Understanding the (N)TSCGEWÖU-(SB) Mining Cable
When you think about the massive machinery operating in Australia's mining industry—from the draglines working the coal seams of Queensland to the underground loaders in Western Australia's gold mines—it's easy to focus on the impressive scale of the equipment itself. However, the unsung heroes of these operations are often the cables that deliver power to these machines, working tirelessly in some of the harshest environments on Earth. Mining cables represent a critical intersection of electrical engineering and materials science, where reliability isn't just about performance—it's about safety, productivity, and keeping Australia's resource extraction industry running smoothly. Among the various cable solutions available, the (N)TSCGEWÖU-(SB) mining cable stands out as a particularly robust example of engineering designed specifically for the demanding conditions found in both surface and underground mining operations.
5/23/20259 min read
Understanding the (N)TSCGEWÖU-(SB) Mining Cable
When you think about the massive machinery operating in Australia's mining industry—from the draglines working the coal seams of Queensland to the underground loaders in Western Australia's gold mines—it's easy to focus on the impressive scale of the equipment itself. However, the unsung heroes of these operations are often the cables that deliver power to these machines, working tirelessly in some of the harshest environments on Earth.
Mining cables represent a critical intersection of electrical engineering and materials science, where reliability isn't just about performance—it's about safety, productivity, and keeping Australia's resource extraction industry running smoothly. Among the various cable solutions available, the (N)TSCGEWÖU-(SB) mining cable stands out as a particularly robust example of engineering designed specifically for the demanding conditions found in both surface and underground mining operations.
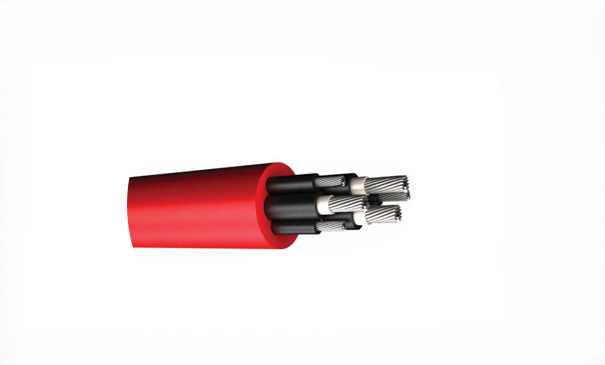
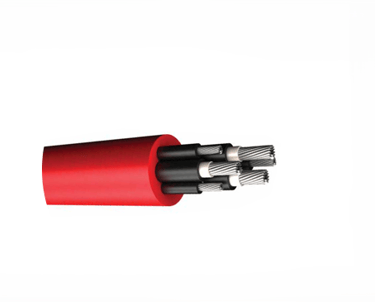
Where These Cables Earn Their Keep
Surface and Underground Mining Applications
The (N)TSCGEWÖU-(SB) cable serves primarily as what mining engineers call a "trailing cable"—essentially a flexible power cord that follows mobile equipment as it moves throughout a mining site. Picture a massive electric shovel working an open-pit copper mine: as the shovel moves along the bench, repositioning itself to access different areas of the ore body, it needs a power source that can move with it whilst maintaining a reliable electrical connection.
In open-pit operations, these cables must withstand being dragged across rough terrain, exposed to the elements, and subjected to the mechanical stress of constant movement. Underground applications present even greater challenges, where the cable might be routed through narrow tunnels, around sharp corners, and through areas where water seepage, chemical exposure, and limited ventilation create an environment that would quickly destroy conventional electrical cables.
The versatility of this cable design extends beyond traditional mining equipment to include drilling rigs, conveyor systems, and mobile crushing units—essentially any piece of heavy machinery that requires both mobility and a reliable high-voltage power supply.
Conquering Harsh Environmental Conditions
To understand why specialised mining cables like the (N)TSCGEWÖU-(SB) are necessary, consider the environmental challenges they face daily. In underground coal mines, cables encounter not only physical abrasion from being dragged across rough surfaces but also exposure to coal dust, methane, and varying levels of moisture. Open-pit operations expose cables to temperature extremes, UV radiation, ozone, and the chemical residues from blasting operations.
The cable's design specifically addresses these challenges through its material selection and construction methodology. The heavy-duty elastomer outer sheath provides resistance to oils, acids, and other chemicals commonly found in mining environments, whilst the flexible conductor design ensures the cable can withstand the repeated bending and flexing that occurs during normal operation.
