demanding requirements of modern mining operations while maintaining the safety standards essential for protecting personnel and equipment in hazardous environments.