Beyond Mining: Heavy-duty Industrial Applications
Whilst mining represents the primary application for these cables, their robust construction makes them suitable for other demanding industrial environments. Tunnelling operations, such as those involved in major infrastructure projects like Sydney's WestConnex or Melbourne's Metro Tunnel, require cables that can perform reliably in confined spaces with limited access for maintenance or replacement.
Construction sites operating heavy electrical equipment, marine applications involving ship-to-shore power connections, and industrial facilities with mobile equipment all benefit from the durability and flexibility that characterise this cable design.
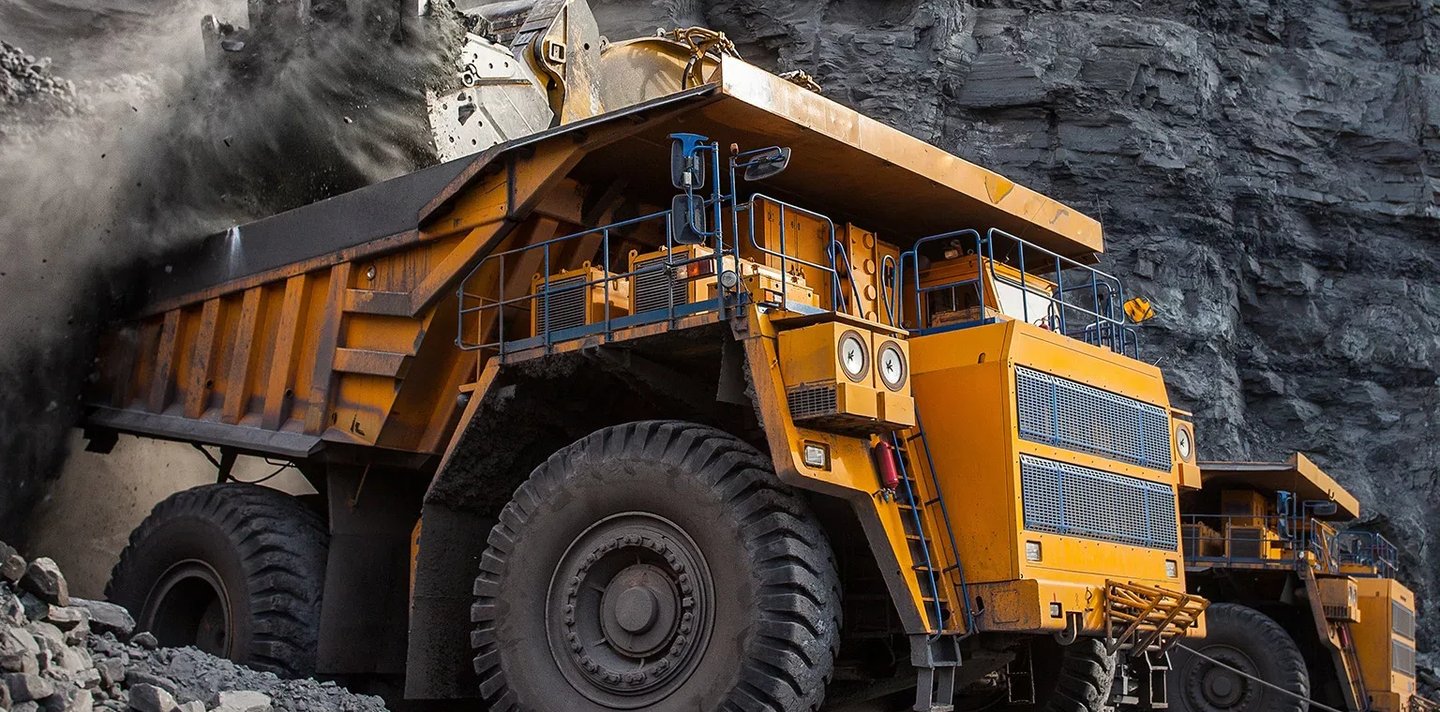
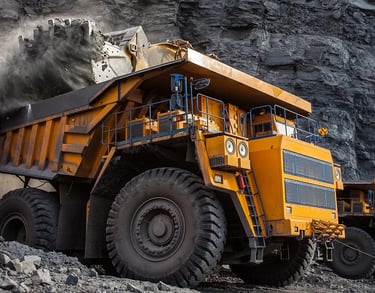
Engineering Excellence: Cable Structure and Design Philosophy
Understanding the Construction Approach
The (N)TSCGEWÖU-(SB) cable employs what electrical engineers describe as a "laid-up" construction, where multiple components are twisted together to form a cohesive whole that's stronger and more flexible than its individual parts. Think of it like a rope: individual fibres are relatively weak, but when twisted together in the proper configuration, they create a structure capable of supporting tremendous loads.
The conductors themselves are manufactured from electrolytic copper—the highest purity grade available—and are tinned to prevent corrosion. The "Class 5" designation indicates these conductors are made from very fine strands of wire, providing maximum flexibility whilst maintaining excellent electrical conductivity. This flexibility is crucial because the cable must bend and flex thousands of times during its operational life without developing fatigue failures.
The insulation system represents perhaps the most sophisticated aspect of the cable's design. Phase cores (the conductors carrying the main electrical load) are insulated with a specialised compound designated as 3G13, which meets the stringent requirements of DIN VDE 0207. This insulation must not only provide electrical isolation but also resist the mechanical stresses, temperature variations, and chemical exposures typical of mining environments.
One particularly interesting design feature is the use of semiconductive layers both over the phase conductors and around the earth cores. These layers help manage the electrical field distribution within the cable, reducing the likelihood of electrical breakdown and extending the cable's operational life. It's somewhat analogous to how the aerodynamic design of an aircraft manages airflow to prevent turbulence—the semiconductive layers manage electrical field distribution to prevent electrical stress concentrations.
The earth cores (used for safety grounding) are intentionally left uninsulated and are positioned interstitially—that is, in the spaces between the main phase conductors. This arrangement provides several advantages: it creates a more compact cable design, ensures that the earth conductors are in intimate contact with the outer sheath (improving grounding effectiveness), and provides multiple paths for fault current in the event of insulation failure.
Electrical Performance Characteristics
The cable is rated for 6/10 kV operation, which in Australian electrical terminology means it can safely operate at 6 kV line-to-earth voltage and 10 kV line-to-line voltage. This voltage level is common in mining applications because it provides a good compromise between power transmission capability and safety considerations.
The test voltages—17 kV AC and 42.5 kV DC—demonstrate the substantial safety margin built into the cable design. These test levels are approximately three to four times the operating voltage, ensuring that the cable can withstand voltage surges, switching transients, and other electrical stresses that occur in real-world mining operations.
Compliance with VDE 0250-813 indicates that the cable meets stringent European standards for mining applications, which are recognised internationally for their rigorous testing requirements and comprehensive coverage of operational scenarios.
Technical Specifications: Understanding the Numbers
When examining the technical specifications for different cable configurations, several key parameters tell the story of each cable's capabilities and intended applications.
The smallest configuration, 3x35+3x25/3, features three 35 mm² phase conductors and three 25 mm² earth conductors. With an overall diameter ranging from 46.0 to 50.0 mm and weighing approximately 3,800 kg per kilometre, this represents the most compact option in the range. The copper content of 1,344 kg per kilometre indicates the substantial amount of conductive material required to handle the electrical loads whilst maintaining flexibility.
Moving up the scale, the 3x70+3x35/3 configuration doubles the phase conductor size to 70 mm², with correspondingly larger earth conductors. The diameter increases to 62.3-66.3 mm, and the weight jumps to 5,800 kg per kilometre with 2,352 kg of copper content. This configuration would typically be selected for higher-power applications or longer cable runs where voltage drop becomes a significant consideration.
The largest standard configuration, 3x95+3x50/3, represents the heavy-duty end of the spectrum. With phase conductors of 95 mm² and the largest overall diameter of 64.9-68.9 mm, this cable can handle substantial electrical loads. The total weight of 7,200 kg per kilometre, including 3,216 kg of copper, reflects the substantial engineering required to deliver high power in demanding environments.
These specifications reveal an important engineering principle: as power requirements increase, the cable must grow not just in conductor size but in overall robustness to handle the increased mechanical and thermal stresses that accompany higher electrical loads.
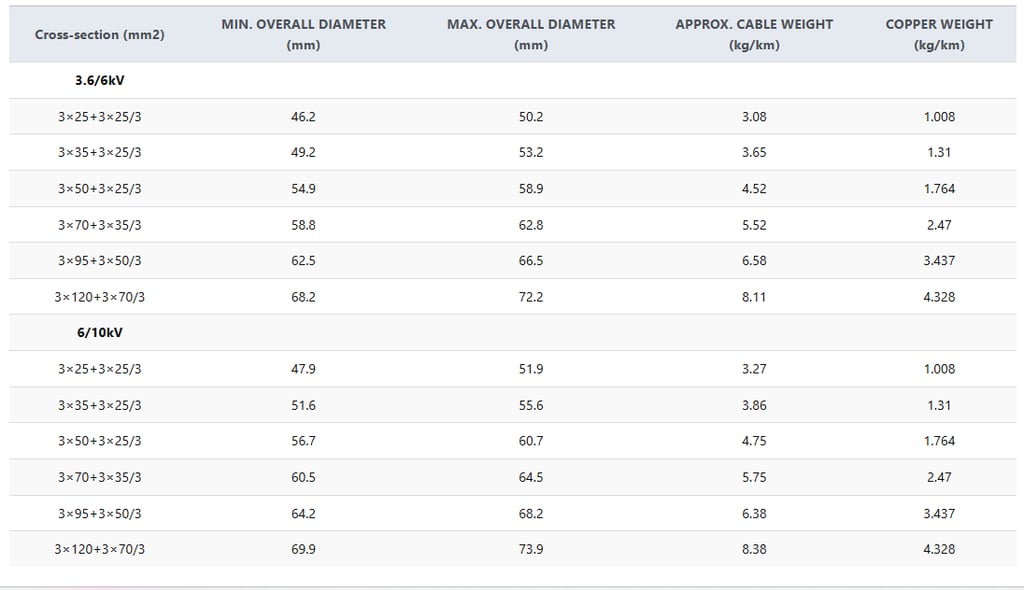
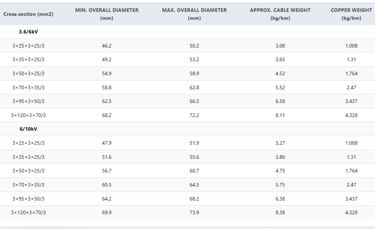
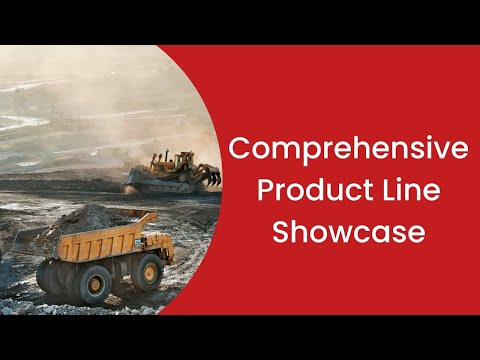
Addressing Common Concerns and Misconceptions
Flexibility and Durability Under Stress
One of the most frequent concerns expressed by mining operators relates to whether any cable can withstand the mechanical abuse typical of mining operations. The repeated dragging, bending, and flexing that occurs as equipment moves throughout a mining site would quickly destroy conventional electrical cables.
The (N)TSCGEWÖU-(SB) cable addresses this concern through several design features working in concert. The Class 5 conductor construction uses hundreds of fine wire strands rather than a few large ones, distributing mechanical stress across many individual elements. The elastomer outer sheath provides both protection and flexibility, allowing the cable to bend around obstacles without developing stress concentrations that could lead to failure.
The interstitial placement of earth conductors also contributes to mechanical robustness by eliminating large voids within the cable structure that could allow the cable to deform under stress. This design approach creates a more homogeneous structure that responds predictably to mechanical loading.
Chemical and Environmental Resistance
Mining environments expose cables to a remarkable variety of chemical challenges. Underground coal mines may expose cables to acids formed by the reaction of water with sulphur-bearing minerals. Metalliferous mines might involve exposure to processing chemicals, whilst surface operations can expose cables to fuel spills, hydraulic fluids, and cleaning solvents.
The 5GM5 elastomer sheath material specified for this cable has been specifically formulated to resist degradation from oils, acids, and other chemicals commonly encountered in mining operations. This isn't simply a matter of selecting a 'tough' material—the elastomer must maintain its flexibility and electrical properties even after prolonged exposure to these challenging substances.
Flame resistance represents another critical consideration, particularly in underground operations where fire poses an extreme hazard due to limited escape routes and ventilation challenges. The cable's materials and construction are designed to resist ignition and limit flame propagation, contributing to overall mine safety.
Ground Fault Protection and Safety
The uninsulated earth conductors sometimes raise questions about safety, particularly among those more familiar with conventional electrical installations. However, this design choice reflects the specific requirements of mining applications, where reliable grounding is absolutely critical for personnel safety.
In mining equipment, the earth conductors serve multiple functions: they provide a low-resistance path for fault currents, enable effective operation of ground fault protection systems, and help dissipate static charges that can accumulate on mobile equipment. The direct contact between earth conductors and the outer sheath ensures that the equipment frame remains at ground potential even if mechanical damage occurs to the cable.
Whilst physical damage to earth conductors does affect the cable's performance and should be repaired promptly, the interstitial design reduces the likelihood of simultaneous damage to multiple earth paths, maintaining some level of protection even under adverse conditions.
Moisture and Water Ingress
Underground mining operations frequently involve significant water challenges, from groundwater seepage to washdown operations for dust control. The cable's construction must prevent water ingress whilst maintaining flexibility and mechanical durability.
The elastomer sheath provides the primary barrier against moisture ingress, but the cable's design also minimises the consequences of any water that does penetrate the outer protection. The semiconductive layers help prevent water from creating preferential electrical conduction paths, whilst the intimate contact between earth conductors and the sheath provides multiple drainage paths for any moisture that does enter the cable.
Installation and Handling Best Practices
Proper installation represents a critical factor in cable performance and longevity. The VDE standards referenced in the cable specification provide detailed guidance on installation practices, but several key principles deserve emphasis.
Strain relief at cable terminations is absolutely essential because the cable will experience significant mechanical loading during operation. Without proper strain relief, mechanical stresses concentrate at the termination points, leading to premature failure. Cable routing should avoid sharp bends, particularly when the cable is under tension, as these create stress concentrations that can lead to conductor fatigue or insulation damage.
During installation, protection from mechanical damage is crucial. Even though the cable is designed for harsh service, unnecessary abuse during installation can compromise its long-term reliability. This includes avoiding dragging the cable over sharp edges, using proper pulling techniques to avoid overstressing the conductors, and ensuring that cable supports are adequate to prevent excessive sagging or stress concentration.
The Engineering Achievement in Context
The (N)TSCGEWÖU-(SB) mining cable represents more than just a robust electrical connection—it embodies decades of engineering refinement aimed at meeting the unique challenges of extractive industries. In Australia's mining sector, where equipment downtime can cost thousands of dollars per hour and safety is paramount, the reliability of electrical infrastructure becomes a critical competitive advantage.
The cable's design reflects a deep understanding of the operational realities facing mining operations: the need for mobility without sacrificing electrical performance, the requirement for chemical and mechanical resistance without compromising flexibility, and the imperative to maintain safety standards in environments where conventional electrical equipment simply cannot survive.
From the red dirt of the Pilbara to the deep shafts of Victorian gold mines, cables like the (N)TSCGEWÖU-(SB) enable the extraction of resources that underpin Australia's economy. Their robust construction, comprehensive testing, and compliance with international standards ensure that Australia's mining operations can continue to operate safely and efficiently, regardless of the environmental challenges they face.
The ongoing evolution of mining technology, from autonomous haul trucks to remote-controlled equipment, will undoubtedly create new challenges for cable design and application. However, the fundamental engineering principles embodied in cables like the (N)TSCGEWÖU-(SB)—robust construction, environmental resistance, and operational flexibility—will continue to serve as the foundation for powering the machinery that extracts the resources essential to modern civilisation.
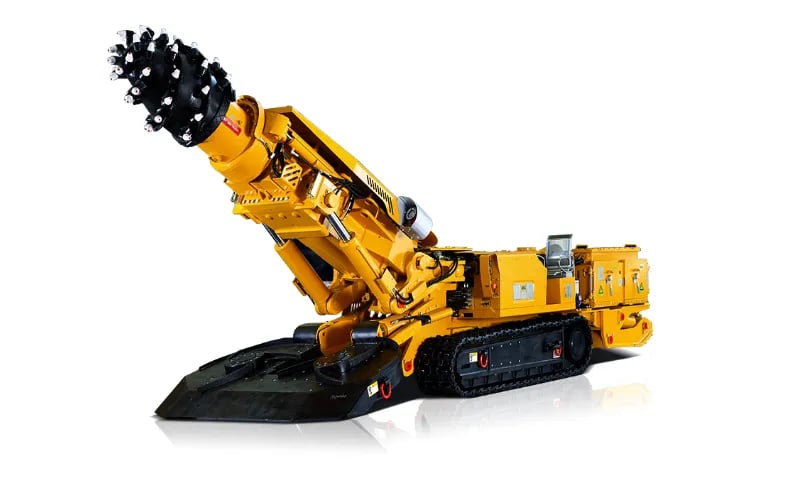
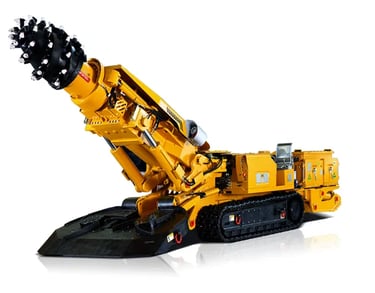